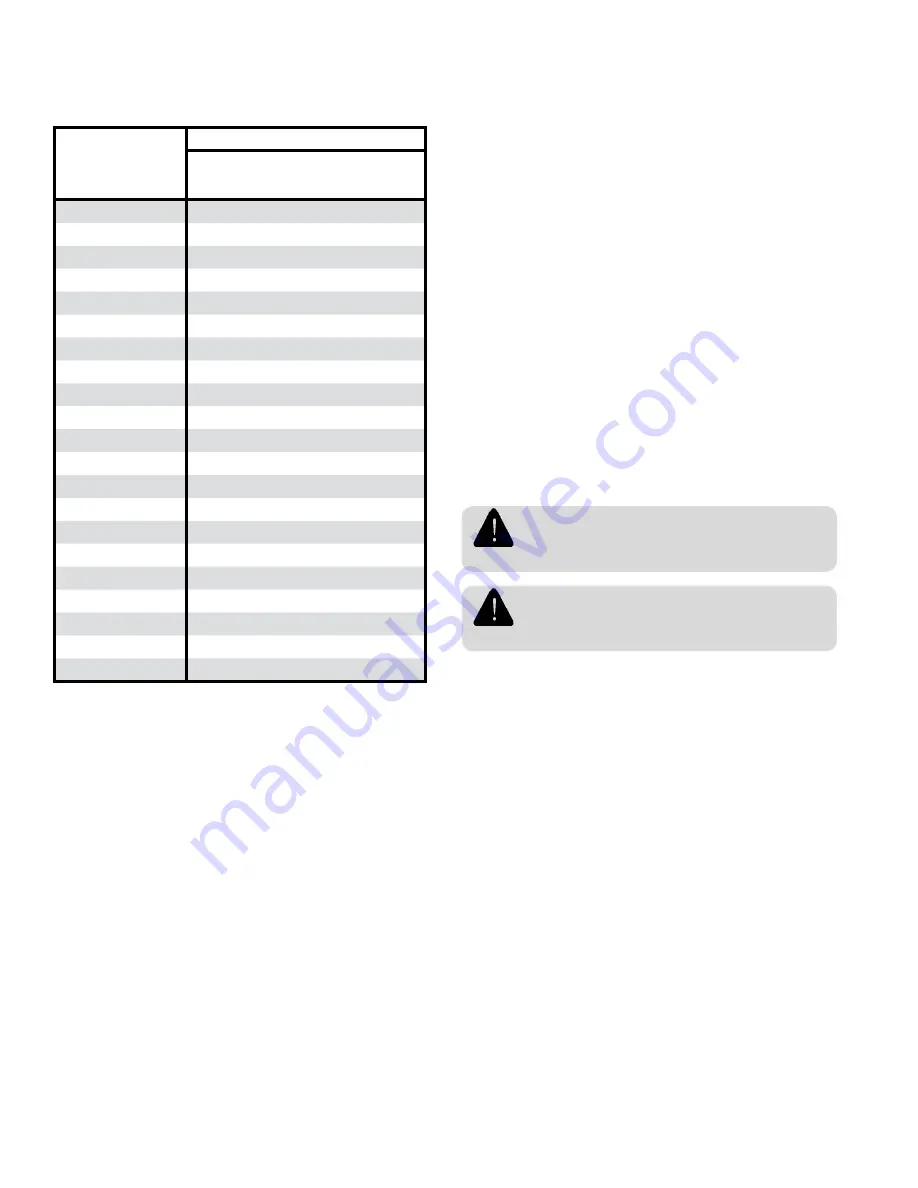
56
APPENDIX F – Adjusting Gas Input Rate (continued)
Seconds for Two
(2) Revolutions
Size of Gas Meter Dial
One-Half
Cu. Ft.
One
Cu. Ft.
Two
Cu. Ft.
24
150.0
300.0
450.0
26
138.4
276.9
415.3
28
128.5
257.1
385.7
30
120.0
240.0
360.0
34
105.8
211.7
317.6
38
94.7
189.4
284.2
42
85.7
171.4
257.1
46
78.2
156.5
234.7
50
72.0
144.0
216.0
55
65.4
130.9
196.3
60
60.0
120.0
180.0
65
55.3
110.7
166.1
70
51.4
102.8
154.2
80
45.0
90.0
135.0
90
40.0
80.0
120.0
100
36.0
72.0
108.0
120
30.0
60.0
90.0
140
25.7
51.4
77.1
160
22.5
47.0
67.5
180
20.0
40.0
60.0
200
18.0
36.0
54.0
Table F-1: Gas Flow Rate in Cu. Ft. / Hr.
less than 98% of rated input, replace or re-
drill existing main burner gas orifices:
(1)
Remove Main Burners per procedure in
Boiler Service instructions in Section (X).
(2)
Remove gas orifices. Drill each orifice
one (1) drill size larger (drill size is
stamped on orifice).
(3)
Reinstall gas orifices and main burner.
Repeat procedure to measure input rate.
15.
Recheck Main Burner Flame.
16.
Return other gas-fired appliances to
previous condition of use.
LP/Propane Gas Boilers:
1.
Follow the procedure for gas boilers, except:
2.
Adjust tank regulator for gas valve inlet
pressure of 13.5 inches w.c. or less, but not
less than 11.5 inches w.c.
3.
Gas valve has step-opening regulator, which
initially opens to 1.4 to 2.5 inches w.c. and
steps to full pressure after approximately 30
seconds. Check manifold pressure after step
has occurred.
Leak test Gas Piping:
THE BOILER AND ITS GAS
CONNECTIONS must be leak tested and
leak free before placing boiler in operation.
FOR LEAK TESTING OVER ½ PSIG,
disconnect boiler and its individual shut-
off valve from gas supply piping.
1.
For testing at ½ psig or less, isolate boiler
from gas supply piping by closing boiler’s
individual manual shut-off valve.
2.
Check for gas leaks in all piping joints,
valves, and fittings using a non-corrosive
leak detection solution or an electronic leak
detector.
3.
Repair any leaks.
Summary of Contents for ESC
Page 6: ... Figure S 1 Minimum Clearances to Combustibles SPECIFICATIONS continued ...
Page 30: ...30 Internal Wiring Figure IW 1 Wiring Diagram ...
Page 31: ...31 Internal Wiring continued Figure IW 2 Wiring Diagram ...
Page 37: ...37 APPENDIX B1 INTENTIONALLY OMITTED ...
Page 50: ...50 Figure D 0 Piping Schematic Symbols APPENDIX D System Piping continued ...
Page 62: ...62 SERVICE RECORD DATE SERVICE PERFORMED ...