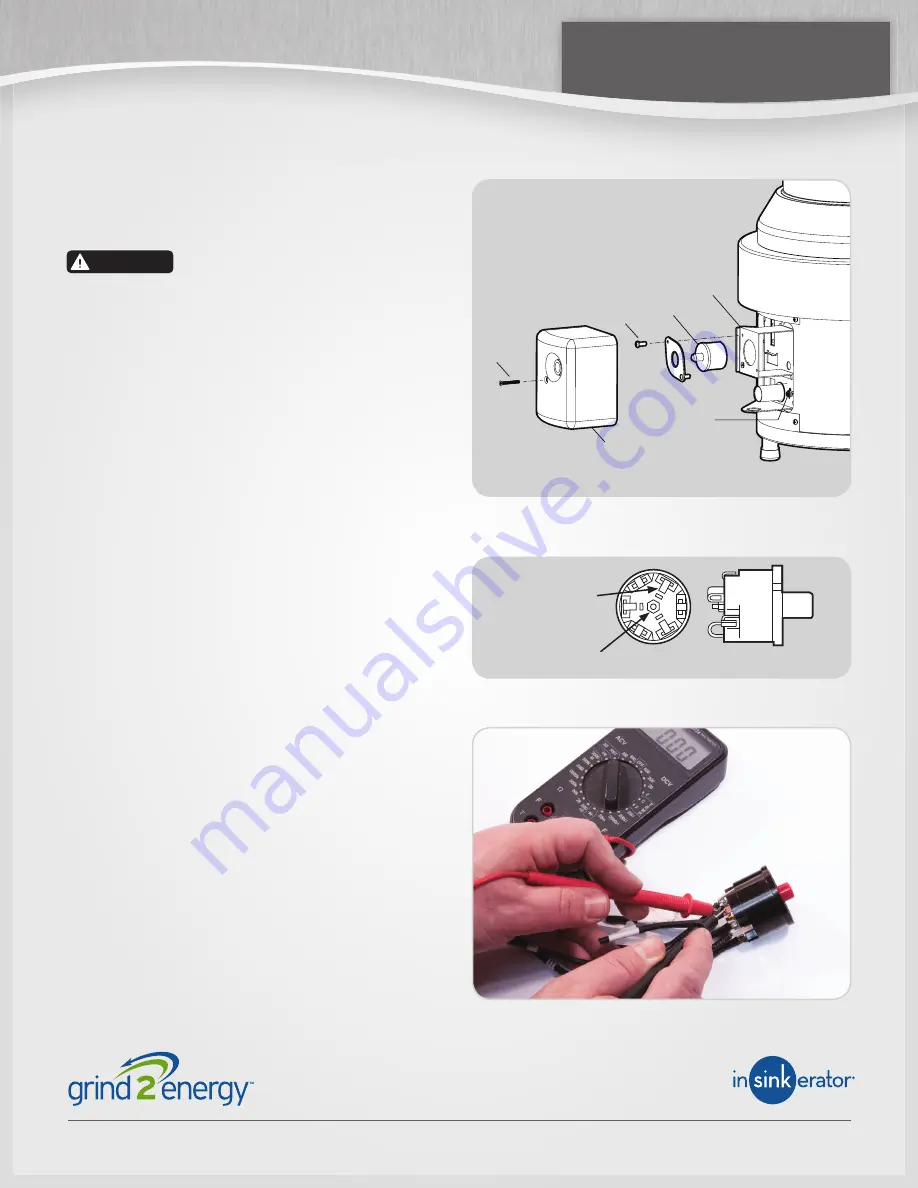
Terminal Box
Overload
Protector
Mounting
Bracket
Grounding
Screw
Screw
Screw
Overload Protector
Terminal
6
1
2
5
4
3
Center post
(3 Ø shown)
Overload Protector
Testing Overload Protector
WARNING
SHOCK HAZARD!
Turn off electrical power at circuit
breaker, use voltmeter or circuit tester to ensure that
POWER IS OFF.
1. Remove screw and terminal box (figure 23).
2. Remove two screws, securing overload protector to
bracket and pull out from unit. Disconnect overload wires
from stator.
3. Push red button in and check continuity between all
terminals and center post using an ohmmeter (figure 24).
6 terminals – 3 Ø
4. Check for continuity between all terminals and center
post. Replace overload protector if circuit is open on any
terminal/center post combination.
5. Re-install terminal box in reverse order.
Replacing Overload Protector
1. Remove screw and terminal box (figure 24).
2. Disconnect wires.
3. Remove two screws securing overload protector to
bracket, disconnect wires and remove protector.
4. Connect new switch wires and tuck wires into bracket
and secure new protector to bracket using two screws.
5. Re-install terminal box and screw.
grind2energy.com
Grind2Energy Technical Support: 844-874-7529 | 15
G2E015-15F-89-84
figure 24. Testing Overload Protector
figure 23. Terminal Box and Components
figure 24. Testing Overload Protector