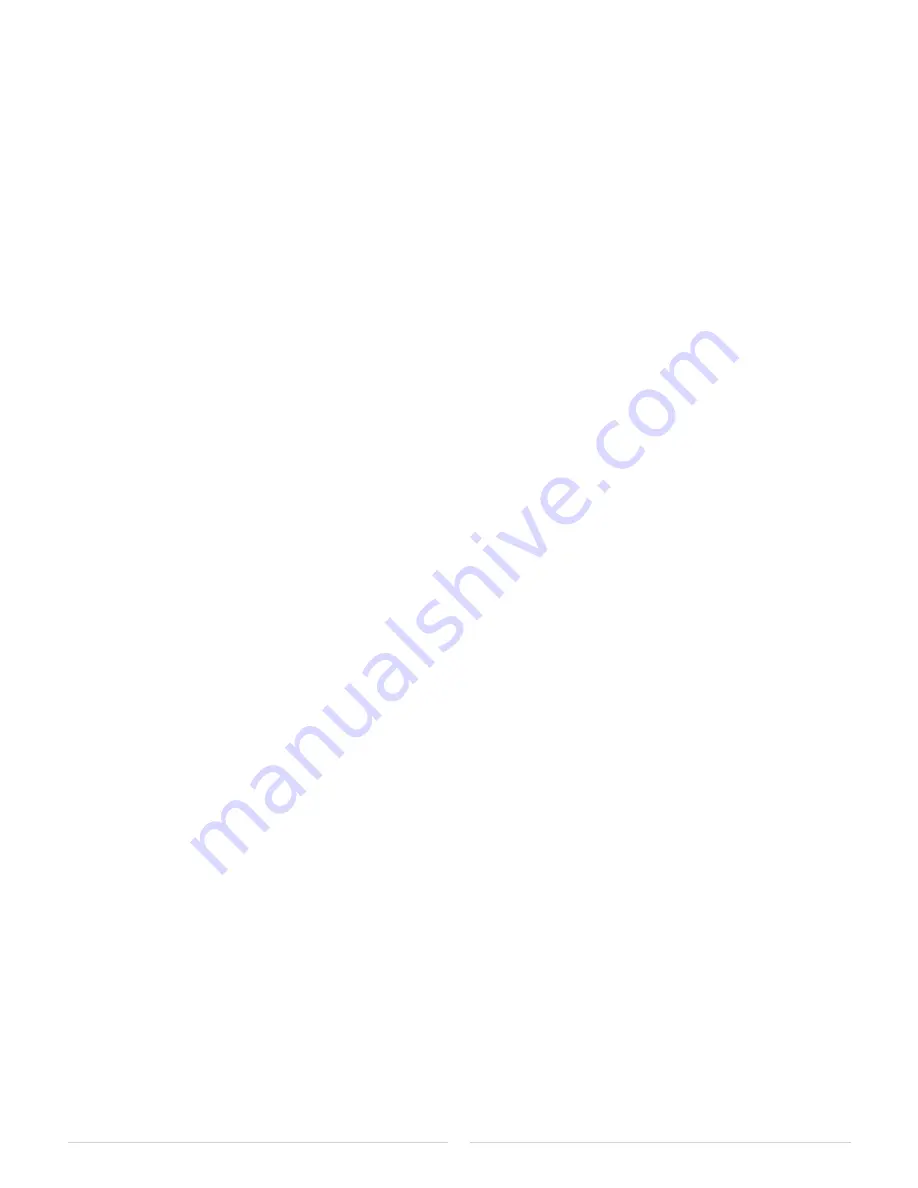
3-6
3-3.1 CALIBRATION MODE
Calibration mode is used to calibrate the absolute position sensors and set the initial position
of the cannon’s horizontal and vertical locations. Typically, this process is done once at the
factory and should normally not need to be repeated by the customer. In calibration mode,
there are no user or mechanical limits on the cannon, and damage and or injury can occur if
care is not taken. All position data returned to the controlling system in this mode is based
on uncalibrated sensor readings and do not indicate the actual position of the monitor. As a
safety precaution, Goto mode operations are disabled in calibration mode, since we do not
know the monitors actual position in regards to the calibrate points.
To calibrate a cannon, you will need to use the Jog mode commands to place the cannon
in the straight forward horizontal position
(Note: this position is marked by arrows on the
fixed base and movable body of the cannon. Ensure that the cannon is installed with the
base arrow pointing in the forward direction)
. You may move left and / or right using the Jog
commands, and can go past the horizontal mechanical stops in this mode. Once the horizontal
position is reached, you can use the vertical jog commands to place the vertical body is
straight up and level. If this setting is not precisely set to the straight up position, then there is
the possibility that when the cannon is commanded to go to the -45 degree mark, it will travel
into the lower vertical mechanical stop at around the -48 degree mark. If this occurs, reset the
monitor to its calibration points and recalibrate.
Calibration is initiated by executing a Calibration command from the PLC. In the event that
there is a sensor replacement and the cannon will need to be recalibrated in the field, there is
a Clear All Limits command, which will put it into calibration mode without any limits. Once
calibrated, the position sensor will report cannon position based on the washdown coordinate
system, and Goto commands are enabled.
3-3.1.1 USER LIMITS
Once the monitor has been calibrated, limits are automatically populated for both the hard ( or mechanical )
and user limits. The default hard limits are set to + / - 175 degrees in the horizontal axis and +90 / -45 de-
grees in the vertical axis. User limits are defaulted to + / - 90 degrees horizontal and +90 / -45 degrees verti-
cal. If needed, these limits can be modified one of two ways:
1. The PLC may issue a command that directly programs the limits to an absolute position without
needing to move the cannon there first. For example, to set the right horizontal user limit to +175
degrees, you would issue this command with 1750 in the absolute position field.
2. The other way of setting limits is to move the monitor to the position where you want to set
the limit and execute a set limit command with the current position as the desired limit. Once
all limits have been programmed, you are ready to use the cannon to do either Jog or Goto
commands.