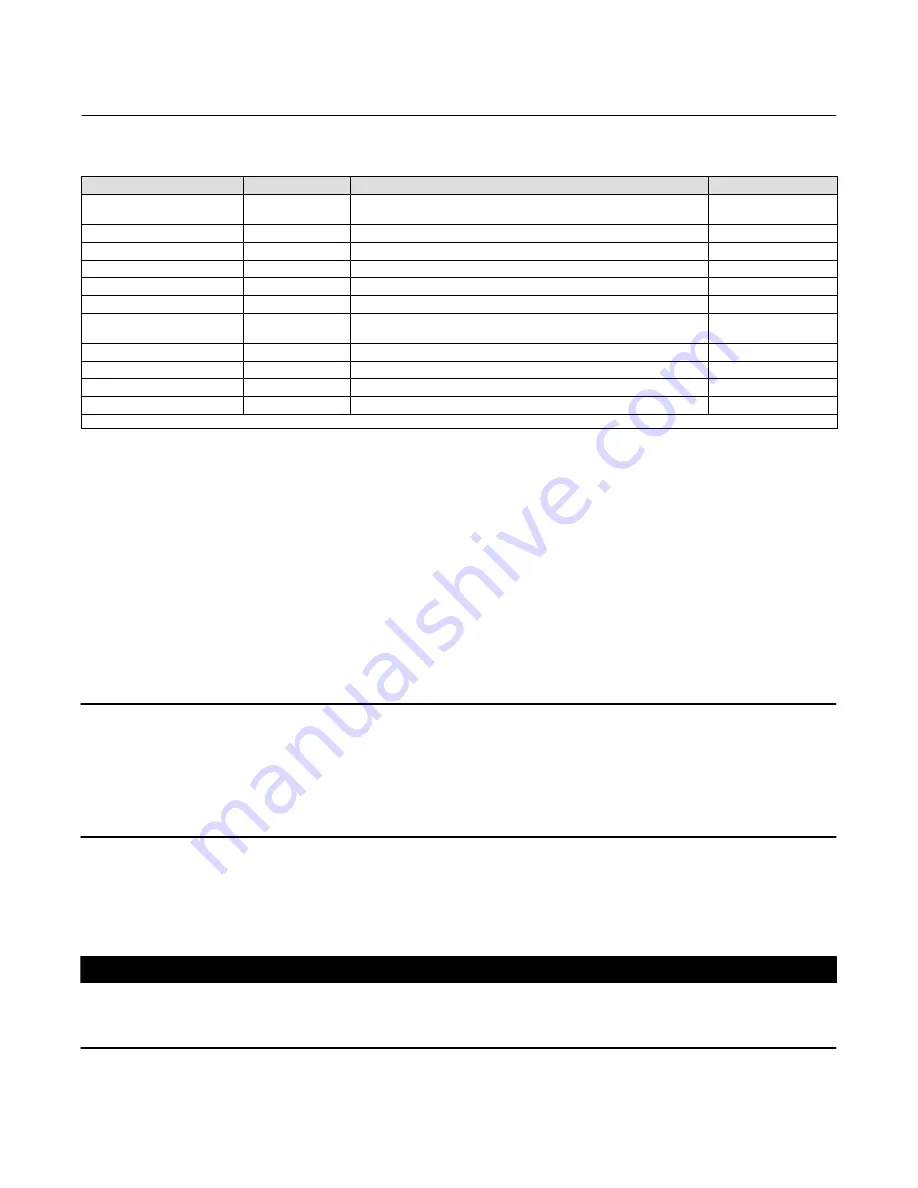
Instruction Manual
D102748X012
DLC3010 Digital Level Controller
Maintenance & Troubleshooting
May 2018
83
Table 6‐2. Tools Required
Tool
Size
Usage
Keys
Hex Key
2 mm
Handle
Cover‐lock set screws
31
20
Hex Key
2.5 mm
Small cap screws
13
Hex Key
4 mm
Lever assembly mtg cap screw
14
Hex Key
5 mm
Terminal box mtg cap screw
7
Hex Socket
10 mm
Coupling nut
76
Open‐end
13 mm
Transmitter mounting nuts
34
Phillips Screwdriver
Terminal screws
Electronics module mtg screws
25
36
Small flat blade screwdriver
LCD assy mtg screws
40
Strap wrench
Helpful for removing a display cover that has been over‐tightened
3
Large flat blade screwdriver
(1)
Flex circuit mtg screws
19
Needle nose pliers
(1)
Align/clamp ring extraction
17
1. Needed to remove a flex circuit if date code numbers are requested for warranty information.
Removing the DLC3010 Digital Level Controller from a 249 Sensor
249 Sensor in Standard Temperature Applications
1. Loosen the set screw (key 31) in the terminal box cover assembly (key 6) so that the cover can be unscrewed from
the terminal box.
2. After removing the cover (key 6), note the location of field wiring connections and disconnect the field wiring from
the wiring terminals.
3. As shown in figure 2‐4, locate the access handle on the bottom of the transducer housing. Using a 2 mm hex key,
back out the set screw in the depression on the access handle until it is flush with the handle surface. Press on the
back of the handle, as shown in the figure, and slide the handle toward the front of the unit, (the locked position), to
expose the access hole. Be sure the locking handle drops into the detent.
Note
If the access handle will not slide, the sensor linkage is most likely in an extreme position. When the lever assembly is at a hard stop
inside the housing, the locking pin on the access door may not be able to engage the mating slot in the lever assembly. This
condition can occur if the displacer has been removed, if the sensor is lying on its side, or if the instrument had been coupled to the
sensor while the displacer was not connected. To correct this condition, manipulate the sensor linkage to bring the lever assembly
to within approximately 4 degrees of the neutral position before attempting to slide the handle. A probe inserted through the top
vent of the 249 head may be required to deflect the driver rod to a position where the lever assembly is free.
5. Loosen and remove the hex nuts (key 34) from the mounting studs (key 33).
6. Carefully pull the digital level controller straight off the sensor torque tube.
CAUTION
Tilting the instrument when pulling it off of the sensor torque tube can cause the torque tube shaft to bend. To prevent
damage to the torque tube shaft, ensure that the digital level controller is level when pulling it off of the sensor torque
tube.