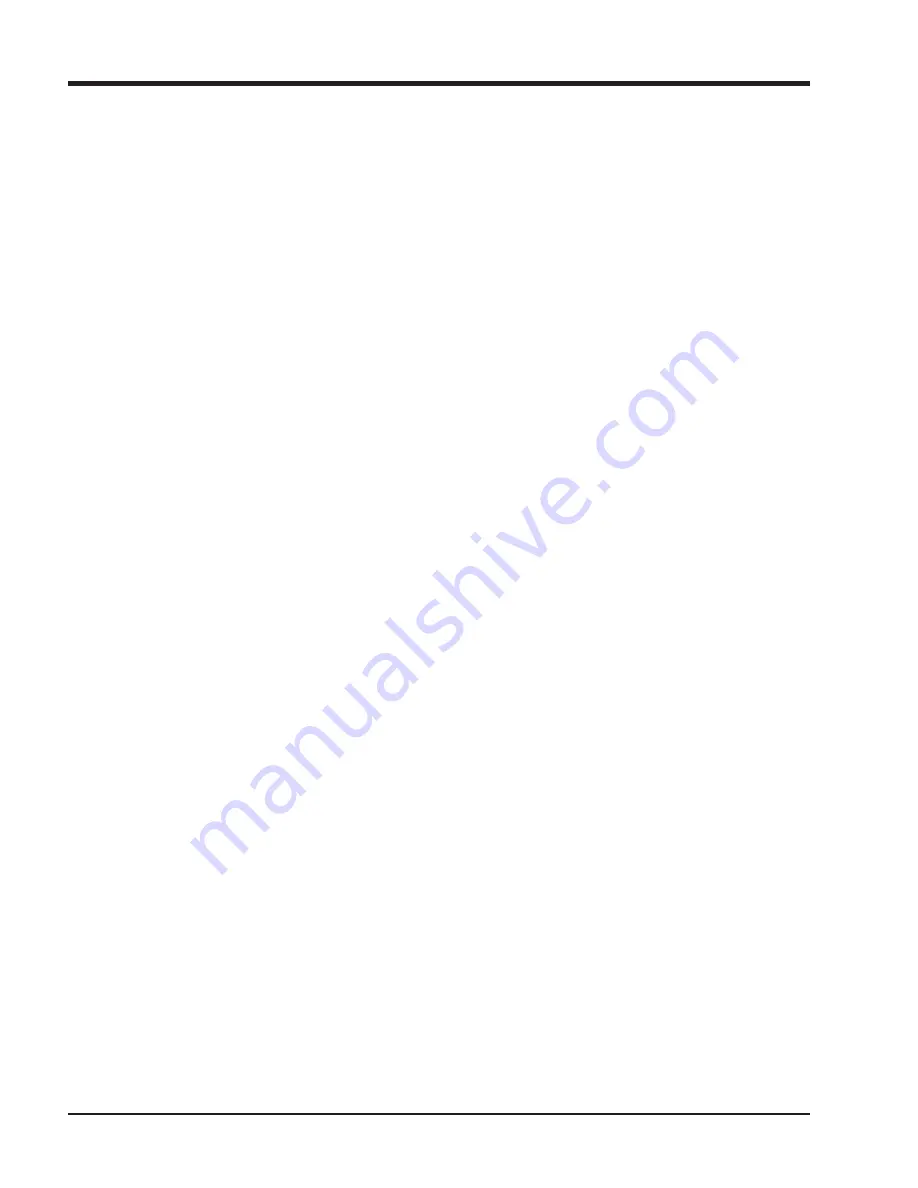
14 – 2
Vission 20/20 • Operation and Service Manual •Vilter/Emerson • 35391SC 2.0
Section 14
•
Slide Calibration
mechanical stops for normal slide travel. These soft-
ware limits purpose is to prevent the slide from actu-
ally hitting the mechanical stops which could result
in a number of undesirable consequences. By default,
the software limits are set to 150mV from either end
point. The position percentage is calculated from the
software limits. Therefore, it is possible to read a val-
ue greater than 100% or less than 0% if inertial carries
the slides after these limits are reached.
Volume Slide Valve Potentiometer
This section provided critical information and control
parameters related to the volume slide actuator. The
“% Vol” display shows the actual value in percent of the
volume slide without any conditioning that might be ap-
plied to the other volume position displays. In addition,
this section displays the value of the actuator signals in
millivolts in the “input Value” display box.
“-” Button:
• When the operator presses and holds this button,
the output associated with volume slide decreases
is energized. If the actuator does not turn in the cor-
rect direction when this button is pressed, then the
operator will have to alter how the actuator is wired
to the panel.
“+” Button:
• When the operator presses and holds this button,
the output associated with volume slide increase is
energized. If the actuator does not turn in the cor-
rect direction when this button is pressed, then the
operator will have to alter how the actuator is wired
to the panel.
Software limit setpoint:
• The Vission 20/20 uses the “Min Limit” and “Max
Limit” setpoint to de
fi
ne an area within the mechani-
cal stops for normal slide travel. These software limits
purpose is to prevent the slide from actually hitting
the mechanical stops which could result in a number
of undesirable consequences. By default, the soft-
ware limits are set to 150mV from either end point.
The position percentage is calculated from the soft-
ware limits. Therefore It is possible to read a value
greater than 100% or less than 0% if inertial carries
the slides after these limits are reached.
Slide Valve Operation
The slide valve actuator is a gear-motor with a position
sensor. The motor is powered in the forward and reverse
directions from the main computer in the control panel.
The position sensor tells the main computer the position
of the slide valve. The main computer uses the position
and process information to decide where to move the
slide valve next.
During calibration, the position sensor records the high
and low count of motor turns. The operator tells the
position sensor when the actuator is at the high or low
position with the push button. Refer to the calibration
instructions for the detailed calibration procedure.
The position sensor can get “lost” if the motor is moved
while the position sensor is not powered. To prevent
this, the motor can only be moved electrically while
the position sensor is powered. When the position sen-
sor loses power, power is cut to the motor. A capaci-
tor stores enough energy to keep the position sensor
circuitry alive long enough for the motor to come to a
complete stop and then save the motor position to non-
volatile EEPROM memory. When power is restored, the
saved motor position is read from EEPROM memory and
the actuators resumes normal function This scheme is
not foolproof. If the motor is moved manually while the
power is off or the motor brake has failed, allowing the
motor to free wheel for too long after the position sensor
loses power, the actuator will lose its calibrated position.
A brake failure can sometimes be detected by the po-
sition sensor. If the motor never stops turning after a
power loss, the position sensor detects this, knows it will
be lost, and goes immediately into calibrate mode when
power is restored.
Summary of Contents for Vission 20/20
Page 1: ...Vission 20 20 micro controller Operation and service manual Version 2 0 ...
Page 2: ......
Page 4: ......
Page 6: ......
Page 66: ...8 4 Blank Vission 20 20 Operation and Service Manual Vilter Emerson 35391SC 2 0 ...
Page 76: ...10 8 Blank Vission 20 20 Operation and Service Manual Vilter Emerson 35391SC 2 0 ...
Page 86: ...12 6 Blank Vission 20 20 Operation and Service Manual Vilter Emerson 35391SC 2 0 ...
Page 106: ...15 4 Blank Vission 20 20 Operation and Service Manual Vilter Emerson 35391SC 1 9 ...
Page 108: ...16 2 Blank Vission 20 20 Operation and Service Manual Vilter Emerson 35391SC 2 0 ...
Page 136: ...21 4 Blank Vission 20 20 Operation and Service Manual Vilter Emerson 35391SC 2 0 ...
Page 146: ...24 4 Blank Vission 20 20 Operation and Service Manual Vilter Emerson 35391SC 2 0 ...
Page 154: ...26 4 Blank Vission 20 20 Operation and Service Manual Vilter Emerson 35391SC 2 0 ...
Page 156: ...A 2 Blank Vission 20 20 Operation and Service Manual Vilter Emerson 35391SC 2 0 ...
Page 158: ...B 2 Blank Vission 20 20 Operation and Service Manual Vilter Emerson 35391SC 2 0 ...
Page 162: ...B 6 Blank Vission 20 20 Operation and Service Manual Vilter Emerson 35391SC 2 0 ...
Page 180: ...B 24 Blank Vission 20 20 Operation and Service Manual Vilter Emerson 35391SC 2 0 ...
Page 204: ...B 48 Blank Vission 20 20 Operation and Service Manual Vilter Emerson 35391SC 2 0 ...
Page 220: ...B 64 Blank Vission 20 20 Operation and Service Manual Vilter Emerson 35391SC 2 0 ...
Page 257: ......