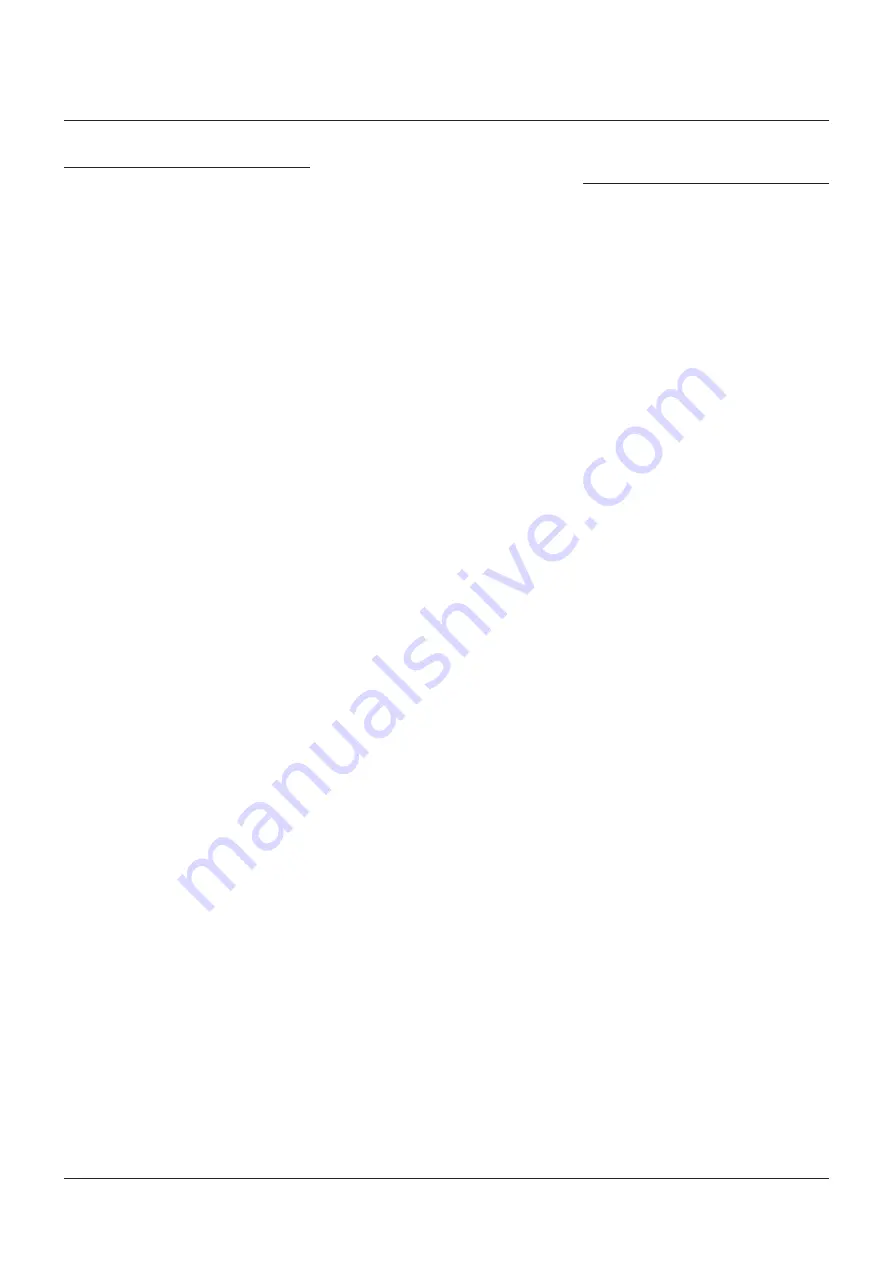
5
CAUTION
Whenever the cover is removed and reinstalled,
the end of the pallet stem must engage the stem
guide chamber in the cover for proper seating and
valve operation.
INSTALLATION (PLACING INTO SERVICE)
3600B and 3650B Series relief valves must be
mated with the appropriate flange(s). The nozzle
must be plumb (top mounted) or level (side
mounted) and the inlet flange face level (top
mounted) or plumb (side mounted) to ensure
proper operation of the relief valve.
1. remove the valve from the shipping
container. check to see if extra
loading weights were bagged and
packed separately.
2. remove the cover, cover gasket and all
packing material above the pallet and within
the valve.
3. To load pallet weights perform the following:
a. remove pallet assembly from body.
b. remove grip ring from pallet stem.
c. Non-variable setting: locate weight
marked “vacuum” and place on top
of compensating weight and/or pallet.
Secure with grip ring.
Note
: if setting is less than 2” Wc, weight
will be pre-loaded on the pallet.
d. variable setting: each lead weight
is calibrated from 1” Wc increment.
(increments of ¼” Wc and ½” Wc may be
supplied on special order). Those weights
necessary for the initial specified setting
will be tagged separately from any extra
weight provided. remove the packaging
on the weights tagged for the initial
specified setting and place the weights
on top of the pallet. Secure with grip ring.
Store remaining weights for future use (in
case the setting needs to be increased).
e. Weigh entire pallet assembly (including
installed weights). using the applicable
calibration table, confirm that the
assembly is the proper weight to achieve
the required setting. allowable weight
tolerance is +5%, -5%.
f. remove any remaining packing material
from valve body. Wipe seat ring, guide
posts and pallet assembly with a soft cloth
to remove any material which could affect
valve operation.
g. place pallet assembly on valve body seat.
ensure that pallet moves freely within
guide posts and rests flat on the seat ring.
h. replace the cover gasket and cover.
Tighten cover screws uniformly.
CAUTION
The end of the pallet stem must engage the stem
guide chamber in the cover for proper seating and
valve operation.
4. place the valve in a level position. check the
pallet operation on model 3600B by using a
non-sparking tool which will pass through
the center of the mesh screen. push up on
the pallet, then lower it onto the seat. pallet
should move freely and rest flat on the
seat ring.
5. With valve in level position, check the
pallet operation on model 3650B. reach
up through the bottom flange opening and
carefully push up on the pallet, then lower it
onto the seat. pallet should move freely and
rest flat on the seat ring.
6. mount the valve on the flanged nozzle or
flame arrester using the appropriate full
faced gasket.
NOTE
it is recommended that steel valves be given a coat
of paint immediately after installation is completed.
apply paint to external surfaces only.
CAUTION
DO NOT MATE A FLAT FACE FLANGE TO A
RAISED FACE FLANGE.
If it is necessary to mate a flat face flange with
a raised face flange, use the proper spacer to
convert the raised face to a flat face.
7. verify that the valve is level to permit proper
operation of the pallet. install mounting
hardware and tighten uniformly.
8. for model 3650B Series pressure relief
valve, install connecting piping (if required)
to outlet flange. use a full faced gasket and
tighten all mounting hardware uniformly.
MAINTENANCE (ASSEMBLING
AND DISMANTLING)
The valve should be inspected and cleaned
at periodic intervals. The first inspection
should be made approximately 30 days after
commissioning. Subsequent inspections should
be made every 30 days. The user may adjust the
schedule for his own convenience and safety,
depending upon the product being stored.
WARNING
• Relief valve must be isolated from tank pressure
before servicing. All gas must be blocked
and pressure safely vented. If no isolation
valve is present, carefully open vacuum cover
or lift pressure pallet, allowing pressure
to vent slowly.
• Wear appropriate gloves and/or breathing
apparatus if hazardous vapors are present.
1. To inspect the valve proceed as follows:
a. remove cover and then pallet assembly.
b. inspect pallet inserts for ripples, tears,
or nicks, as well as seating surfaces for
debris, abrasion or pitting. pallet edges
and guide posts should be free or burrs,
corrosion or other obvious damage.
clean all components, replacing any
showing excess wear or damage. on
the “all-Weather” versions, inspect the
Teflon coating for any damage that would
affect operation.
c. reassemble in reverse order.
CAUTION
The end of the pallet stem must engage the stem
guide chamber in the cover for proper seating and
valve operation.
VAREC
3600B/3650B SerieS preSSure or vacuum relief valveS
INSTRUCTION, OPERATION AND MAINTENANCE MANUAL