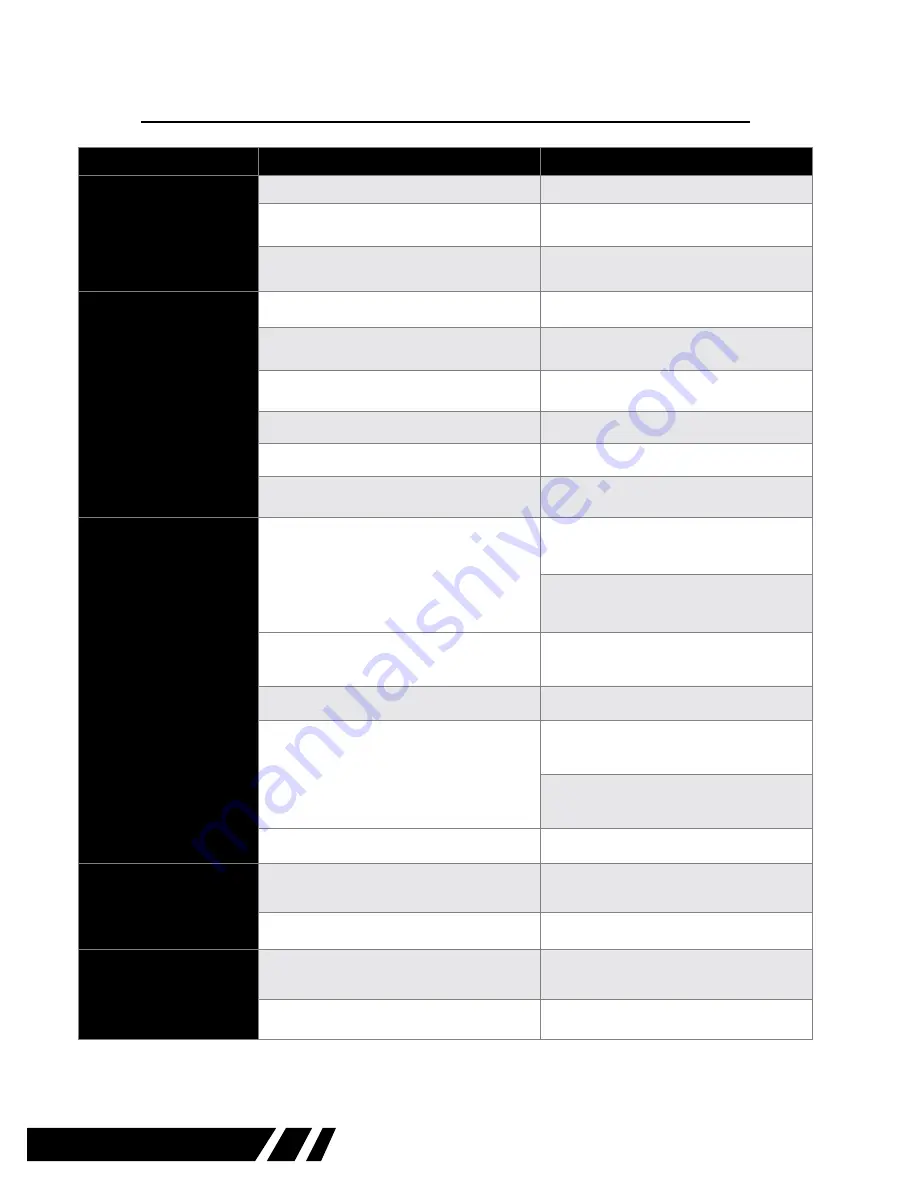
8
99400 Series
Troubleshooting Electric Rolling Motors
Symptom
Possible Causes
Solution
Motor won’t run.
Loose plug connections.
Ensure all plug connections are secure.
Motor voltage doesn’t match power source
voltage.
Ensure that motor voltage matches the volt-
age of the power source.
Torque controller is in “Auto” or “Assisted”
mode & is waiting for additional input.
Check the torque controller dialog
screen & enter info required.
Motor will not shut off at
controller setting.
Limit setting on the torque controller is set
too high.
Recalculate or reduce limit setting.
Torque required exceeds motor capacity.
Set motor speed (if 2 or 4-speed) to lower
speed or switch to larger motor.
Motor set at low speed setting
(2-or 4 speed motors only).
Set motor to high speed setting.
Motor is too large for application.
Switch to a smaller motor.
Trigger switch needs repair.
Replace the trigger switch.
Motor needs assessed by repair specialist.
Have the motor serviced by an
authorized repair specialist.
Motor runs hot.
Motor is operating at high temperatures and
is hot to the touch.
Run the motor outside of the tube in free
speed for 3 to 5 minutes to increase motor
air flow and decrease motor temperature.
Ensure the air vents on the motor cap are
rotated to the 12 o’clock and 6 o’clock
positions.
Motor is operating at or above
its max. amperage rating.
Set motor speed (if 2-or 4 speed) to lower
gear or switch to larger motor.
Ambient temperature are high.
See Care & Maintenance on page 9.
Air supply is being obstructed.
Check motor’s air vents for debris
or obstruction.
Ensure operator is not obstructing vents
with hand during operation.
Motor needs assessed by repair specialist.
Have the motor serviced by an authorized
repair specialist.
Motor will not
auto-reverse.
Loose plug connection.
Ensure plug connection to torque controller
is secure.
Motor is not auto-reversible
Motor must be manually reversed.
Motor is losing power.
Carbon brushes need replaced.
Replace brushes. See “Brush Replace-
ment” on page 10.
Proper amperage is not reaching motor.
Ensure power cord is proper length and
gauge.
Summary of Contents for 99400 Series
Page 2: ......
Page 6: ...6 99400 Series...