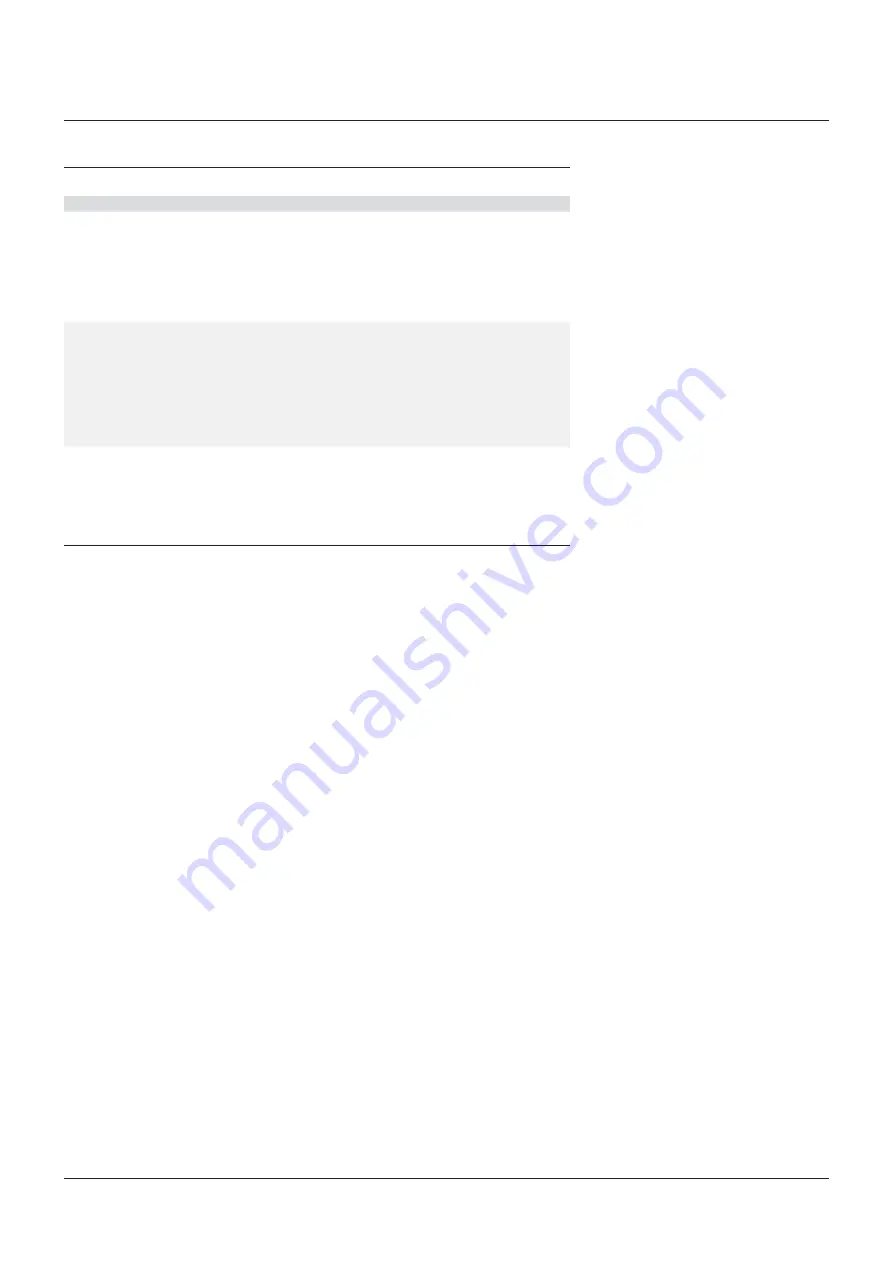
7
KTM
POWDER DISCHARGE SYSTEM (PDS) METALTITE
®
BALL VALVES
INSTALLATION, OPERATION AND MAINTENANCE INSTRUCTIONS
Trouble examples
Causes
Measures
Unsmooth operation
1. Jamming due to solids or slurry in the
fluid.
1. Clean the inside of the valve.
If necessary, replace parts (ball,
seats, stem bearing, thrust bearing).
2. Fluid sticks to ball and seats.
2. Clean the inside of the valve.
If necessary, replace ball or seats.
3. Unusual pressure rise exceeding seat
rating limit when shutting the valve.
3. Take measures to prevent abnormal
pressure rise in pipe.
Outside leakage
1. Sealing performance of gasket and
gland packing decreases gradually when
operation frequency is high or the high
temperature fluid flows.
1. The fastening nuts or bolts at gasket
and gland packing are required to
be lightly tightened, or gasket and
gland packing replaced.
2. Sealing performance of gasket and gland
packing decreases when shutting the
valve during abnormal pressure rise in
the piping.
2. Take measures to prevent pressure
rise and replace seats, gaskets and
gland packing.
Seat leakage
1. Fluid sticks to ball and seats.
1. Clean the inside of the valve.
If necessary, replace ball or seats.
2. Abrasion of ball and seats.
2. Replace ball and seats.
9 TROUBLESHOOTING
10 VALVE DISASSEMBLY
Assemble/disassemble the valves in a clean, well-lit and well ventilated place.
CAUTION
Before removing the valve from the piping, ensure that the system has been fully depressurized and
any dangerous fluids have been drained off.
Failure to do so may cause serious personal injury and/or damage to the valve.
Maintenance of the valves must be performed only by qualified personnel. Never operate/disassemble
the valves before checking the safety. The valve is extremely heavy; ensure a stable position to prevent
it from falling down when assembling/disassembling.
There is a cavity inside the ball valve when a ball is fully open or fully closed. For a safe disassembly,
following instructions must be carried out.
1. Half open the valve when still installed in piping, and make sure no pressure remains in the cavity.
Failure to do so may result in injury, explosion or fire caused by the remaining pressure.
2. Before disassembling the valve, make sure that it has been decontaminated of any harmful gasses
or fluids, and disassembly is done at a well ventilated place and within a safe temperature range
for maintenance.
3. Pressure of flammable gas and other dangerous fluids must be checked only at well ventilated
places outdoors, far away from any fire source.
Refer to the following construction drawing(s) for disassembling. The numbers of parts vary
slightly depending on the valve size, but the basic structures are identical.