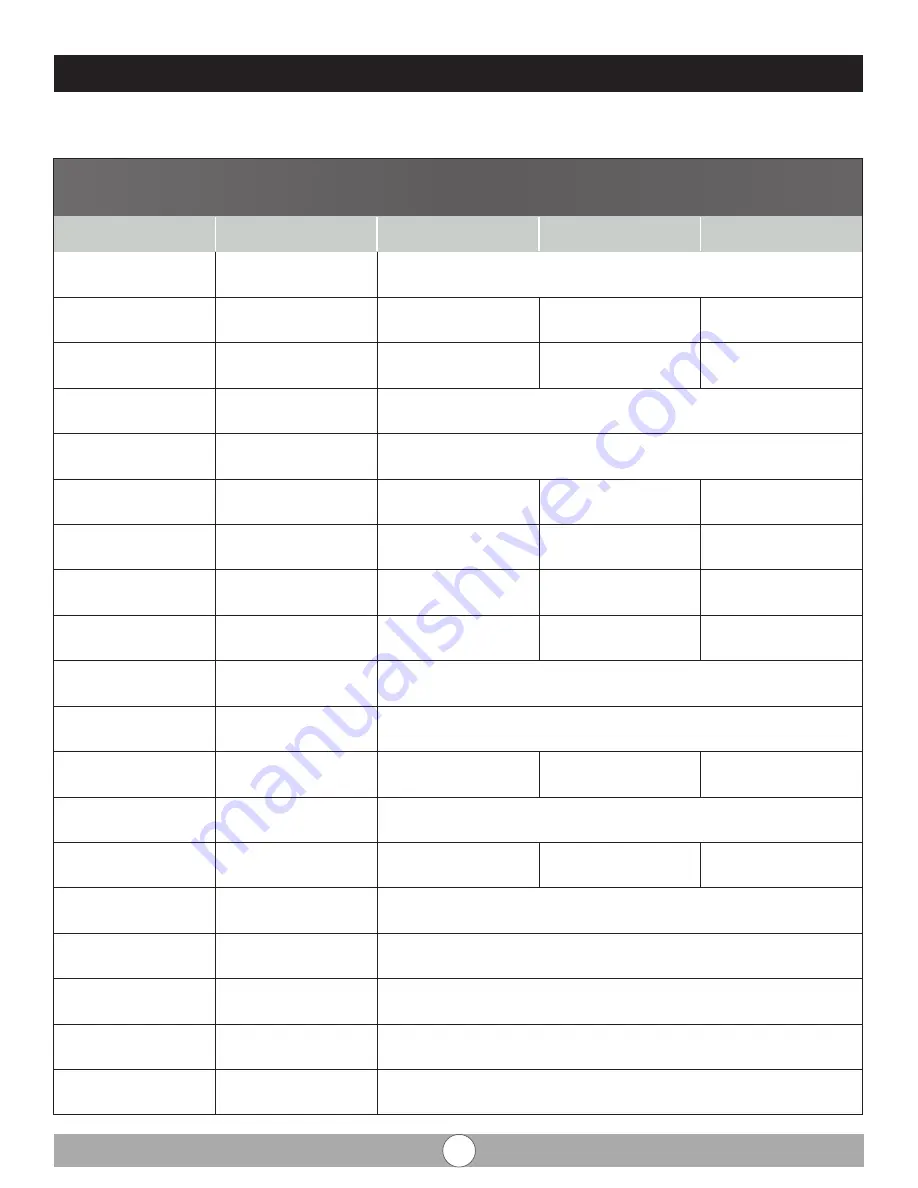
EPA Series -
Installation and Operation Manual
16
EnerPro Boiler-EPA Series-
IOM
EPA/EPAW Boiler Model
Item
Unit
1050
1600
2080
Firing Sequence
Fully modulating
Min. Fuel Input
MBH
105
160
208
Max. Fuel Input
MBH
1,050
1,600
2,080
Thermal Efficiency
%
Up to 98
Fuel Type
Type
Natural Gas
Vent Connection
Inch
6
8
10
Condensate Drain
Connection
Inch
1¼
1¼
1¼
Water Return
Inch
2
1/2
” F
2
1/2
” F
3” F
Water Supply
Inch
2
1/2
” F
2
1/2
” F
3” F
ASME MAWP
psig
160 psig
Max. Water Temp.
Safety Limit
F°/°C
200/93.3
Water Capacity
US Gal/L
51/194
66/248
77/290
Max. Flue Gas Temp.
F°/°C
230/110
Total Weight
lbs/kg
1,240/562
1,750/795
1,980/899
Control Voltage
V/P/H
110/1/60
Blower Voltage
V/P/H
110/1/60
NO
x Emmissions
ppm
<30
Control System
-
Honeywell Sola
Supply Gas Pressure
Inch of Water Column
3.5”-14” wc (Honeywell gas valve) 3.5”-20” wc Dungs Gas Valve
4.4.4 Boiler Technical Specifications
Summary of Contents for EPA1050
Page 40: ...EPA Series Installation and Operation Manual 40 EnerPro Boiler EPA Series IOM...
Page 41: ...EPA Series Installation and Operation Manual 41 EnerPro Boiler EPA Series IOM...
Page 42: ...EPA Series Installation and Operation Manual 42 EnerPro Boiler EPA Series IOM...
Page 43: ...EPA Series Installation and Operation Manual 43 EnerPro Boiler EPA Series IOM...
Page 44: ...EPA Series Installation and Operation Manual 44 EnerPro Boiler EPA Series IOM...
Page 45: ...EPA Series Installation and Operation Manual 45 EnerPro Boiler EPA Series IOM...
Page 46: ...EPA Series Installation and Operation Manual 46 EnerPro Boiler EPA Series IOM...
Page 47: ...EPA Series Installation and Operation Manual 47 EnerPro Boiler EPA Series IOM...
Page 48: ...EPA Series Installation and Operation Manual 48 EnerPro Boiler EPA Series IOM...
Page 52: ...EPA Series Installation and Operation Manual 52 EnerPro Boiler EPA Series IOM...
Page 57: ...EPA Series Installation and Operation Manual 57 EnerPro Boiler EPA Series IOM...