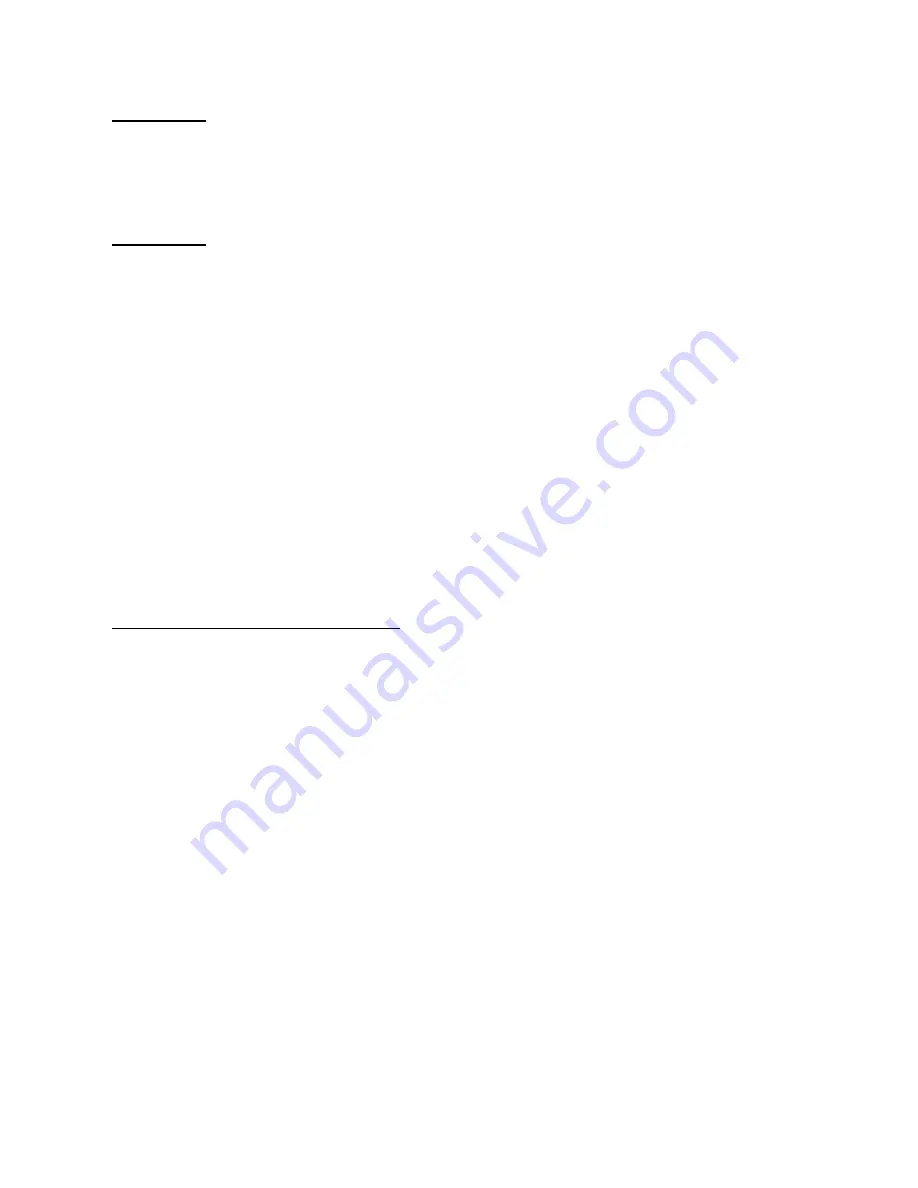
EK-Pak Owner and Installation Manual
EK-Pak Owner & Installation Manual First Edition December 2002
2
WARNING:
Have the burner/heating module started up and serviced at least once
annually by a qualified service technician. Professional care is
necessary to properly service your equipment and verify it is operating
reliably. Failure to properly maintain the equipment could result in
severe personal injury, death or substantial property damage.
WARNING:
You must keep the area around the burner/heating module free from the
following. Failure to comply could result in severe personal injury, death
or substantial property damage due to potential fire, explosion or
equipment damage from corrosive flue products.
•
Do not store or use gasoline or other flammable vapors or liquids
near or in the same room as the burner.
•
Do not use or store laundry products, paint, varnish, thinner or
other such chemicals near or in the same room as the burner/
water heater. These chemicals cause creation of acids in the
burner, heat exchanger and vent system that can cause severe
damage.
•
Do not store combustible materials near or in the same room as
the burner/heating module.
General care and maintenance
Please read through the information provided for you in this manual. Ask your
qualified service technician to explain normal operation of your equipment.
Daily inspect the space around the burner/heating module to verify the area is
clean and free of the materials listed above.
Periodically watch the operation of your burner/heating module through an
operating cycle to verify normal operation. If you notice unusual conditions or
equipment behavior, contact your qualified service technician. Follow the
instructions on the next page to shut down the burner/heating module while
waiting for the technician.