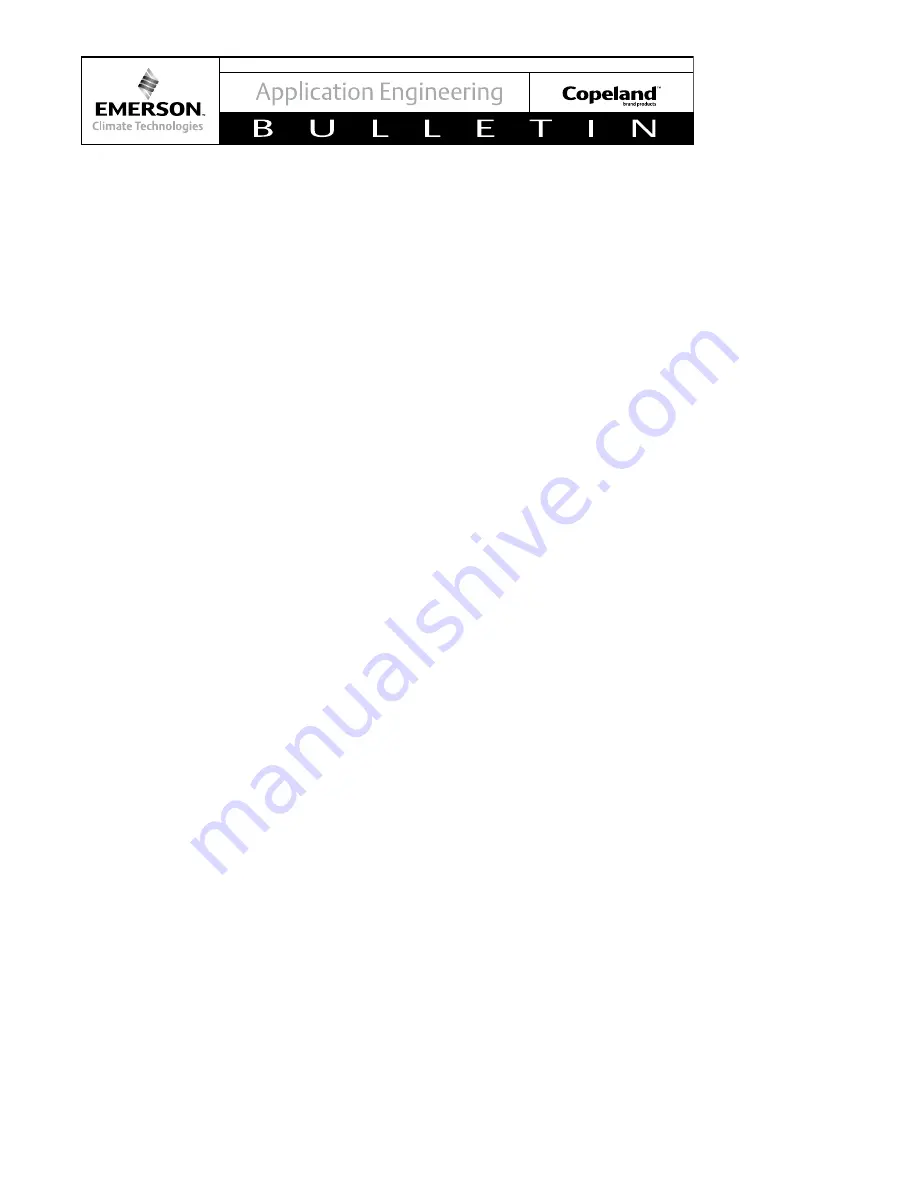
AE4-1312 R2
© 2010 Emerson Climate Technologies
Printed in the U.S.A.
8
15% of the average on the three phases of a three-
phase compressor should be investigated further. A
more comprehensive trouble-shooting sequence for
compressors and systems can be found in Section
H of the Emerson Climate Technologies Electrical
Handbook.
7. Before replacing or returning a compressor
:
Be
certain that the compressor is actually defective. As
a minimum, recheck a compressor returned from
the field in the shop or depot for Hipot, winding
resistance, and ability to start before returning to
Emerson Climate Technologies. More than one-third
of compressors returned to Emerson for warranty
analysis are determined to have nothing found
wrong. They were misdiagnosed in the field as
being defective. Replacing working compressors
unnecessarily costs everyone.
Tandem Scroll Compressors
The refrigerant charge limit for tandem compressors
is shown in
Table 5.
A three-phase unit with a charge
over this limit must have crankcase heaters added to
both compressors. The ZRT90 – ZRT122 compressors
are mounted on rails using rubber mounting parts. The
ZRT136 – ZRT162 compressors are rigidly mounted
on rails using solid steel mounting parts. These
mounts are installed at the factory and should not be
loosened. Tighten to 125 inch pounds (14 NM) if it
becomes necessary to tighten these mounts. Holes
in the mounting rails may be used to mount isolation
grommets under the entire tandem.
A discharge check valve must be placed in the
common discharge line when pump down is used. Both
compressors must be at the same level to prevent oil
from migrating to the lowest compressor through the
oil equalization line.
Compressors may be individually cycled. Individual
compressors should not be replaced in the field. The
entire tandem compressor unit must be replaced if
it becomes necessary to replace one compressor.
Individual compressors configured for tandem usage
may not be available for field replacement. See
section below for further tips on field replacement of
compressors.
Compressor Replacement after Motor Burn
In the case of a motor burn, the majority of contaminated
oil will be removed with the compressor. The rest of the
oil is cleaned through use of suction and liquid line filter
dryers. A 100% activated alumina suction filter drier is
recommended but must be removed after 72 hours. See
AE24-1105
for clean up procedures and
AE11-1297
for liquid line filter-drier recommendations.
It is highly
recommended that the suction accumulator be
replaced if the system contains one.
This is because
the accumulator oil return orifice or screen may be
plugged with debris or may become plugged shortly after
a compressor failure. This will result in starvation of oil
to the replacement compressor and a second failure.
Start-up of a New or Replacement Compressor
It is good service practice, when charging a system,
to charge liquid refrigerant into the high side only and
charge the low side of the system with vapor only. It is
not good for any compressor to have liquid refrigerant
dumped from a refrigerant cylinder into the crankcase
of the compressor.
Do not start the compressor while
the system is in a deep vacuum.
Internal arcing may
occur when a scroll compressor is started in a vacuum.
Do not operate compressor without enough system
charge to maintain at least 7 psig (0.5 kg/cm2)
suction pressure. Do not operate with a restricted
suction. Do not operate with the low pressure
cut-out disabled.
Allowing suction pressure to drop
below 7 psig (0.5 kg/cm2) for more than a few seconds
may overheat scrolls and cause early drive bearing
damage. Never install a system in the field and leave it
unattended with no charge, a holding charge, or with the
service valves closed without securely locking out the
system. This will prevent unauthorized personnel from
accidentally operating the system for comfort cooling
and potentially ruining the compressor by operating
with no refrigerant flow.
Excessive Liquid Flood back Tests
The following tests are for those system configurations
and charge levels identified in
Table 1
that need special
testing to verify exemption from need of an accumulator.
Figure 1
should be used to determine the effectiveness
of an accumulator. The compressor sump temperature
during any test where the return gas superheat is near
zero must always meet the guidelines of
Figure 1
.
To test for
excessive continuous liquid refrigerant
flood back
, it is necessary to operate the system in a test
room at conditions where steady state flood back may
occur (low ambient heating operation). Thermocouples
should be attached with glue or solder to the center of
the bottom shell and to the suction and discharge lines
approximately 6 inches (15 cm from the shell). These
thermocouples should be insulated from the ambient air
with Permagum® or other thermal insulation to be able
to record true shell and line temperatures. If the system
is designed to be field charged, it should be overcharged
by 15% in this test to simulate overcharging commonly
found in field installations.