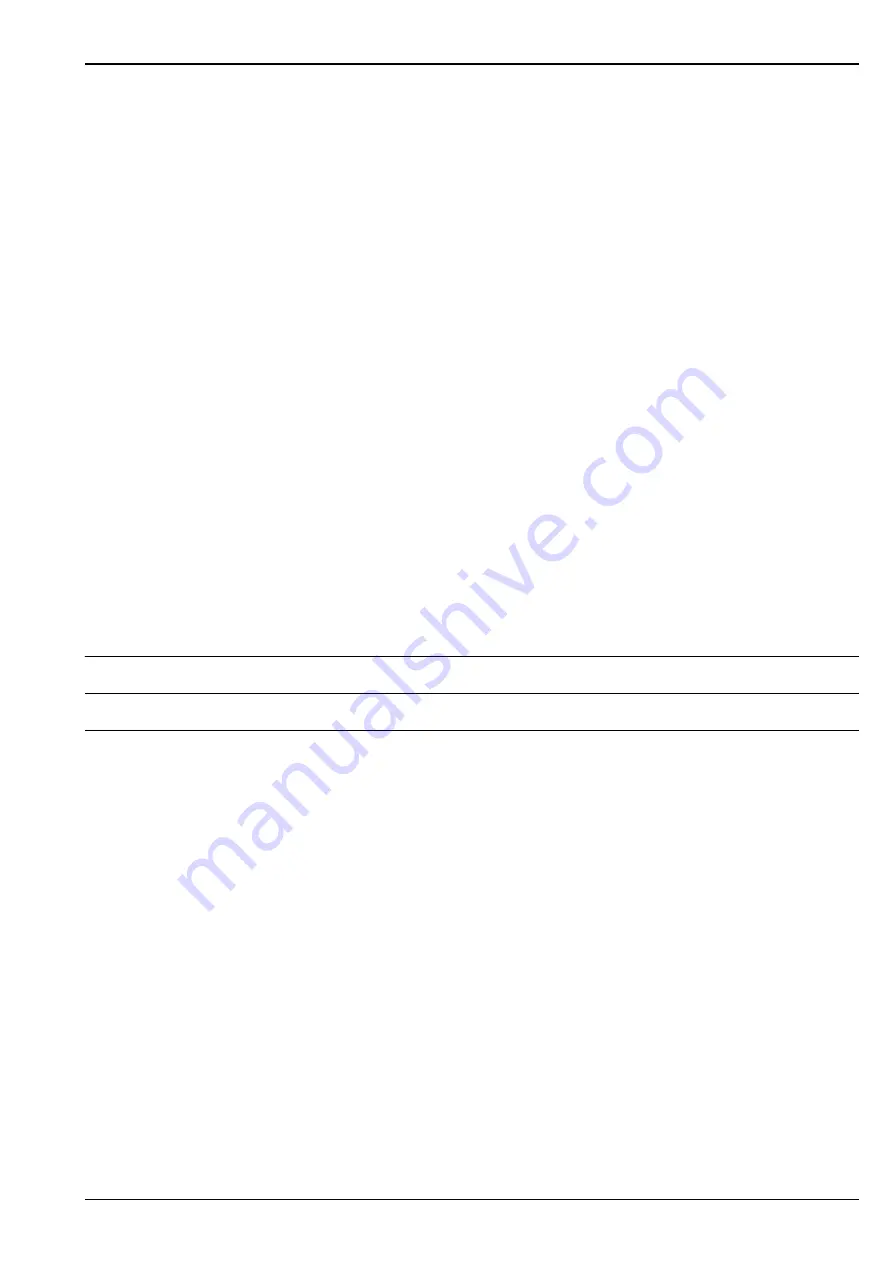
Proline Promass 80A, 83A
Hauser
19
Heating
Some fluids require suitable measures to avoid loss of heat at the sensor. Heating can be electric, e.g. with
heated elements, or by means of hot water or steam pipes made of copper or heating jackets.
"
Caution!
• Risk of electronics overheating! Make sure that the maximum permissible ambient temperature for the
transmitter is not exceeded. Consequently, make sure that the adapter between sensor and transmitter and
the connection housing of the remote version always remain free of insulating material. Note that a certain
orientation might be required, depending on the fluid temperature.
• With a fluid temperature b200 to +350 °C (+392 to +662 °F) the remote version of the high-
temperature version is preferable.
• When using electrical heat tracing whose heat is regulated using phase control or by pulse packs, it cannot
be ruled out that the measured values are influenced by magnetic fields which may occur, (i.e. at values
greater than those permitted by the EC standard (Sinus 30 A/m)). In such cases, the sensor must be
magnetically shielded.
The secondary containment can be shielded with tin plates or electric sheets without privileged direction
(e.g. V330-35A) with the following properties:
– Relative magnetic permeability
μ
r
≥
300
– Plate thickness d
≥
0.35 mm (0.014")
• Information on permissible temperature ranges
Special heating jackets which can be ordered as accessories from Hauser are available for the sensors.
Zero point adjustment
All Promass devices are calibrated to state-of-the-art technology.
The zero point determined in this way is imprinted on the nameplate of the device.
Calibration takes place under reference conditions
For this reason, Promass generally does
not
require zero point adjustment!
Experience shows that the zero point adjustment is advisable only in special cases:
• To achieve highest measuring accuracy also with very small flow rates.
• Under extreme process or operating conditions (e.g. very high process temperatures or
very high-viscosity fluids).
Inlet and outlet run
There are no installation requirements regarding inlet and outlet runs.
Length of connecting cable
max. 20 m (65 ft), remote version
System pressure
It is important to ensure that cavitation does not occur, because it would influence the oscillation of the
measuring tube. No special measures need to be taken for fluids which have properties similar to water under
normal conditions.
In the case of liquids with a low boiling point (hydrocarbons, solvents, liquefied gases) or in suction lines, it is
important to ensure that pressure does not drop below the vapour pressure and that the liquid does not start
to boil. It is also important to ensure that the gases that occur naturally in many liquids do not outgas. Such
effects can be prevented when system pressure is sufficiently high.
Consequently, it is generally best to install the sensor:
• Downstream from pumps (no risk of partial vacuum)
• At the lowest point in a vertical pipe