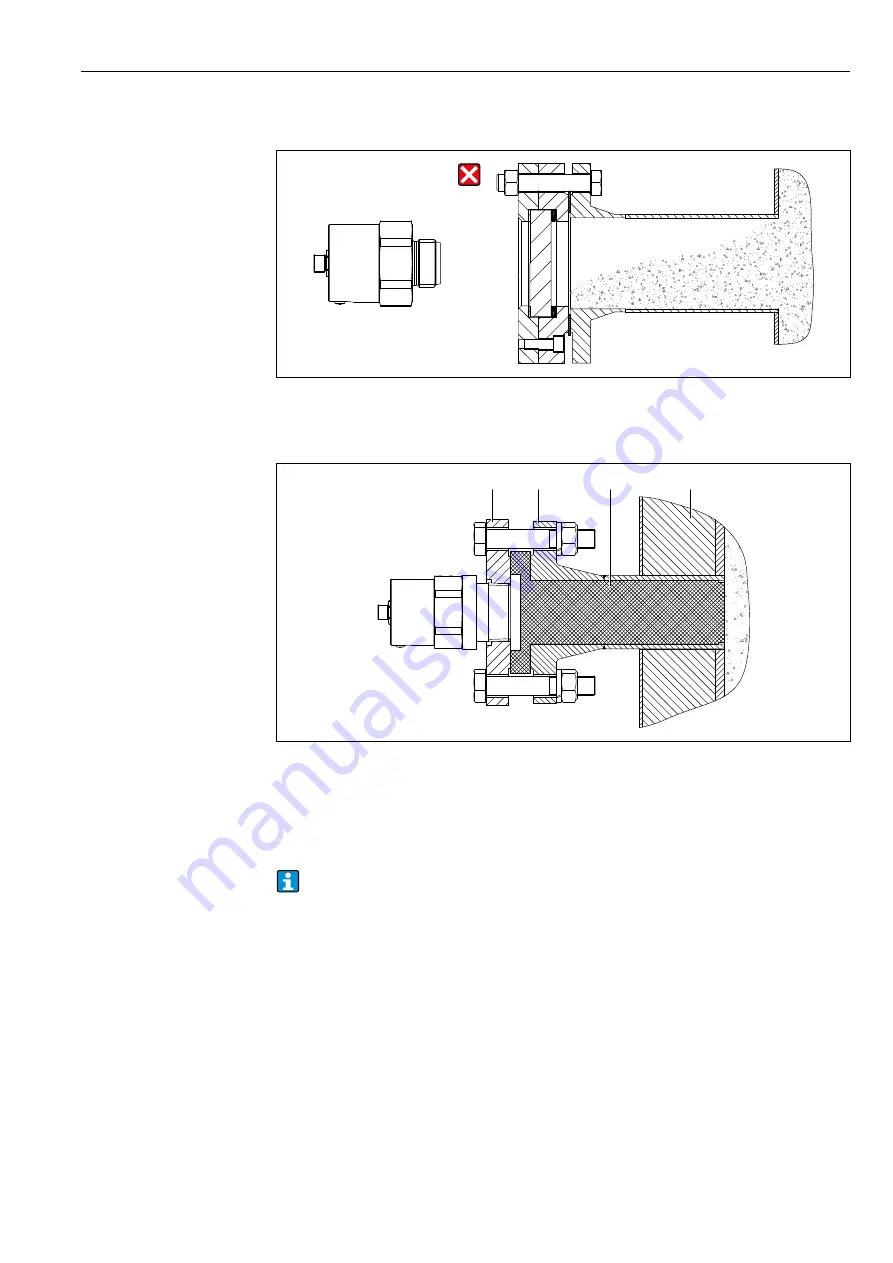
Soliwave FDR16/FQR16
Hauser
15
Mounting
Avoid material accumulation in front of the sight glass (risk of incorrect measure-
ments).
0000000024
13 Impermissible mounting with the risk of material accumulation
Mounting on process nozzle
1 2 3 4
0000000027
14 Mounting on process nozzle
1
Mounting flange
2
Process nozzle
3
Plug
4
Process insulation
• Suitable mounting flanges → 31
• Suitable plugs → 33
• Suitable process nozzle of type FAR50 → 36