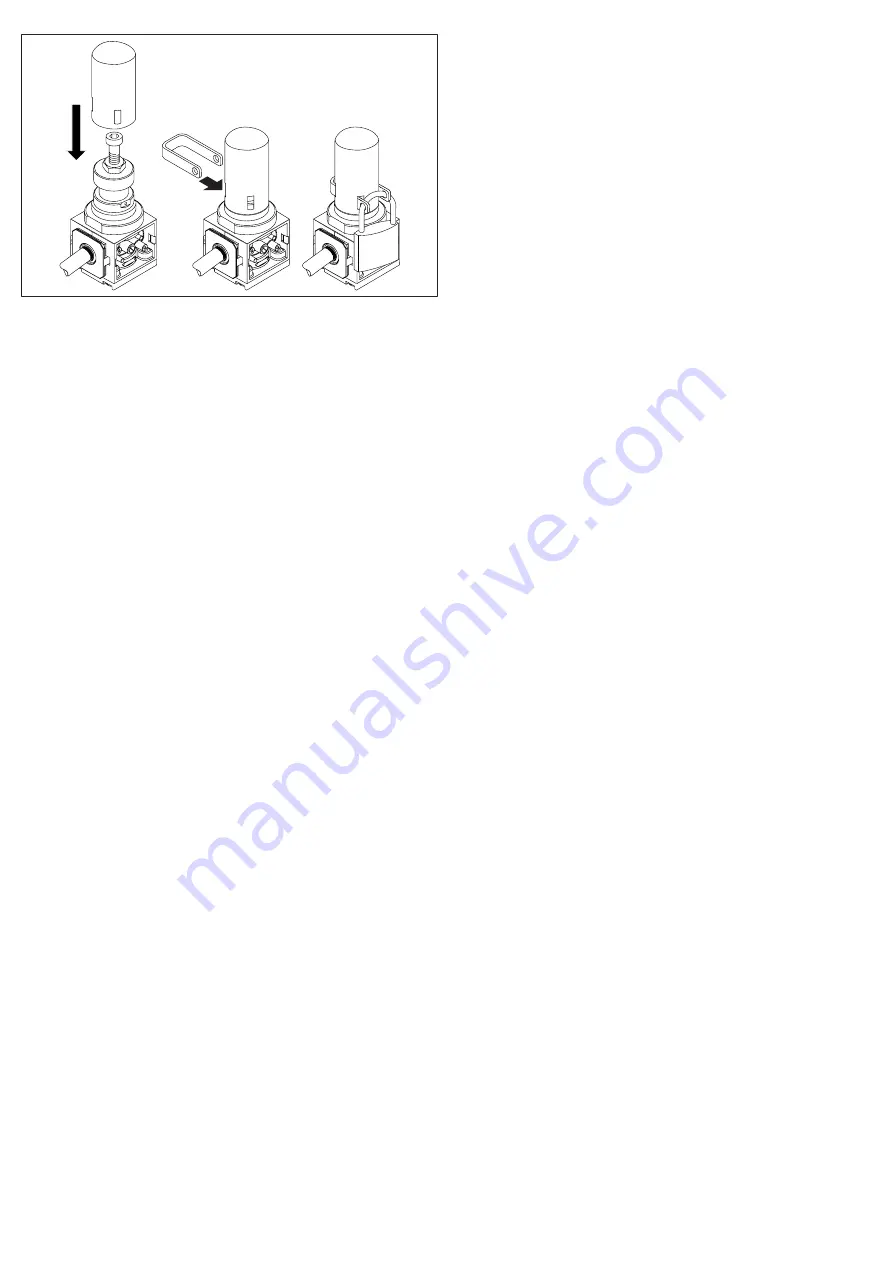
I.
II.
III.
Fig. 8: Attaching the adjustment screw lock
1.
Place the adjustment screw lock on the adjustment screw.
2.
Push the locking bracket through the adjustment screw lock.
3.
Lock the locking bracket with a suitable device, e.g. a padlock.
7 Commissioning
Follow the steps below to carry out commissioning.
7.1 Basic requirements
Personnel qualifications
Commissioning only by qualified personnel (see section
cations).
Limits
• Comply with the limits (accident prevention, material protection). Limits: see
7.2 Notes on safety
To eliminate risks during commissioning, observe the notes on safety: see section
7.3 Preparation
General requirements
• Make sure that all plugs and connections have been mounted correctly.
7.4 Step-by-step commissioning
If you have carried out and completed all preparation work, you can commission
the system.
8 Operation
8.1 Basic requirements
The following points must be observed during operation.
General requirements
• Do not touch the product or any connected parts during operation (accident
prevention).
• Never switch off, modify or bypass safety devices.
Limits
• Comply with the limits (accident prevention, material protection). Limits: see
• Make sure that there are no ferromagnetic sources near the product (material
protection).
Service
• Carry out service work in the designated time intervals: see section
In case of malfunctions during operation
• In case of a malfunction that presents an immediate danger for employees or
systems: Switch off product.
• Carry out analysis and troubleshooting of malfunctions according to the fol-
lowing specifications: see section
• If a malfunction cannot be remedied: Inform the customer service. Contact
data: see back cover.
9 Service
The following operation-related activities are necessary to ensure safe use of the
product with minimal wear and tear:
• Cleaning, see section
9.1 Notes on safety
To eliminate risks during service, observe the notes on safety: see section
9.2 Inspection
During inspection, check the product for damage and contamination at regular
intervals.
9.2.1 General requirements
Use in normal ambient conditions
• Inspection interval: The product must be checked monthly.
• The operator is responsible for inspection of the product and the overall sys-
tem.
Use in aggressive ambient conditions
Aggressive ambient conditions include, for example:
• High temperatures
• Heavy accumulation of dirt
• Proximity to grease-dissolving liquids or vapors
Aggressive ambient conditions lead to further requirements for inspection:
• Adapt the inspection interval for seals to the ambient conditions.
NOTICE!
Seals age faster under aggressive ambient conditions. Inspect seals
more frequently.
• Enter the adapted inspection intervals in the system-specific maintenance
plan (accident prevention, material protection).
9.2.2 Procedure
Preparation
All work has to be prepared as follows:
1.
Close off dangerous areas (accident prevention).
2.
Make sure the system or system part is not under pressure or voltage.
3.
Protect the system against being restarted.
4.
Allow the product and adjacent system parts to cool down (accident preven-
tion).
5.
Wear protective clothing (accident prevention).
Visual inspection
Visually inspect for integrity.
Detailed inspection
• Check identifications and warnings on the product: Labels and identifications
must be legible (accident prevention, material protection).
Replace hard-to-read labels or identification immediately.
• Check the lines.
• Check the seals.
• Check to make sure that all fittings are properly connected.
• Check the safety devices on the system.
• Check the product functions.
AVENTICS™
645 | 548325-001 | English
19