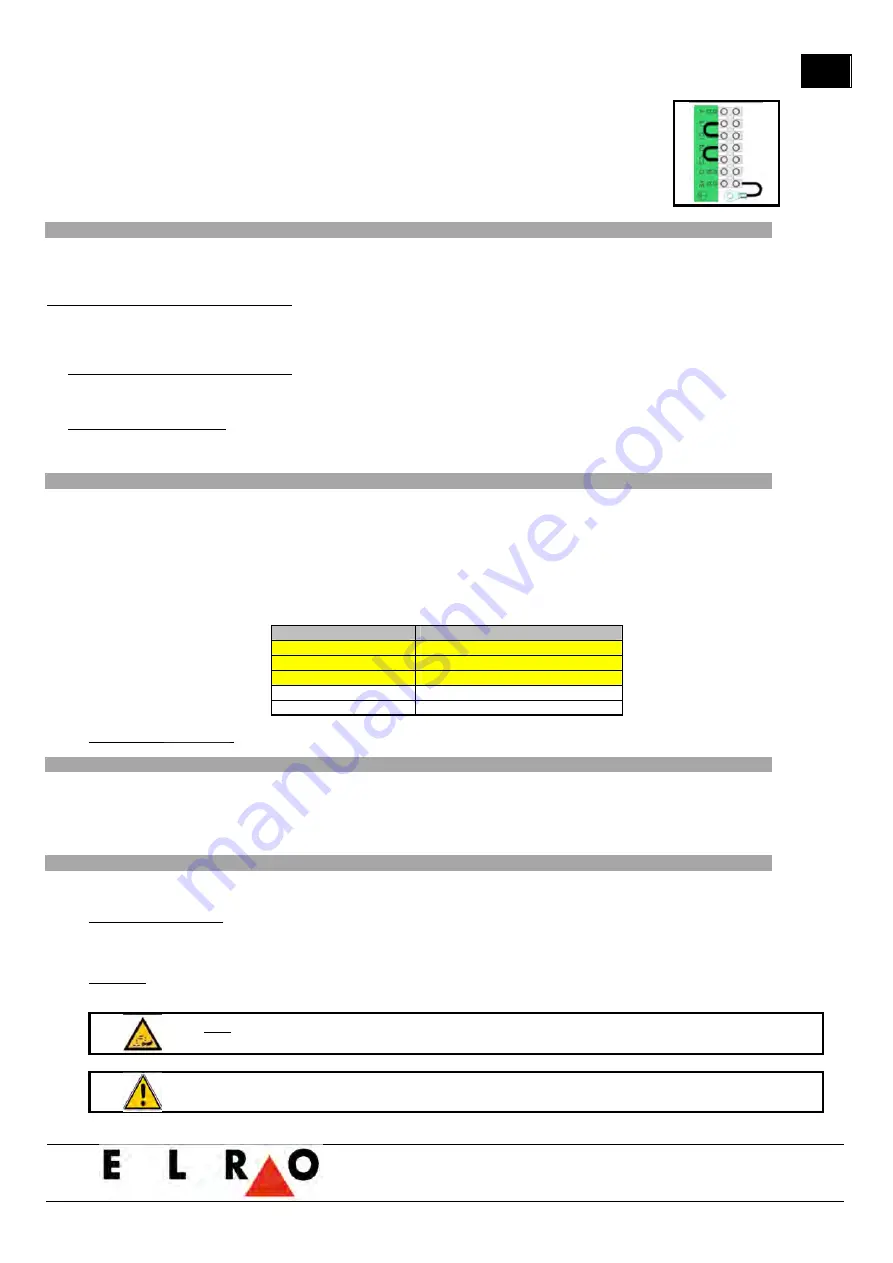
3E-490044NI – 03/20
Page 4
EN
ELRO-Werke AG
Wohlerstrasse 47
5620 Bremgarten
A :
Oven output information = switch on/ switch off
B1 :
Oven output information: dry heat power request
C1 :
Oven input information: power allocation or not by the energy saver for dry heat
B2 :
Oven output information: steam heat power request
C2 :
Oven input information: power allocation or not by the energy saver for steam heat
D :
Neutral
PE :
Earth terminal
GAS CONNECTION
Check that the adjustments of the appliance correspond to the nature and pressure of the gas supply. (See section : Data plate).
Connect the appliance to the gas supply via a local isolation valve. Fig. 6B
CHECKING THE CONNECTION PRESSURE Fig. 6C
To check the gas supply pressure to the appliance, just connect a water column pressure gauge to the pressure tap (see the sketch below),
when the burners are working.
The gas pressure thus measured must be equal to that indicated on the data plate for the gas used (See section 1: Data plate).
Gas operating pressure on the jets (P out) Fig. 6D
The pressure should be from 8 to 11 mbar. Use a calibrated and accurate measuring device.
If the value is inconsistent do not change the setting of the gas valve, replace it.
Connection of a flexible hose:
Recommended solution: 6/10 level ovens: NF approved gas flexible hose (of "TUBOGAZ" type, 0.75 m in length, 15/21 (1/2")
∅
with
coupling) that must be periodically examined and replaced if necessary.
WATER CONNECTION
- To ensure that the mains water supply is protected and to comply with current regulations a backflow prevention devise conforming to CAa
standard (Ovens fitted with automatic wash function including an integral detergent pump) as per norms : EN14367 or EA (all other units) to
norms EN13959 and in compliance with local regulations (WRAS, SVGW, DVGW).
Pipework and anti-pollution protection is not fitted because the distance between the water supply and the unit are variable. Installation,
connection and commissioning should be undertaken by specialist concessionaires or authorised personnel.
- Nature: 168 µm filter integral with the oven
- Provide a local stop cock. Fig. 3A
- To check the quality of the water supply to your equipment, 3 major factors need to be addressed (see section « Controlling water quality »)
Parameter
Level required
Hardness
TH 4 to 7 °e (60 to 100 ppm)
Chlorides (Cl
-
)
≤
150 mg/l
PH
6.5 to 9
Conductivity
≥
50 µS / cm
Free chlorine (Cl
2
)
≤
0.2 mg / l
Attention (UK
specification
): Fit an approved double check valve to comply with local water regulations.
DRAIN CONNECTION
The water discharged could be condensate and at very high temperature (98°C). Only use materials suitable for these temperatures.
The oven is equipped with a vent which connects the appliance directly to the external drainage system to comply with pollution control
standards.
It is vital that there is a trap between the unit and the drainage system to prevent back odours. Fig. 4A
CONNECTION OF CLEANING PRODUCTS
The oven has an automatic cleaning system to wash the cooking cavity.
Except for the UK market: No detergent product is recommended or supplied. Any detergent used with this appliance must have been verified to
represent no greater risk than Fluid Category 3. If the detergent used represents a Fluid Category risk greater than Fluid Category 3 alternative
backflow protection to the double check valve supplied with the appliance will be required immediately upstream of the appliance. The backflow
protection used must be appropriate to the risk posed by the detergent.
Attention: The nature and length of the detergent hose should not be altered in any way
The detergent inlet hose is identified by a label and a coloured plug to ensure it is placed in the correct container. Fig. 7A
Note: Refer to the “General requirements” chapter when handling or using these chemicals, if in any doubt refer to
the products safety sheet
Never use descaling product in the automatic cleaning system. This could seriously damage the ovens
hydraulic circuits.