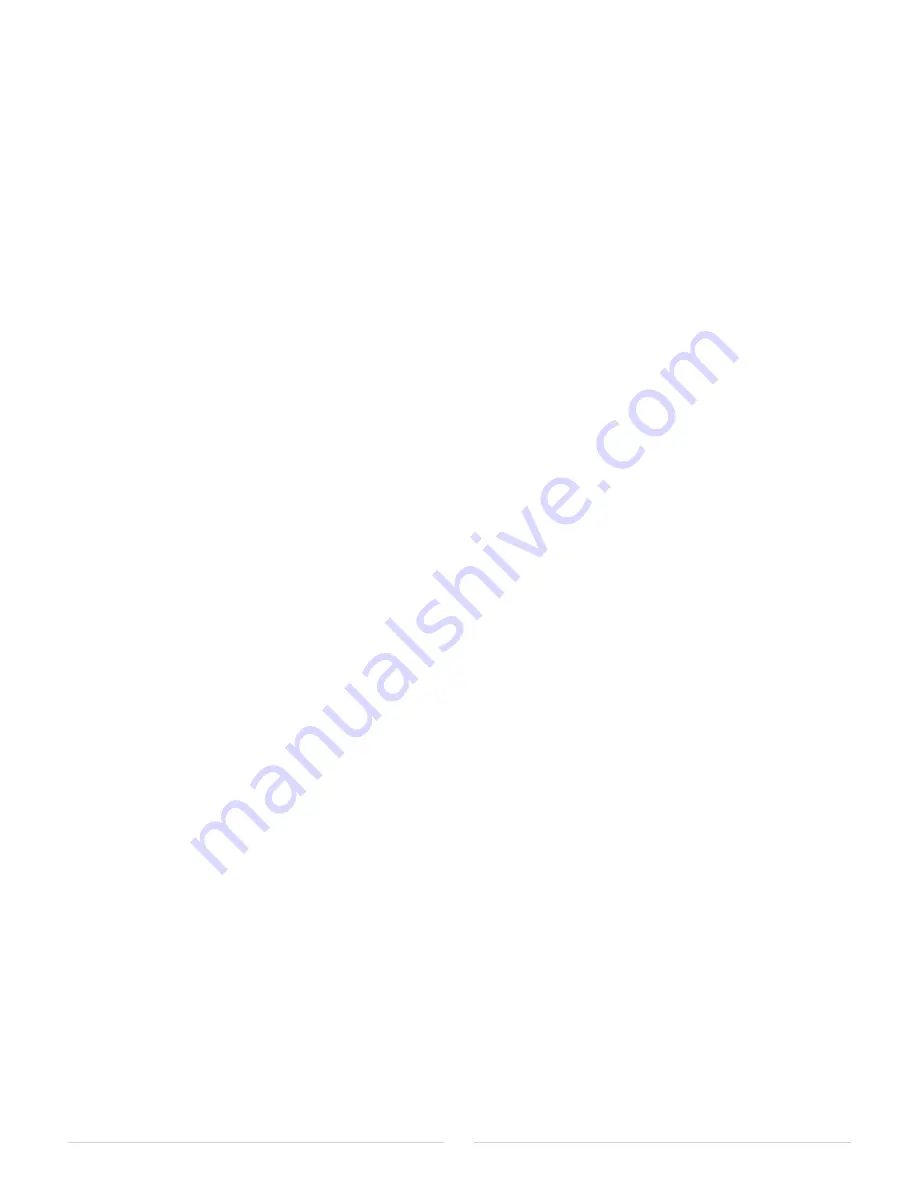
3-13
The values of these non-volatile registers should be set at the factory to allow proper
operation of the cannon with sufficient operating margin, but protect both the cannon
and external equipment from damage from collision. If the configuration of the cannon is
changed, such as inverted operation, or if the standard nozzle is replaced with a different
weight nozzle, then these parameters may need to be changed for correct operation.
The speed calibration is present in case the cannon is operated at alternate voltage, or the
speed profile has changed due to operational wear. Incorrect changes to these registers could
result in equipment malfunction and / or damage.
3-6.1 SPEED CALIBRATION
Typically, the speed is controlled in a closed loop with the motor PWM being automatically
adjusted as needed. This feature will need to be temporarily turned off so that we can set the
motors to move at a constant speed based on the Minimum Vertical or Horizontal PWM value,
and adjust the PWM value to meet the required speed. Currently, the minimum supported
speed of the cannon is 0.5 degrees / sec. We will use the Jog Commands with proper limits set
to operate the monitor and monitor the speed. Starting from 0, increment the PWM value and
execute a Jog move. If the monitor does not move, increase the value until movement starts.
Keep repeating until the desired speed of 0.5 degrees / second is meet.
Now, repeat these same jog commands but with the maximum speed (15 degrees/second)
programmed into the Jog commands. Slowly increase the PWM slope from 0 in small
increments such as .01 until the programmed maximum speed is reached. Typical values for a
cannon at 24 volts with a standard nozzle would be a PWM minimum of around 12 and a PWM
slope of around 0.325. Re-enable speed control when complete.
3-7.1 TORQUE CALIBRATION
Torque Calibration will determine the maximum torque that is required to detect an obstacle
or hard stop for the cannon. The minimum torque value is the amount of torque that is
required to stop a move in progress at the lowest programmed speed. This value is set such
that a known amount of torque is needed to stop the move in progress. This is measured by
placing a force gauge attached to an anchor point, and starting a Jog move with the minimum
speed of 0.5 degrees / second. Start from 0 and command a Jog move. If no movement stops
the value is set too low, so increase by small values such as .01 and repeat the Jog move until
movement starts without tripping the Torque Limit. Continue increasing until the force gauge
reads the desired minimum torque. This should be enough torque to allow movement under
maximum flow, but allow the movement to be stopped with a moderate amount of additional
force.
Repeat the above steps with the cannon set for maximum speed and increase the slope slowly
until the high speed operation is also stopped at the additional desired torque.