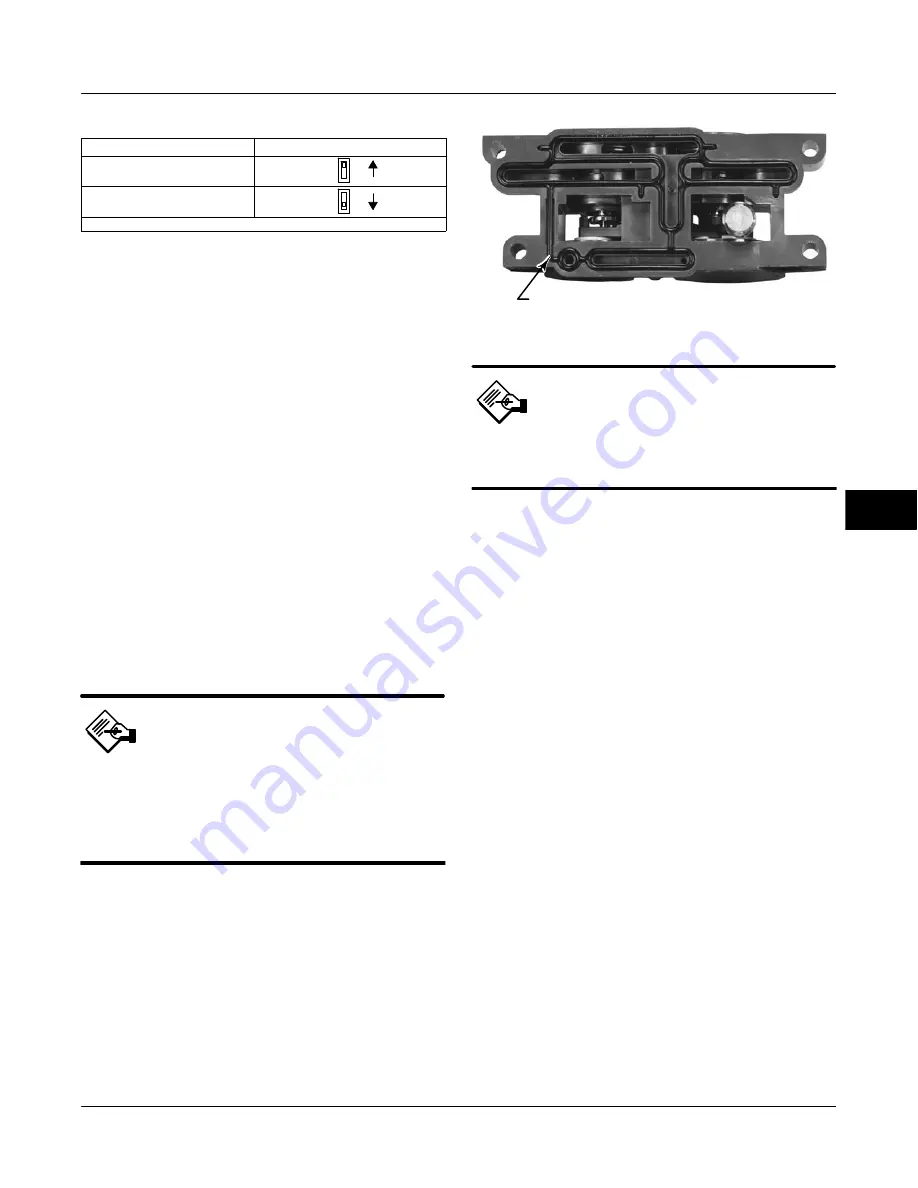
Maintenance and Troubleshooting
September 2013
7-7
Table 7-2. DIP Switch Configuration
(1)
Operational Mode
Switch Position
Multidrop Loop
UP
Point-to-Point Loop
DOWN
1. Refer to figure 7-4 for switch location.
Replacing the PWB Assembly and Setting
the DIP Switch
1. Apply silicone lubricant to the pressure sensor
O-rings (key 40) and install them on the pressure
sensor bosses in the module base assembly.
2. Properly orient the PWB assembly (key 50) as you
install it into the module base. The two electrical leads
from the I/P converter (key 41) must guide into their
receptacles in the PWB assembly and the pressure
sensor bosses on the module base must fit into their
receptacles in the PWB assembly.
3. Push the PWB assembly (key 50) into its cavity in
the module base.
4. Install and tighten three screws (key 33) to a torque
of 1 N
m (10.1 lbf
in).
5. Set the DIP switch on the PWB assembly
according to table 7-2.
Note
For the digital valve controller to
operate with a 4 to 20 mA control
signal, be sure the DIP switch is in the
point-to-point loop position, i.e.,
switch in down position.
6. Reassemble the module base to the housing by
performing the Replacing the Module Base procedure.
7. Setup and calibrate the digital valve controller.
Pneumatic Relay
Refer to figures 8-2 through 8-9 for key number
locations. The pneumatic relay (key 24) is located on
the front of the module base.
Figure 7-5. Pneumatic Relay Assembly
W8074
RELAY SEAL
Note
After relay submodule replacement,
calibrate the digital valve controller
to maintain accuracy specifications.
Removing the Pneumatic Relay
1. Loosen the four screws that attach the relay
(key 24) to the module base. These screws are
captive in the relay.
2. Remove the relay.
Replacing the Pneumatic Relay
1. Visually inspect the holes in the module base to
ensure they are clean and free of obstructions. If
cleaning is necessary, do not enlarge the holes.
2. Apply silicone lubricant to the relay seal and
position it in the grooves on the bottom of the relay as
shown in figure 7-5. Press small seal retaining tabs
into retaining slots to hold relay seal in place.
3. Position the relay (with shroud) on the module
base. Tighten the four screws, in a crisscross pattern,
to a final torque of 2 N
m (20.7 lbf
in).
4. Using the Field Communicator, verify that the value
for the parameter Relay matches the relay type
installed.
5. After replacing the relay and verifying the relay
type, calibrate travel or perform touch-up calibration to
maintain accuracy specifications
Gauges, Pipe Plugs, or Tire Valves
Depending on the options ordered, the DVC6000 will
be equipped with either gauges (key 47), pipe plugs
(key 66), or tire valves (key 67). Single-acting direct
instruments will also have a screen (key 236, figure
8-6). These are located on the top of the module base
next to the relay.
7
Summary of Contents for Fisher FIELDVUE DVC6000
Page 2: ......
Page 22: ...DVC6000 Digital Valve Controllers September 2013 1 12 1 ...
Page 82: ...DVC6000 Digital Valve Controllers September 2013 4 22 4 ...
Page 94: ...DVC6000 Digital Valve Controllers September 2013 5 12 5 ...
Page 139: ...Loop Schematics Nameplates September 2013 B 1 B B Appendix B Loop Schematics Nameplates B ...
Page 161: ......