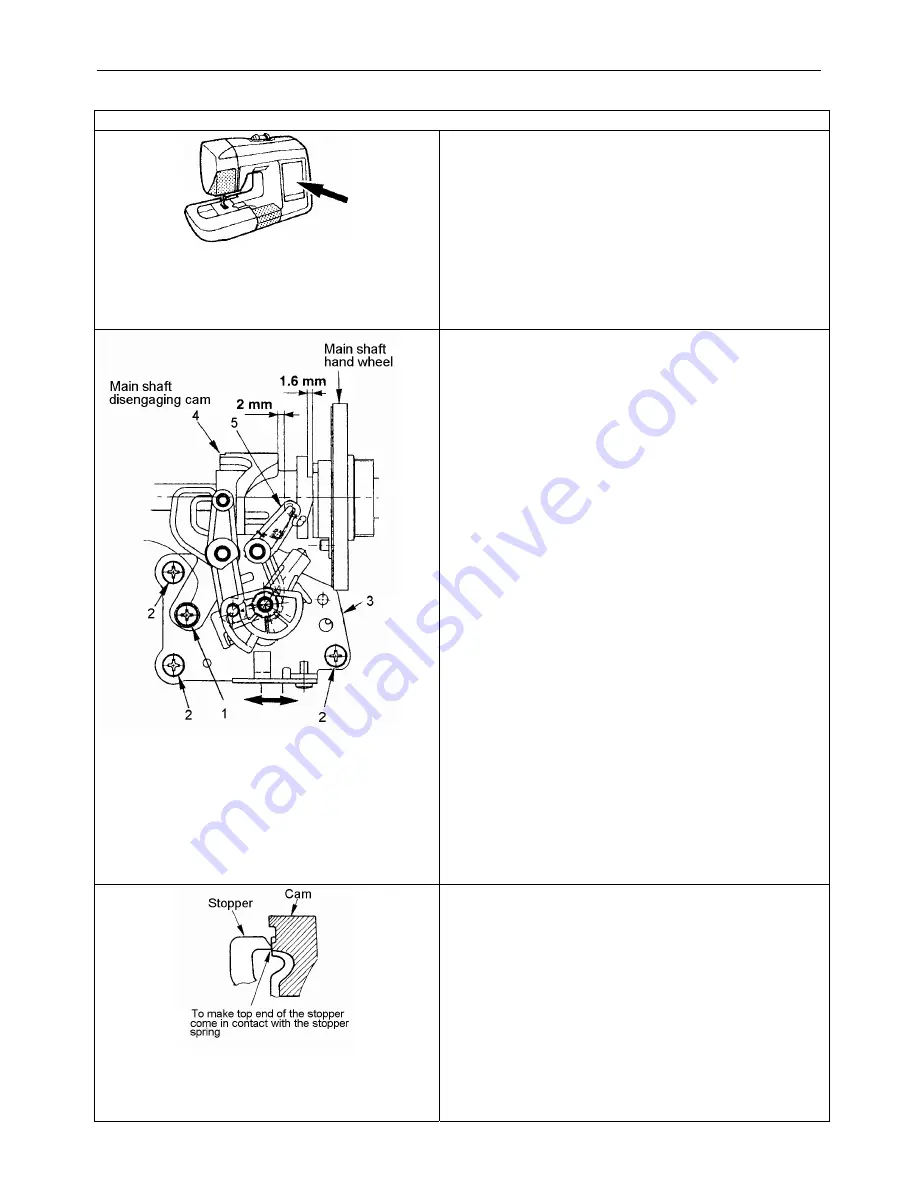
Elna International Corps. SA
Xquist
service manual
UPPER MAIN SHAFT DISENGAGING
Location of components to be adjusted.
6. Remove the Under cover.
7. Remove the Face cover inside.
8. Remove the Belt cover.
9. Remove the Free arm bottom cover.
10. Loose the 5 screws from the bottom plate base.
11. Remove the Front panel.
12. Disconnect all Front panel connectors.
13. Disconnect all connectors on the left side from the
microcomputer circuit board so that you have
access to the Disengaging mechanical system.
HOW TO ADJUST
Relation of the position of the main shaft disengaging
cam and the main shaft-disengaging cam.
1. Provide a clearance of 1,6 mm between the main
shaft hand wheel and the main shaft-disengaging
cam. Using a 1.6-mm spacer or the like.
2. Loosen adjustment screw 1 and the tree screws 2
from the needle throwing STM installing plate.
3. Move needle-throwing STM installing plate 3 to the
left or right to adjust the distance of 2 mm between
the main shaft-disengaging cam 4 and main shaft
disengaging link 5.
4. Tighten the tree screws 2 to fixe the needle
throwing STM installing plate.
Note:
When this adjustment is performed, the needle entry
point shifts. Perform again the needle entry
adjustment.
After this adjustment, perform the Main shaft
disengaging stopper adjustment.
MAIN SHAFT DISENGAGING STOPPER
1. Provide a clearance of 1,6 mm between the main
shaft hand wheel and the main shaft-disengaging
cam.
2. Loose the screw 1.
3. Make the top end of the main shaft disengaging
stopper comes in contact with the stopper spring.
4. Tighten the screw 1.
5. After adjustment, apply grease to the sections
below.
•
Joint of the main shaft-disengaging cam and
the main shaft hand wheel.
•
Cam section of the main shaft disengaging