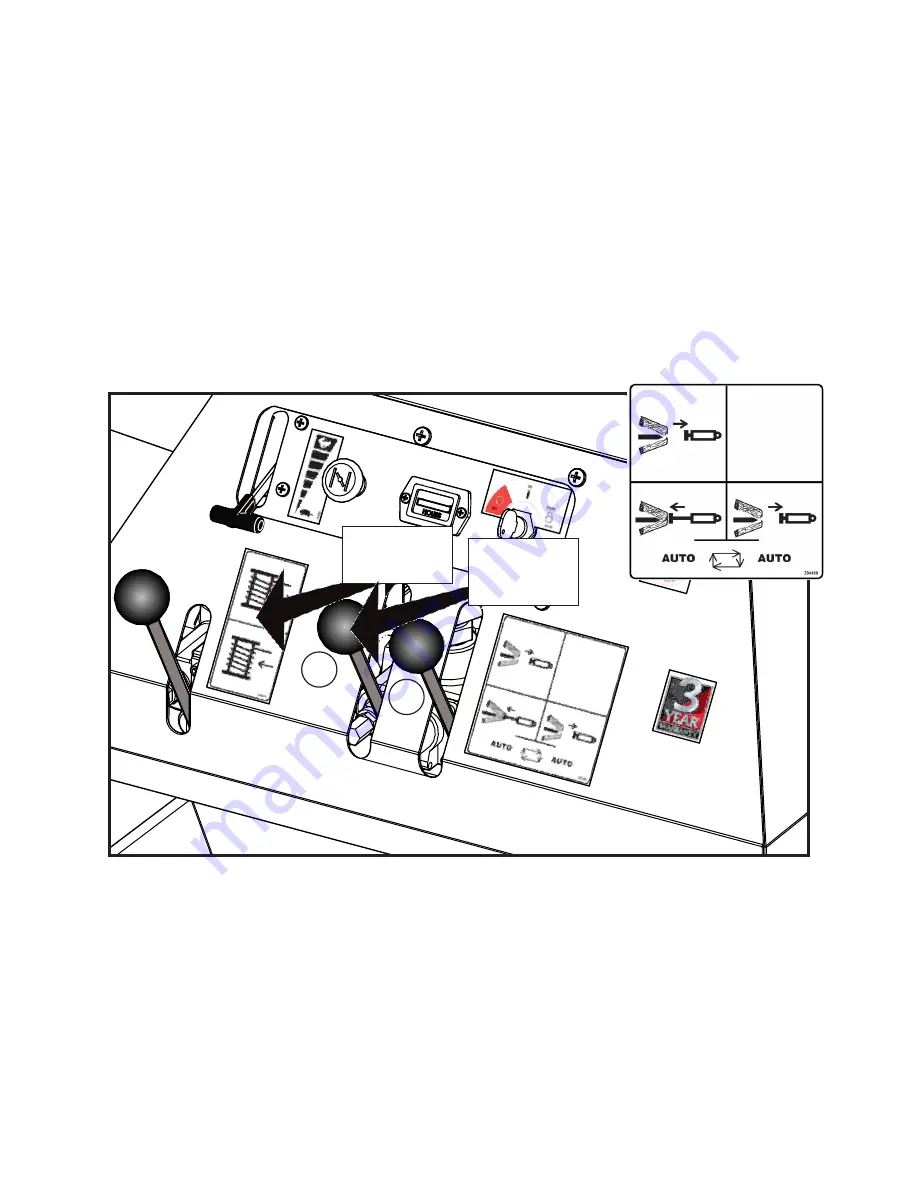
24
Fig. 7 WP830 and WP860 SPLITTER
CYLINDER CONTROL & LABEL
4.5.5. HYDRAULIC CONTROLS & AUTO CYCLE
WP830 and WP860:
These two hydraulic levers control the extending and retracting movement of the Wood Processors' splitting
cylinder rod.
These 3-position "spring-loaded-to-center neutral" levers, control the flow of oil to the cylinder.
They are equipped with a detent in the engaged position to allow the cylinder to move through its complete
cycle and then return to its starting position automatically.
Lever #1 controls the first half of the cylinders auto cycle.
1. Pull it back into detent and the cylinder will start to extend automatically.
2. When the cylinder has fully extended, the lever will kick out to neutral and automatically stop the cylinder.
Lever #2 controls the second half of the cylinders auto cycle.
1. Pull it back into detent and the cylinder will start to retract automatically
2. When the cylinder has fully retracted, the lever will kick out to neutral and automatically stop the cylinder.
Pull both levers back into the detent position to initiate the splitting cycle. The cylinder will fully extend to
split the log. When it reaches full extension (the log is split),#1 lever will pop out of detent. The cylinder
will then begin to retract. When fully retracted #2 lever will come out of detent and the cylinder will stop.
Please note that lever #1 can be used to manually retract the cylinder:
1. Move lever #1 forward, the ram will begin to retract
2. Release the lever and it will return to neutral and the cylinder will stop.
Pull back to
auto cycle
extend
Pull back to
auto cycle
retract
1
2