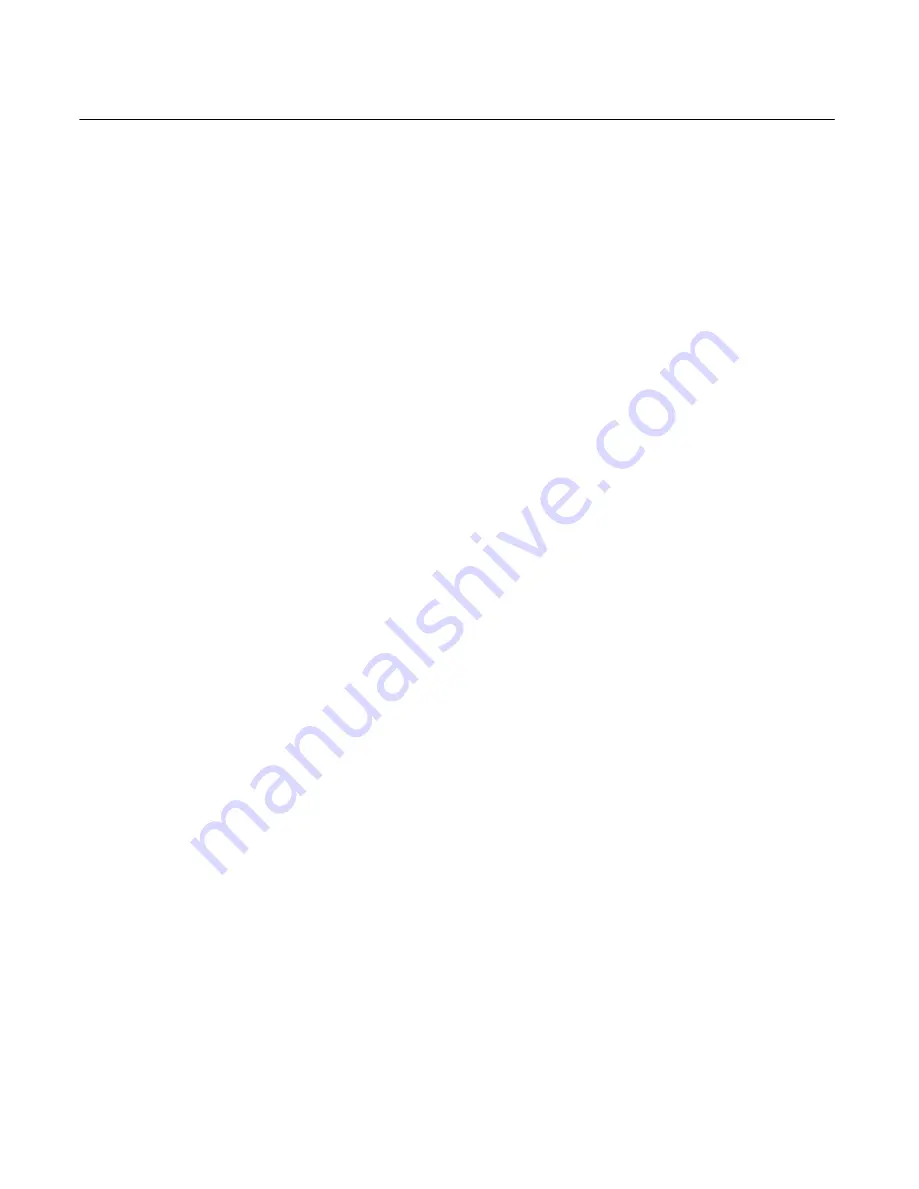
GX Valve and Actuator
Instruction Manual
Form 5770
June 2006
7
5. Torque the cap screw (key 14) to the actuator rod
(key 22) to 65.5 N
S
m (48.3 lbf
S
ft) and lay this
assembly into the upper diaphragm casing (key 9).
6. Place the actuator springs (key 12) onto the
spring locators in the diaphragm plate (key 11).
D
For 6-inch size 1200 actuators,
place the
actuator springs (keys 12 and 13) onto the spring
locators in the diaphragm plate (key 11). Note that
eight large springs (key 13) should be used with one
installed at the center of the diaphragm plate and
seven installed radially around the diaphragm plate
(key 11). Seven small springs (key 12) should be
installed inside the large springs (key 13) which are
located radially around the diaphragm plate. There is
no small spring at the center of the diaphragm plate
(key 11).
7. Remove and replace the actuator rod bushing
(key 19) and actuator rod seal (key 20) in the
actuator yoke (key 8), if necessary.
8. Set the actuator yoke (key 8) down onto the
assembly that is resting in the upper diaphragm
casing (key 9) so that the yoke legs are
perpendicular with the ribs on the top of the upper
diaphragm casing (key 9).
9. Apply anti-seize lubricant to the threads.
D
For size 225 and 750 actuators,
install the
2
long
cap screws (key 16) and hex nuts (key 18) 180
degrees apart from each other and in line with the
actuator yoke legs.
D
For size 1200 actuators,
install the
4
long
cap
screws (key 16) and hex nuts (key 18) 90 degrees
from each other, with two of them in line with the
actuator yoke legs.
10. Tighten the
long
cap screws (key 16) and hex
nuts (key 18), alternating between them to gradually
compress the springs, until the two casing halves
and diaphragm touch.
11. Apply anti-seize lubricant to the threads and
install the remaining
short
cap screws (key 17) and
hex nuts (key 18) to the casing.
12. Tighten the actuator casing cap screws evenly
using a cross-tightening procedure. Torque to 55
N
S
m (40 lbf
S
ft).
13. If you had previously removed the actuator
assembly from the valve, place the actuator
assembly back onto the valve body (key 1).
For
standard bonnet constructions (figures 15, 16,
install the body nuts (key 7) and tighten
evenly using a cross-tightening procedure.
See table 3 for torque requirements.
For extension and bellows bonnet constructions
(figures 19 and 20),
install the bonnet nuts (key 46)
and tighten evenly using a cross-tightening
procedure. See table 4 for torque requirements.
14. With the valve plug/stem (key 3) in the closed
position (on the seat), thread the stem adjustor nut
(key 27) up until it is at the rated travel (see table 2)
from the actuator rod (key 22). Thread the locknut
(key 28) up against the stem locknut and tighten.
15. Stroke the actuator rod until it contacts the stem
adjuster nut (key 27) and install the stem connector
halves and travel indicator (keys 23, 24, and 26) with
the cap screws (key 25). Install the stem connector
halves in the proper orientation so that when looking
at the inside of the stem connector halves, the flats
are down and the beveled surfaces are up.
16. Align the pointer of the travel indicator (key 26)
with the appropriate mark on the travel scale.
17. Tighten the stem connector cap screws
(key 25) to 24 N
S
m (18 lbf
S
ft).
18.
Note: For air-to-close action, the air supply
tubing must be connected to the actuator upper
casing at the air supply connection, see
figure 17 or 18. (If converting from air-to-open to
air-to-close, the tubing will need to be re-routed
to this location).
FIELDVUE
r
DVC2000 Digital Valve
Controller Mounting
This section provides instruction on mounting the
FIELDVUE DVC2000 Series digital valve controller
to the Design GX control valve. For further detail on
the operation and maintenance of the DVC2000
positioner, refer to the DVC2000 instruction manual.
The FIELDVUE DVC2000 Series digital valve
controller mounts directly to an interface pad on the
GX actuator yoke leg, eliminating the need for
mounting brackets (see figure 1). Internal
passageways in the actuator route the pneumatic
output to the actuator casing, which eliminates the
need for external air supply tubing in the air-to-open
(spring-to-close) constructions. (The GX will also
accommodate other valve positioners, using the
NAMUR mounting pads on the side of the yoke
legs.)