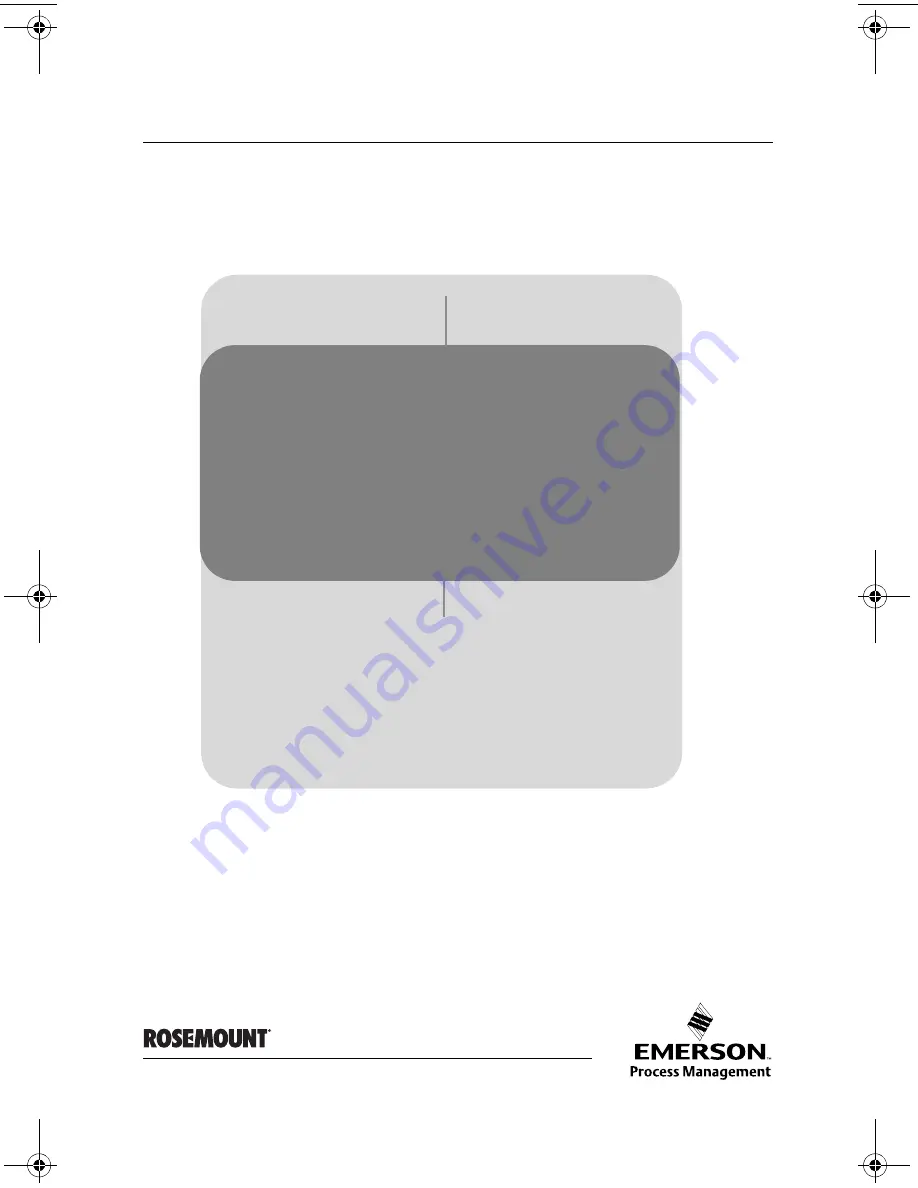
www.rosemount.com
¢00825-0100-4809[¤
Quick Installation Guide
00825-0200-4585, Rev AA
January 2009
Flanged Flo-Tap 585 Annubar
Step 1: Location and Orientation
Step 2: Weld Mounting Hardware
Step 3: Install Isolation Valve
Step 4: Mount Drilling Machine and Drill Hole
Step 5: Remove Drilling Machine
Step 6: Mount the Annubar
Step 7: Insert the Annubar
Step 8: Mount the Transmitter
Step 9: Retracting the Annubar
Product Certifications
Start
End
Rosemount 585 Annubar
®
Flanged
Flo-Tap Assembly
HART
®
4585_0200_QIG_AA.fm Page 1 Thursday, January 29, 2009 3:05 PM