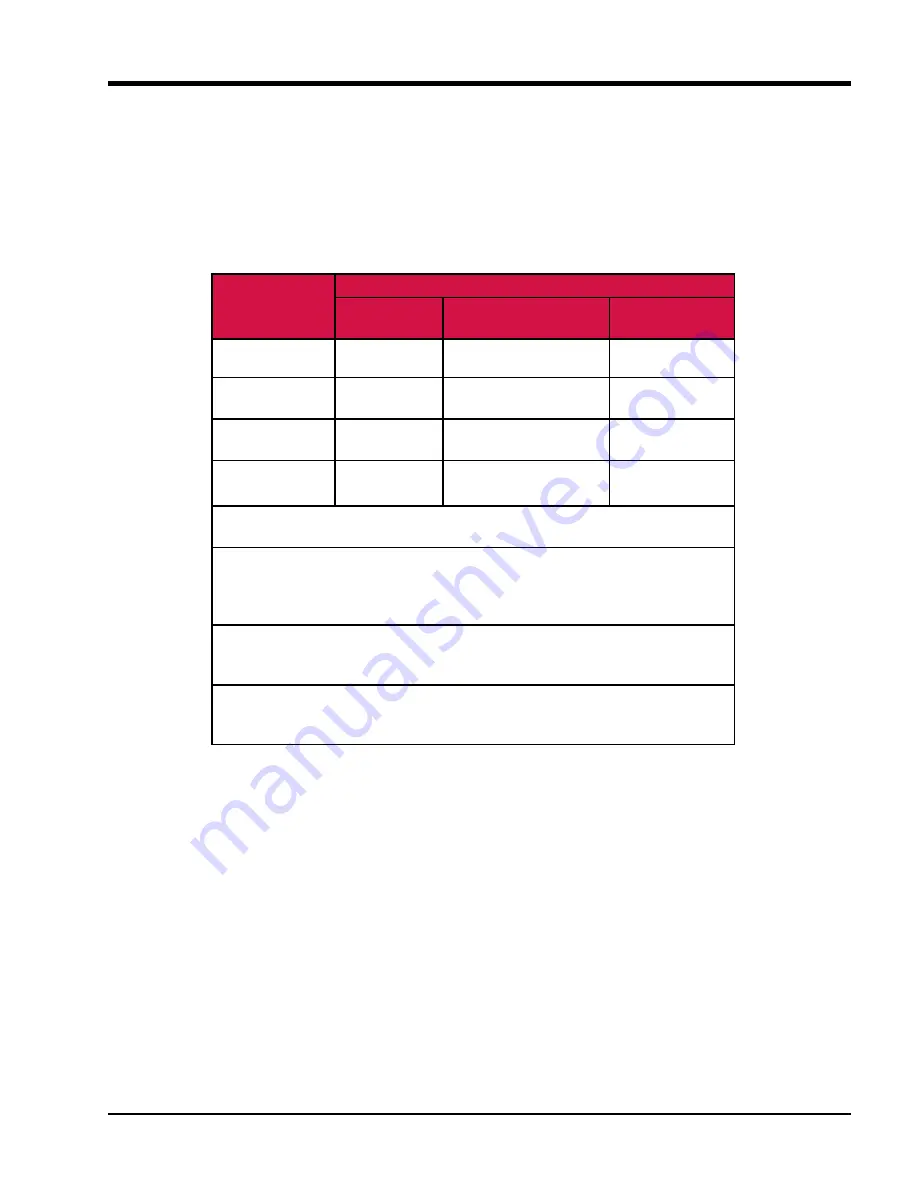
i
HPLD Single Screw Compressor • Installation, Operation and Service Manual • Emerson • 35391HP
What is covered & how long it is covered
: Subject to the other terms of this Warranty Statement, Seller warrants to its
direct purchasers (and to no others) that the Products it manufactures will be free from defects in material and work-
manship under normal use, regular service and maintenance. This warranty only applies when such defect appears
in the Products within 12 months (“m”) from the date such Products are placed in service and when such Products
are returned to and received by Seller within 18m from the date of manufacture by Seller (“12m/18m”), except that
defects in the following Products different than 12m/18m are covered by the number of months indicated below if
returned to Seller within the following number of months (“m Ship”) from shipment by Seller—
What is not covered:
This warranty does not extend to any losses or damages due to misuse; corrosion; accident;
abuse; neglect; normal wear and tear; negligence (other than Seller’s); unauthorized alteration; use beyond rated ca-
pacity; acts of God; war or terrorism; unsuitable power sources or environmental conditions; operation with refrigera-
tion or lubricants which are not suitable for use with the Product; improper installation, repair, handling, maintenance
or application; substitution of parts not approved by Seller; or any other cause not the fault of Seller. This warranty is
only applicable to Products properly maintained and used according to Seller’s instructions, the use of genuine Vilter™
replacement parts and recommended oil in all repairs, and when Buyer has demonstrated adherence to a scheduled
maintenance program as detailed in the applicable operating manual. The Buyer must use Vilter approved oil only and
provide oil analysis results to Vilter. To the extent the Buyer has supplied specifications, information, representation of
operating conditions or other data to Seller in the selection or design of the Products and the preparation of Seller’s
quotation, and in the event that actual operating conditions or other conditions differ from those represented by
Buyer, any warranties or other provisions contained herein which are affected by such conditions will be null and void.
Seller does not warrant that the Products comply with any particular law or regulation not explicitly provided in the
Product specifications, and Buyer is responsible for ensuring that the Products contain all features necessary to safely
perform in Buyer’s and its customers’ plants and operations. If the Products are for a gas compression application,
this warranty does not apply if the Products are operated in conjunction with a gas with an H
2
S level above 100 PPM.
Product
Compressor Type
Reciprocating
Compressors
VSS / VSM Refrigeration
Compressors
VSG / VSSG Gas
Compressors
New Unit
24m Ship
24m Ship
12m/18m
Compressor
(New Unit Only)
24m Ship
60m Ship
12m/18m
New Bareshaft
Compressor
24m Ship
24m Ship
12m/18m
Remanufactured
Compressor
12m/18m
12m/18m
12m/18m
Any Engineered to Order (ETO) packaged system (including Heat Pumps and
Process Chillers) not described above carry the 12m/18m warranty.
VSS / VSM single screw compressors installed and shipped on New Units carry
an internal Product component warranty of 5 years from shipment date and a
warranty of 15 years from shipment date for compressor bearings only. Does
not include actuator motors and shaft seals.
Vilter™ Genuine OEM Parts, retrofit Vission 20/20 panels, retrofit PLC panels and
any other supplied equipment not described above carry a 12m warranty from
shipment date.
New Vapor Recovery Units (“VRU Units”) and its Compressors carry the stan-
dard 12m/18m warranty—all other VRU parts carry a 6 m warranty from ship-
ment date.
Standard VILTER™ Warranty Statement
Summary of Contents for Vilter VSG128
Page 1: ...HPLD Single Screw Bare Shaft Compressor Installation Operation and Service Manual ...
Page 2: ......
Page 32: ...3 8 Blank HPLD Compressor Unit Installation Operation and Maintenance Manual Emerson 35391HPU ...
Page 68: ...6 4 Blank HPLD Compressor Unit Installation Operation and Maintenance Manual Emerson 35391HPU ...
Page 72: ...7 4 Blank HPLD Compressor Unit Installation Operation and Maintenance Manual Emerson 35391HPU ...
Page 78: ...8 6 Blank HPLD Compressor Unit Installation Operation and Maintenance Manual Emerson 35391HPU ...
Page 83: ......