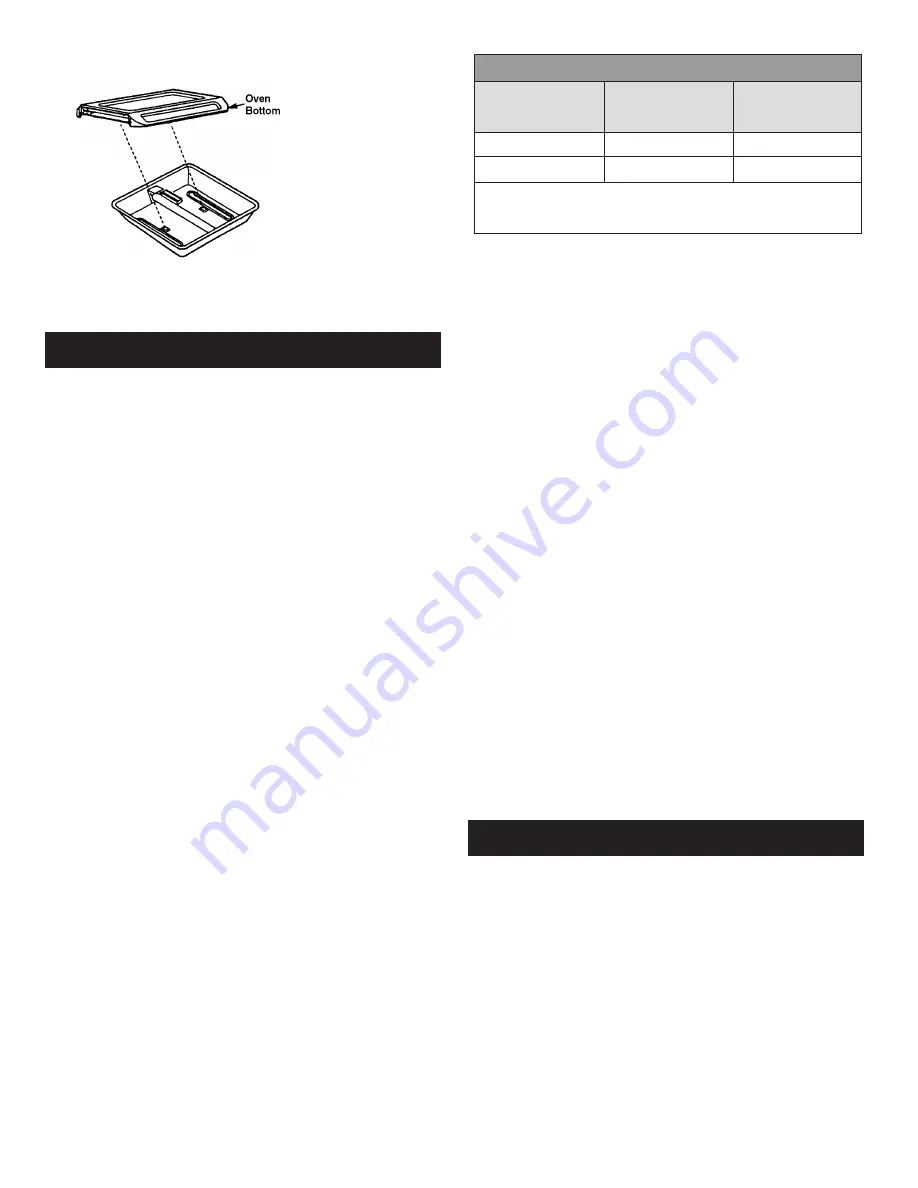
Hot air and moisture
escape from the oven
through a vent in the
center rear of the
cooktop.
Do not block
the vent.
Poor baking/
roasting and bad
combustion can result.
The oven bottom must
be in place for burner
to bake properly on
model 1956.
GAS SUPPLY SYSTEM
Gas and Electrical Supplies
Before connecting to the supply systems, be sure that
the installation conforms with the local codes or, in the
absence of local codes, with the National Fuel Code,
ANSI Z223.1 latest edition or in Canada, CAN/CGA B149
installation codes. See page
4 for electrical requirements.
Gas Piping to Range
The gas supply piping to the range should be 3/4” pipe
which is then reduced to 1/2” at the regulator. With
“LP” gas, the size of the piping to the range should be
determined by your gas fitter.
When connecting pipe to the die cast regulator fitting, use
two wrenches. Excess pressure or tightening the pipe too
tight can cause the regulator to crack, resulting in a gas
leak or a possible fire or explosion.
Make sure that if flexible connectors are used in
connecting the appliance to the gas supply, they are AGA
and/or CGA approved. Poorly designed connectors can
be a source of gas leaks. Even if AGA/CGA approved
flexible connectors are used, the customer should be
cautioned against kinking or damaging the connection
when moving or cleaning the range. This could cause a
gas leak.
Manual Shutoff
Install a manual shutoff valve in the gas line, in an
accessible location, near the unit. Know where the gas
valve is so you can shut off the gas to the range quickly.
Suitable pipe thread sealant must be used which is
approved for use with “LP”/Natural gas. Be sure to use
this thread sealant on all pipe connections.
Pressure Testing
The appliance, and its individual shutoff valve must be
disconnected from the gas supply piping system during
any pressure testing of that system at test pressures in
excess of 1/2 psi (3.5 kPa).
The appliance must be isolated from the gas supply piping
system by closing its individual manual shutoff valve
during any pressure testing of the gas supply system at
test pressures equal to or less than 1/2 psig (3.5kPa).
The gas supply pressure for checking the regulator
setting shall be at least one inch w.c. above
manufacturer’s specified manifold pressure.
Gas Leak Testing
After the final gas connection has been made, all the
top burner valves should be closed and the gas supply
and manual shutoff turned on. All connections in the
gas supply line and in the range should be tested with
soap suds or electronic sniffer for leaks. If a leak is
present, bubbles will appear. The leak should be stopped
by tightening the joint, or unscrewing completely and
applying additional pipe dope and re-tightened. Any
factory connections which may have been disturbed
should be retested.
A match should never be used when testing for leaks.
All fittings have been tightened and tested at the
factory. If a leak is detected, tighten the fitting. Don’t
use pipe dope on factory fittings.
FUEL CONVERSION OF RANGE TOP
Warning – Fire Hazard
• Locate gas supply shut off valve to the appliance.
• Shut off gas supply before converting fuels.
• Make all conversions before turning gas supply back on.
Failure to follow these instructions could result in fire,
explosion or other personal injury.
Models 1947, 1955 & 1956
All of our ranges are factory set to burn natural gas unless
“LP” is specified. If you are converting from Natural Gas
15
GAS-SUPPLY PRESSURE REQUIREMENTS*
Gas Type
Minimum Manifold
Pressure
Min. Gas-Supply
Pressure**
Natural Gas
Liquid Propane (LP)
5-in. Water Column
10-in. Water Column
6-in. Water Column
11-in. Water Column
*Gas-supply pressure for testing the regulator setting shall be at least 1 in. water
column (249 Pa) above the specified manifold pressure; **Max. gas-supply pressure
for all models: 1/2 psi.