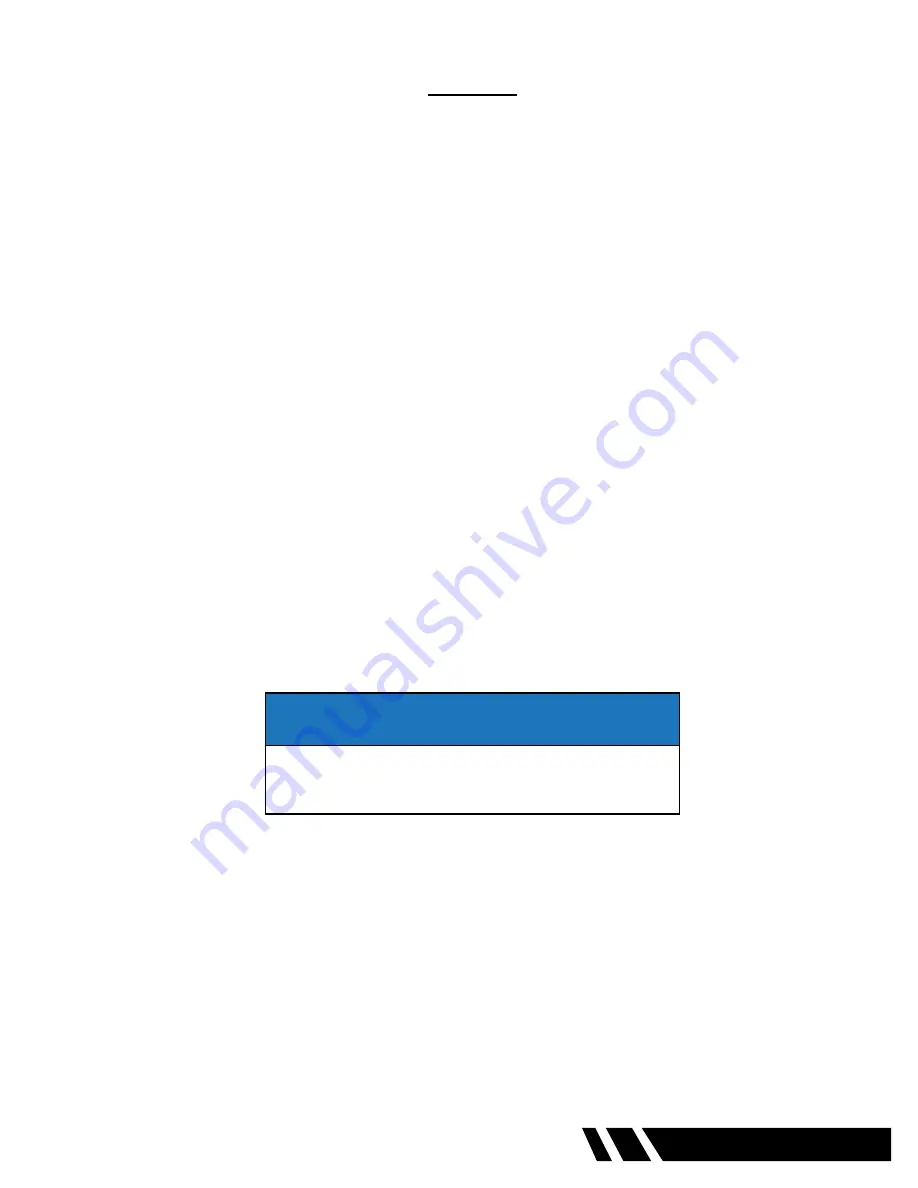
99400 Series
7
Setup
Speed Selection
DO NOT ATTEMPT TO CHANGE THE SPEED WHILE THE MOTOR IS RUNNING!
This motor is equipped with a mechanical four-speed gearbox. To select high speed, turn both dials
to the position indicated with a single dot. To select low speed, turn both dials to the position indicat-
ed with 2 dots. If the dial will not turn completely, rotate the spindle slightly by hand while still turning
the dial until the gearbox engages and the dial turns the full distance.
Operating this motor in the high speed selection will yield faster RPMs for higher productivity and less
torque than the low speed selection.
If the motor is running in the high speed selection and the torque controller is set at it’s highest limit
setting and the tubes are being under-expanded, switch the motor to the low speed selection and
rerun the torque controller setup. For increased productivity and to keep the motor cool, a higher RPM
setting is recommended.
Connect to Torque Controller
Reference ELC Setup information in TM-71.
To get full use of the torque shut-off feature, this motor must be used with the Elliott Model
ELC110220 Electronic Torque Controller. Connect the power cord on the motor to one end of the
included adapter cord and then connect the 7-pin connector on the adapter cord to the torque con-
troller receptacle. The controller will automatically detect that the motor is 220V. (Note: The operat-
ing voltage must correspond with the voltage indicated on the motor’s name plate. 99400-220 motors
designed for 220V can be used with 240V as well.
Be sure to familiarize yourself with the ELC110220 Operating and Maintenance Instructions (TM-71).
Handle
To rotate the handle:
1. Disconnect motor from any power source.
2. Remove carbon brushes (reference pg. 10 “Brush Replacement”).
3. Remove (4) front screws (Item 23).
4. DO NOT separate the gearbox (Item 70) from the gearbox plate (Item 18). Doing this may
void the warranty.
5. Separate gearbox plate (Item 18) from motor housing (Item 12) by no more than what is needed
for rotation (approximately 0.25”).
6. Rotate the handle to desired position.
7. Replace (4) front screws to secure the gearbox plate to the motor housing.
8. Replace carbon brushes (reference pg. 10 “Brush Replacement”).
NOTICE
NOTICE: Before rotating the handle, read all
documentation below. Failure to do so may
result in actions that void the warranty. .
Summary of Contents for 99400 Series
Page 2: ......
Page 6: ...6 99400 Series...