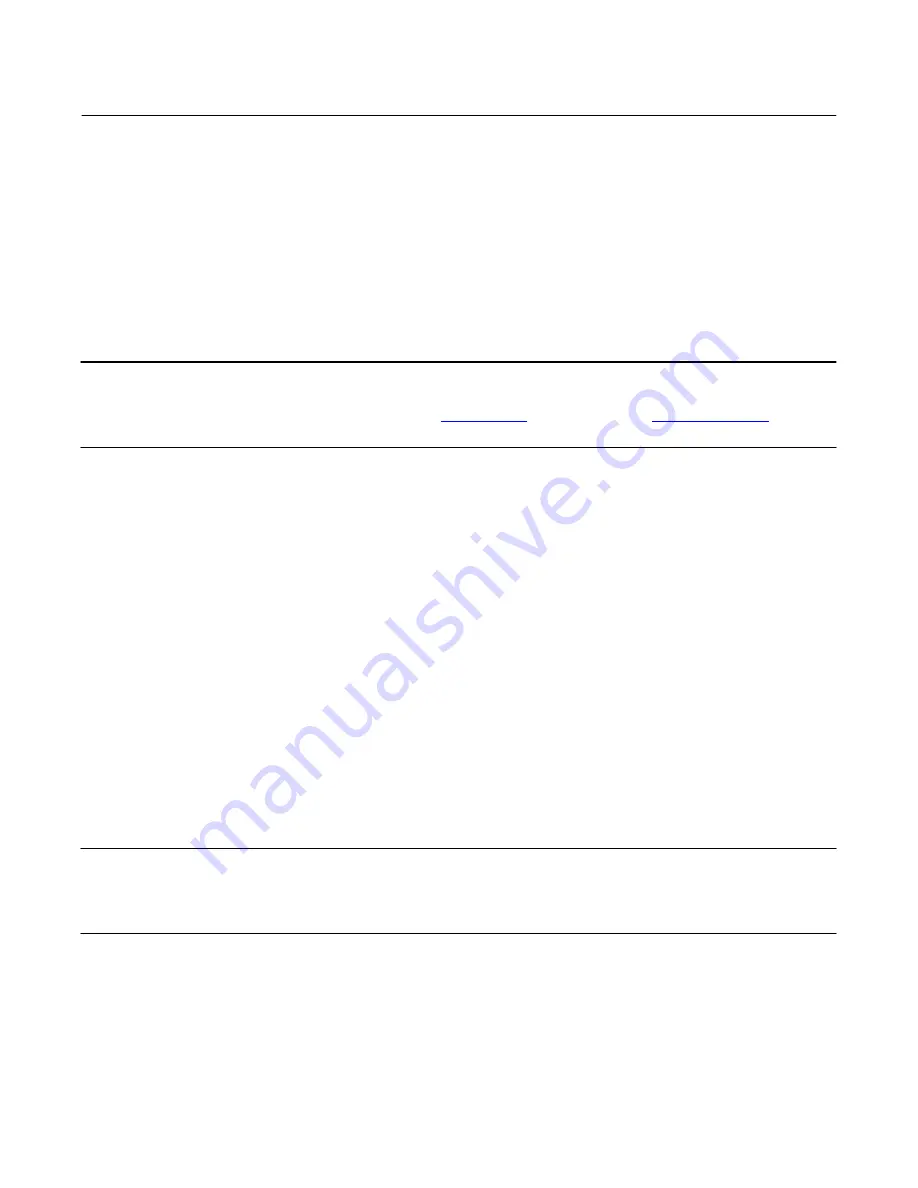
Instruction Manual
D102748X012
DLC3010 Digital Level Controller
Configuration
May 2018
66
Since you now have a valid gain:
D
Change the PV mode to Interface or Density,
D
reconfigure the fluid SGs or range values to the actual fluid values or extremes, and
D
use the Trim Zero procedure in the Partial Calibration menu to backcompute the theoretical zerobuoyancy
angle.
The last step above will align the value of the PV in engineering units to the independent observation.
Note
Information on simulating process conditions is available in the Simulation of Process Conditions for Calibration of Fisher Level
Controllers and Transmitters instruction manual supplement (
Business Partner, or at www.fisher.com.
Following are some guidelines on the use of the various sensor calibration methods when the application uses an
overweight displacer:
Weight‐based:
Use two accurately known weights between minimum and maximum buoyancy conditions. The full
displacer weight is invalid because it will put the linkage on a stop.
Min/Max:
Min now means submerged in the lightest fluid and Max means submerged in the heaviest fluid.
Two point:
Use any two interface levels that actually fall on the displacer. Accuracy is better if the levels are farther
apart. The result should be close if you can move the level even 10%.
Theoretical:
If the level cannot be changed at all, you can enter a theoretical value for torque tube rate manually, then
Trim Zero to adjust the output to the current independent observation of the process condition. Gain and bias errors
will exist with this approach, but it can provide nominal control capability. Keep records of subsequent observations of
actual process versus instrument output and different conditions and use the ratios between the process and
instrument changes to scale the torque rate value. Repeat Zero Trim after each gain change.
Density Applications - with Standard Displacer and Torque Tube
Note
When you change 'PV is' from level or interface to density, the range values will be initialized to 0.1 and 1.0 SGU. You may edit the
range values and density units after that initialization. The initialization is performed to clear out irrelevant numerical values from
length dimensions that cannot be reasonably converted to density dimensions.
Any of the full sensor calibration methods (Min/Max, Two Point, and Weight) can be used in density mode.
Min/Max:
The Min/Max Calibration first asks for the SG of your minimum density test fluid (which could be zero if the
displacer is not overweight). Then, it has you set up a completely submerged displacer condition with that fluid. Next it
asks for the SG of your maximum density test fluid and directs you to completely submerge the displacer in that fluid.
If successful, the computed torque rate and zero reference angle are displayed for reference.