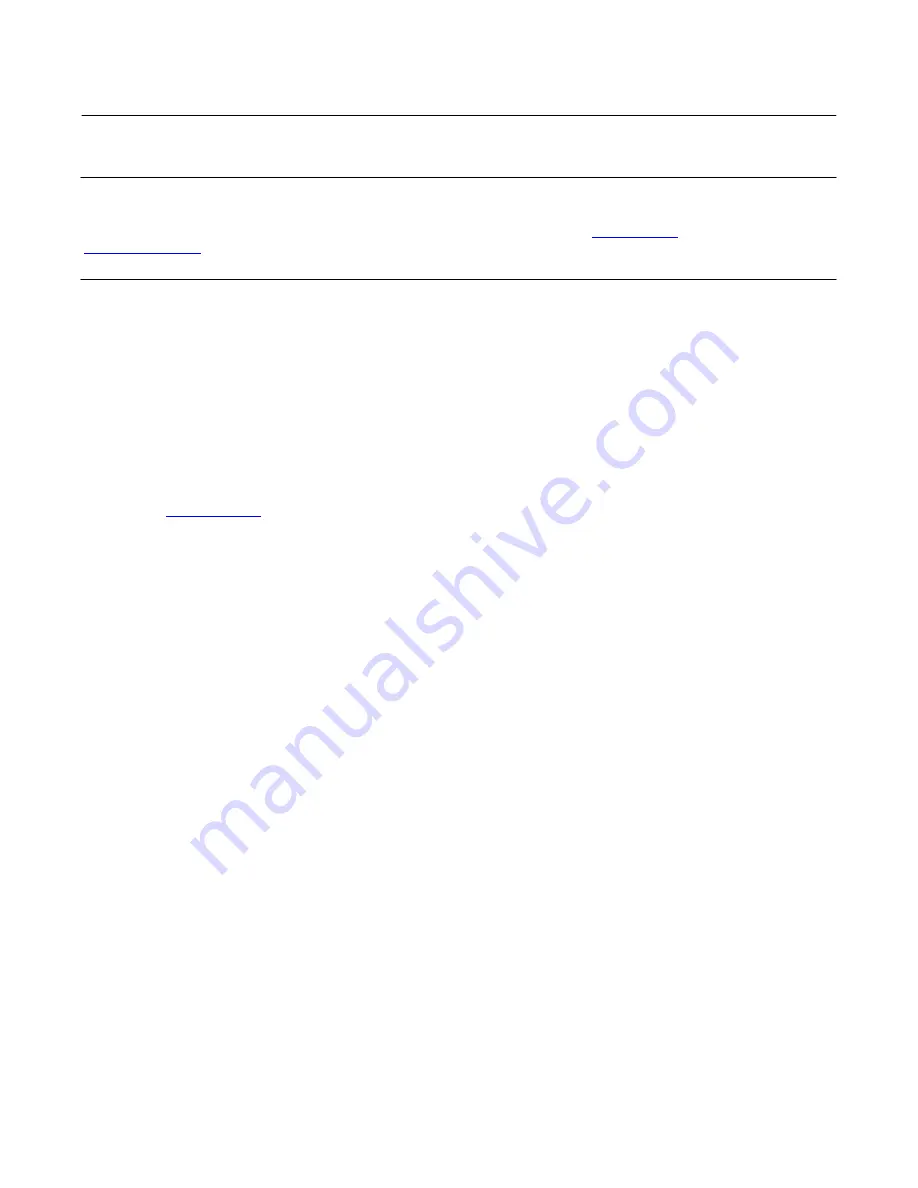
Instruction Manual
D102748X012
DLC3010 Digital Level Controller
Configuration
May 2018
68
Note
Tables containing information on temperature effects on torque tubes can be found in the Simulation of Process Conditions for
Calibration of Fisher Level Controllers and Transmitters instruction manual supplement (
or Local Business Partner, or at www.fisher.com. This document is also available in the device help files linked
to some host applications with graphical user interfaces.
6. Using a sight glass or sampling ports, obtain an estimate of the current process condition. Run the Trim Zero
calibration and report the value of the actual process in the PV engineering units.
7. You should now be able to go to automatic control. If observations over time show the instrument output exhibits,
for example,1.2 times as much excursion as the sight glass input, you could divide the stored torque tube rate by
1.2 and send the new value to the instrument. Then run another Trim Zero calibration and observe results for
another extended period to see if further iteration is required.
Entering Theoretical Torque Tube (TT) Rates
The Simulation of Process Conditions for Calibration of Fisher Level Controllers and Transmitters instruction manual
supplement (
) provides the theoretical composite torque tube (TT) rate for 249 sensors with DLC3010
controllers. These numbers are nominal values. They should be within 10% of the values that the instrument would
compute when you perform a sensor calibration. They will be less accurate for the long torque tubes (249K, L, N, VS,
and P), especially with thin‐wall constructions.
If you are unable to perform a sensor calibration during installation, you may enter the values into the instrument at
the following menu item in the handheld:
Configure > Manual Setup > Sensor > Torque Tube > Change Torque Rate (2-2-1-3-5)
If you select
Find default from nameplate data
instead of
Edit
, the procedure can look up values for commonly available
torque tubes.
Then, manually set the LRV and URV to the PV values at which you desire 4 and 20 mA output, respectively:
Configure > Manual Setup > Ranging > Upper
or
Lower Range Value (2-2-3-4 or -5)
Next, perform a
Trim Zero
operation to align the instrument output with the sight glass reading:
Configure > Calibration > Primary > Partial Calibration > Trim Zero (2-4-1-3-3)
These steps will provide an approximate PV calibration to get a system operational. Further refinements can then be
made when it is possible to manipulate and observe the level and instrument output.
Excessive Mechanical Gain
If the displacer/torque tube sizing provides more than 4.4 degrees of torque tube rotation for a full span change in
process input, It may be difficult to obtain a valid calibration with the normal coupling procedure. In such a case, you
can utilize the full mechanical span of the DLC3010 by coupling the instrument to the torque tube at the 50% travel
condition, instead of at the lowest process condition. When coupled at the 50% travel condition, the travel limits of the
249 hardware will be the constraining factor. If the 249 travel limit is reached before full process input travel is
achieved, the hardware is either improperly sized for the application, improperly assembled, or damaged.