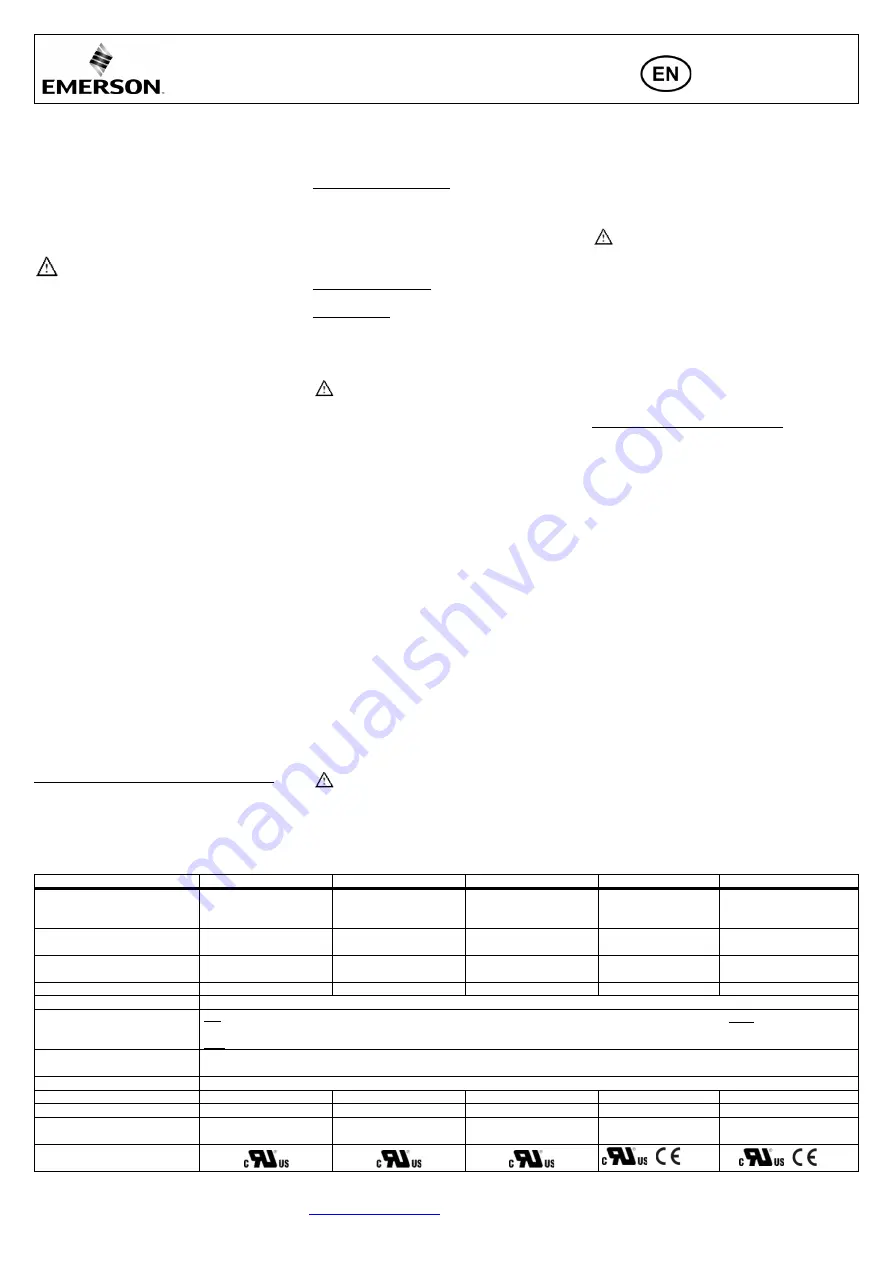
Operating instructions
Electrical Control Valves EX4-8
Emerson Climate Technologies GmbH
Date: 28.04.2020
Am Borsigturm 31 I 13507 Berlin I Germany
EX4-8_OI_EN_DE_FR_ES_IT_RU_R08_865288.docx
General information:
EX4-8 are stepper motor driven valves for precise
control of refrigerant mass flow in refrigeration, air
conditioning, heat pumps, industrial cooling process
and close control systems as:
-
expansion valves and liquid injection valves
-
suction pressure regulator (evaporator or crankcase)
-
hot gas bypass regulator
-
hot gas flow such as heat reclaim application
-
Condensing pressure regulator and liquid duty
Safety instructions:
•
Read operating instructions thoroughly. Failure to
comply can result in device failure, system damage
or personal injury.
•
According to EN 13313 it is intended for use by
persons having the appropriate knowledge and
skill.
•
Before opening any system make sure pressure in
system is brought to and remains at atmospheric
pressure.
•
Do not release any refrigerant into the
atmosphere!
•
Do not exceed the specified maximum ratings for
pressure, temperature, and voltage.
•
Do not operate system before all cable connections
are completed.
•
Do not operate valve connected directly to supply
voltage. Use suitable stepper motor driver.
•
Do not operate the valve when the compressor is
not running.
•
Do not operate the valve when system is under
vacuum except for closure of valve before
refrigerant charging.
•
Before installation or service disconnect all
voltages from system and device.
•
Do not use any other fluid media without prior
approval of EMERSON. Use of fluid not listed
could result in a change of hazard category of
product and consequently change of conformity
assessment requirement for product in accordance
with European pressure equipment directive
2014/68/EU.
•
Ensure that design, installation and operation are
according to European and national
standards/regulations.
Mounting location: (Fig. 1,2)
Expansion valve and liquid injection applications:
-
The motor needs to be pointed between downward to
sideways. (Fig. 1)
-
For best result, locate the valve as close as possible to
the distributor or inlet of evaporator.
-
Check for sufficient refrigerant charge/subcooling
and make sure no flash gas is present at the inlet of
valve before attempting to check valve operation.
Install an sight glass as well as a filter drier before the
valve.
Hot gas bypass applications:
-
The motor needs to be pointed downward.
-
Install the valves as far as possible from compressor
discharge.
-
It is also recommended to install a check valve (
)
on main hot gas pipe going to condenser after branch
line into the valve (
) (Fig. 2).
Suction line application:
-
The motor needs to be pointed downward.
Oil free system:
-
The motor needs to be pointed downward.
Installation:
•
Direction of refrigerant flow must match with arrow
on the label (except bi-flow valves).
Warning:
•
All valves are delivered at half open. Do not charge
system before closure of valve. See operating
instruction of used driver/controller.
•
The interior parts of valve must be protected
against moisture and water at any time. It is not
permitted the use of water, steam or any other
solvent to the inside of valve for cleaning purpose.
Brazing: (Fig.3)
•
Perform and consider the brazing joint as per
EN 14324.
•
Before and after brazing clean tubing and brazing
joints.
•
Minimize vibrations in the piping lines by appropriate
solutions.
•
Do not exceed the max. body temperature of
120°C!
•
Use flux and silver rod having a minimum of 30%
silver.
Pressure Test:
After completion of installation, a pressure test must be
carried out as follows:
-
according to EN 378 for systems which must
comply with European pressure equipment
directive 2014/68/EU.
-
to maximum working pressure of system for other
applications.
Warning:
•
Failure to do so could result in loss of refrigerant
and personal injury.
•
The pressure test must be conducted by skilled
persons with due respect regarding the danger
related to pressure.
Leakage Test:
Conduct a tightness test according to EN 378 with
appropriate equipment and method to identify leakages
of external joints. The allowable leakage rate must be
according system manufacturer’s specification.
Electrical Connection:
Warning:
•
Entire electrical connections have to comply with
local regulations.
•
Improper wiring will result wrong direction of
rotation or no rotation of stepper motor
•
Prewired plug (EXV-M…) are not in compliance with
EN60335-1-40/89 and are ready for connection to the
valve.
•
There is no specific requirement for positioning of
plug on pins (see Fig.5): Push the plug on pins on top
of the valve. Rotate the nut one turn in clockwise
direction and push the plug. Repeat this procedure
until the plug is tightened.
Wiring / Mounting to driver/Controller:
See the wiring diagram of applied driver/controller.
Operation:
•
See operating instructions of applied electronic
driver/controller.
Service / Maintenance:
•
Defective EX valves must be replaced, they cannot
be repaired.
•
For motor check:
-
Remove cable plug from valve.
-
Use an ohmmeter with suitable range.
-
Measure windings resistance per phase at opposite
placed pins acc. Fig.6 and data as in the table below.
•
EX4-8 has capability of positive shut-off when it is
driven to fully close position (as long as inlet pressure
is 0.5 bar above outlet pressure).
Technical Data:
Type
EX4
EX5
EX6
EX7
EX8
Maximum working pressure PS
90 bar (uni-flow),
60 bar (bi-flow)
UL Approval: all 60 bar
60 bar
60 bar
60 bar
45 bar
Factory pressure Test PT
99 bar (uni-flow),
66 bar (bi-flow)
66 bar
66 bar
86 bar
65 bar
Hazard category:
PED 2014/34/EU
-
-
-
II
II
PED Conformity Assessment
-
-
-
Module D1
Module D1
Fluid group (acc.PED)
I (listed A2L refrigerants) & II (listed A1 refrigerants)
Refrigerants
A1:
R744 (subcritical), R448A, R449A, R513A, R450A, R134a, R452A, R23, R410A, R407C,
R404A, R507, R124
Note:
UL Approval: only A1
refrigerants
A2L:
R1234ze, R32, R452B, R454B, R454A, R454C, R123yf
Operating temperature
at inlet:
Uni-flow: –50*… +100°C, Bi-flow: -50*…+80°C
at outlet:
-100*…+100°C
*) UL Approval:
≥
- 40°C
Dimensions
see Fig. 4
Nominal Supply Voltage U
24 VDC
24 VDC
24 VDC
24 VDC
24 VDC
Maximum Current Imax
0.5 A
0.5 A
0.5 A
0.75 A
0.8 A
Winding resistance per phase /
isolation resistance
14
Ω ±
10% /
> 20 M
Ω
14
Ω ±
10% /
> 20 M
Ω
14
Ω ±
10% /
> 20 M
Ω
10
Ω ±
10% /
> 20 M
Ω
7.5
Ω ±
10% /
> 20 M
Ω
Markings
,
1017
,
1017