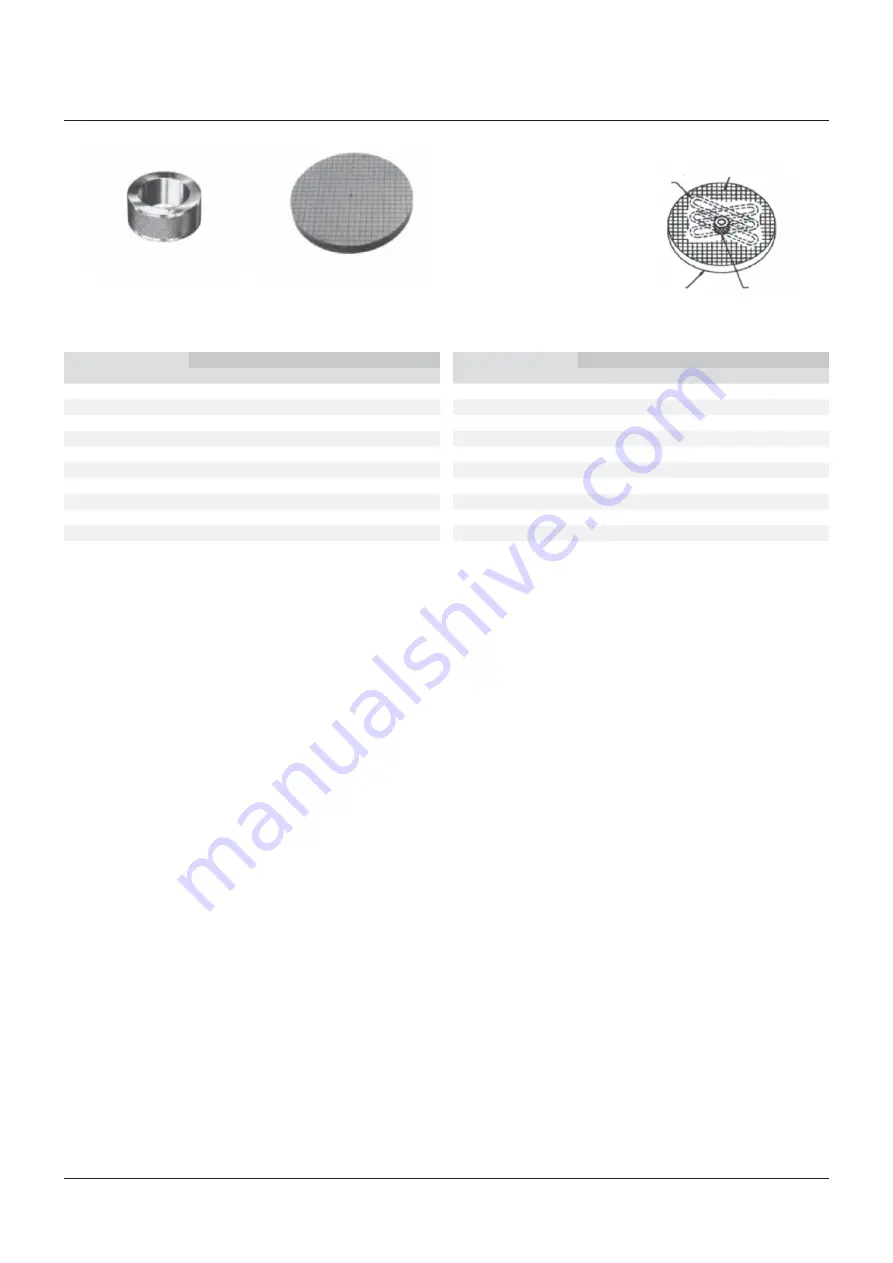
9
F
.002
.051
G
.002
.051
H
.002
.051
J
.003
.076
K
.003
.076
L
.002
.151
M
.003
.076
N
.003
.076
P
.003
.076
Q
.005
.127
F
.002
.051
G
.003
.076
H
.003
.076
J
.004
.102
K
.005
.127
L
.006
.152
M
.007
.178
N
.008
.203
P
.009
.229
Q
.012
.305
CROSBY
STYLE HSL SAFETY VALVES
INSTALLATION, MAINTENANCE AND ADJUSTMENT INSTRUCTIONS
FIGURE 7
Top lapping surface
Motion shown by
dotted line
Lapping block to
be squared up
Bottom rough
surface do not use
FIGURE 6
Lapping block resurfacing plate
Lapping block
TABLE 3 - 'B' DIMENSION
Dimensions
Orifice
NPS
DN
TABLE 4 - SPINDLE CONCENTRICITY (TIR) – DIMENSION
Dimensions
Orifice
NPS
DN
Lapping procedure
Unless the seats have been damaged badly
by dirt or scale, lapping the seating surfaces
should restore them to their original condition.
Never lap the disc insert or disc against the
nozzle.
Lap each part separately against a cast iron
lapping block of the proper size. These blocks
hold the lapping compound in surface pores
and must be reconditioned frequently. Lap the
block against the seat. Never rotate the block
continuously, but use an oscillating movement.
Extreme care should be taken throughout to
make certain the seats are kept perfectly flat.
A. If considerable lapping is required, spread
a thin coat of medium coarse lapping
compound on the block.
B. After lapping with this compound, lap again
with a medium grade compound. The first
step can be omitted unless much lapping is
needed.
C. Lap again using a fine grade compound.
D. When all nicks and marks have disappeared,
remove all compound from the block and seat.
E. Apply polish compound to another block and
lap the seat.
F. As the lapping nears completion, only the
compound left in the pores of the block
should be present. This should provide a
very smooth finish. If scratches appear, the
cause is probably dirty lapping compound.
These scratches should be removed by
using compound free of foreign material.
Discs and disc inserts should be lapped in the
same way as nozzles. The disc insert must be
removed from the holder before to lapping.
Machining nozzle seats
If machining of the nozzle seat or other major
repairs is necessary, it is recommended that
the valve be returned to a Emerson authorized
facility for repair. All parts must be machined
accurately per Emerson specifications. No
pressure relief valve will be tight, nor will it
operate properly unless all parts are machined
correctly.
The most satisfactory way to machine a nozzle
is to remove it from the body. However, it may
also be machined while assembled within the
valve body. In any event it is vitally important
that the seating surfaces run absolutely true
and the original nozzle profile is re-established
as shown in Figure 5. Machining dimensions for
Crosby Style HSL valves are shown in Table 2
and Figure 5. Remove only enough metal to
restore the surface to its original condition.
Turning to the smoothest possible finish will
facilitate lapping. After machining, measure
the nozzle height to ensure it still exceeds the
minimum dimension from Table 2 and then lap
the nozzle seat before re-installation into the
valve body. The nozzle must be replaced when
the minimum face to seat dimension is reached.
Before the disc insert is placed back in the
holder all foreign material should be removed
from both parts. The insert must be free when
in the holder. If the disc insert is damaged too
badly to be reconditioned by lapping, it should
be replaced. Remachining the insert will
change critical dimensions, affecting the action
of the valve and is not recommended.