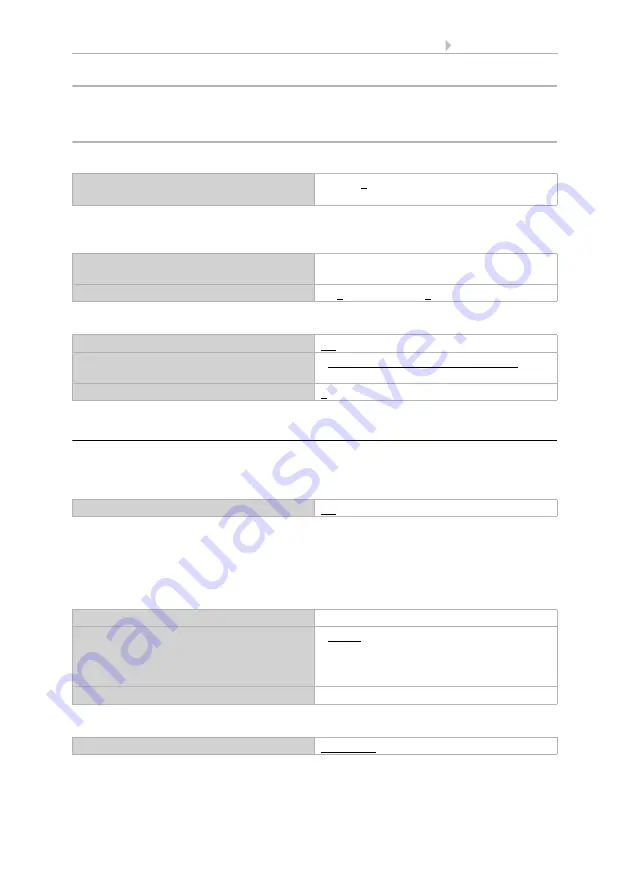
34
Parameter setting
Sensors Intra-Sewi KNX TH-L-Pr and Intra-Sewi KNX L-Pr
• Version: 30.08.2018 • Technical changes and errors excepted.
Information on setting the slave sending cycle and the cycle reset can
be found in chapter
Align communication between master and slave
Set the
sending cycle
shorter than the master's switch-off delay.
Set the
object type and value
for the cycle reset input for the slave in the same way
as for the cycle reset output for the master.
The slave can be
blocked
via the bus.
5.6.1. Master 1/2/3/4
If the device is set as a master, the additional master settings 1 to 4 will appear. This
enables the sensor to perform four different control functions for motion detection. Ac-
tivate the master in order to use it.
Set, in which cases
threshold values and delay times
received via object are to be
retained. The parameter is only taken into consideration if the setting via object is ac-
tivated below. Please note that the setting "After power supply restoration and pro-
gramming" should not be used for the initial start-up, as the factory settings are always
used until the 1st communication (setting via objects is ignored).
Select, whether motion is to be detected
constantly or brightness dependent
.
Sending cycle in the event of movement
(in seconds)
1...240; 2
Cycle reset object type
• 1 bit
• 1 byte (0%...100%)
Cycle reset at value
0 • 1 and/or 0...100; 1
Use block
No •
Yes
Analysis of the blocking object
• at value 1: block | at value 0: release
• at value 0: block | at value 1: release
Value prior to first communication
0 • 1
Use master 1/2/3/4
No • Yes
Maintain the
threshold values and delays received
via communication objects
• never
• after power supply restoration
• after power supply restoration and
programming
Motion detection
constantly • brightness dependent
Summary of Contents for Intra-Sewi KNX L-Pr
Page 2: ......
Page 6: ...6 Clarification of signs ...