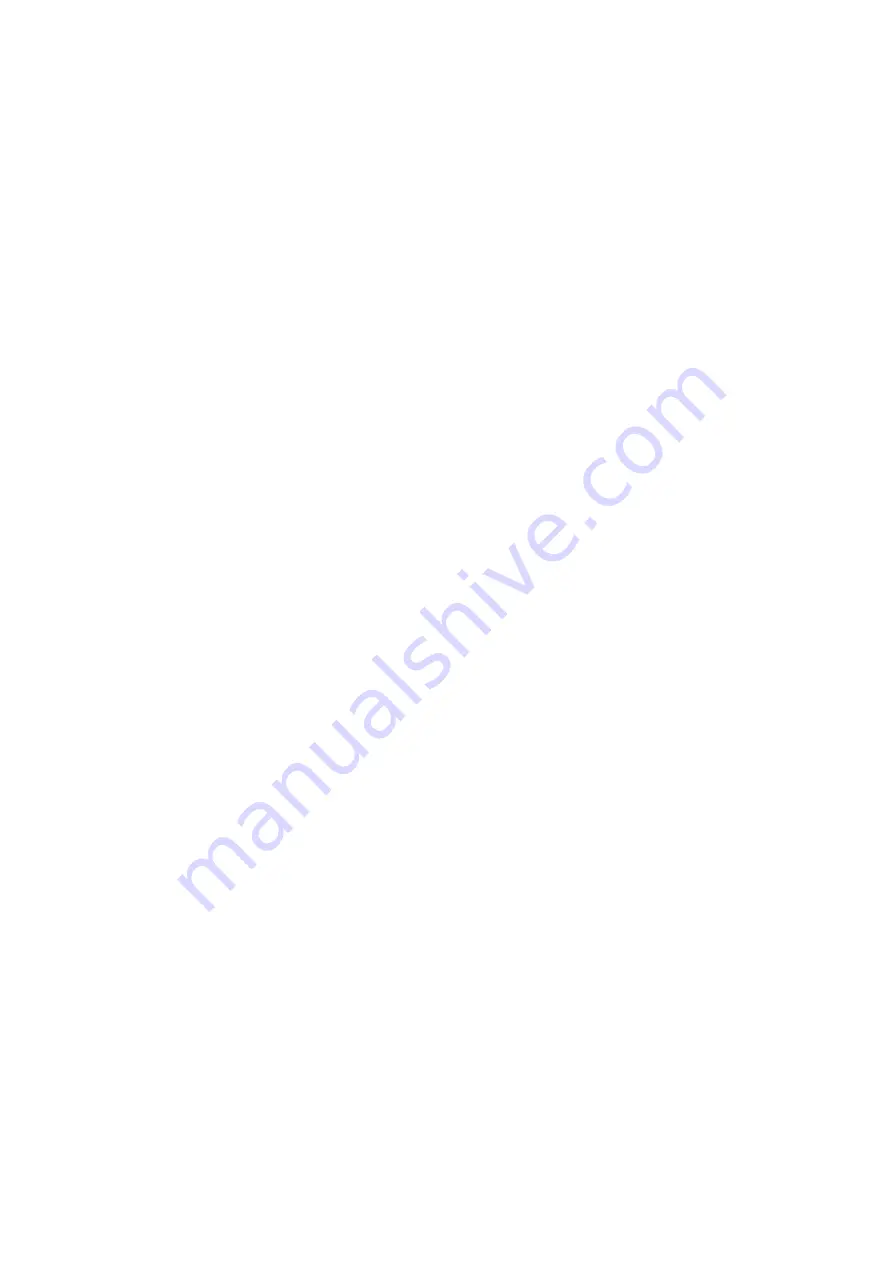
8
NOTES: The machine has also been designed for use in
environments with a pollution rating of 3. (See IEC 664).
1.4 ASSEMBLY AND ARRANGEMENT
Unpack the unit. Place the unit in a properly ventilated and,
if possible, non dusty room, making sure that the air inlet
and outlet from cooling slots are not obstructed.
This machine is suitable for manual torch type P 25
and we do not assume any responsibility in case that a
different kind of torch is used.
1.5. START-UP
The machine must be installed by qualified personnel. All
connections must be made in compliance with current
safety standards and full observance of safety regulations
(see CEI 26-23 - IEC TS 62081).
Connect the air supply to the fitting
L,
making sure that
pressure is 4,7 bar at least with a minimal capacity of 40
litres/min.
If the air supply comes from a pressure regulator of a
compressor or centralized system, the regulator must be
set to an output pressure of no more than 8 bar (0.8 Mpa).
If the air supply comes from a compressed air cylinder, the
cylinder must be equipped with a pressure regulator.
Never connect a compressed air cylinder directly to the
regulator on the machine! The pressure could exceed
the capacity of the regulator, which might explode!
Connect the power cord
P
: the yellow-green cable wire
must be connected to an efficient grounding socket on the
system. The remaining wires must be connected to the
power supply line by means of a switch placed as close as
possible to the cutting area, to allow it to be shut off quickly
in case of emergency.
The capacity of the cut-out switch or fuses installed in
series with the switch must be equal to the current I
1
eff.
absorbed by the machine.
The absorbed current I
1
eff. may be determined by reading
the technical specifications shown on the machine under
the available supply voltage U
1
.
Any extension cords must be sized appropriately for the
absorbed current I
1
max.
1.5.1 Motor-driven generators
They must have an electronic regulator of the tension, a
power equal to or greater than 2,5 kVA and must not
deliver a voltage greater than 260V.
2. USE
Switch the unit on by turning switch
N
(pict.2); this is shown
by LED
B
(pict.1) which is on.
ATTENTION! After turning on the machine, the first
pressure you do on the torch trigger will cause the
immediate strike of the pilot arc.
Check that, under this condition, the pressure shown on
gauge
K
(pict. 2) is 4,7 bar (0,47 MPA), otherwise adjust it
by means of pressure regulator knob
J
(pict. 2), then lock
this knob by pressing it down. Connect work clamp to the
piece to be cut. Set the cutting current by means of the
knob
H
(pict.1). Use the Ø 0,65 mm nozzle.
N.B. Cut quality is greatly improved if the nozzle is kept
in contact with the workpiece.
Make sure that the grounding clamp and workpiece have a
good electrical contact, especially with painted, oxidized or
insulated sheet metal.
Do not connect the grounding clamp to the part of the
material that is to be removed.
Press the torch trigger to strike the pilot arc.
If cutting does not begin within 2 seconds, the pilot arc
goes out; press the trigger again to re-strike it.
Hold the torch upright while cutting.
When you have finished cutting and released the trigger,
air will continue to leave the torch for approximately 100
seconds to allow the torch to cool down.
It is advisable not to turn the machine off until this
cool-down period is complete.
Should you need to make holes or begin cutting from the
centre of the workpiece, you must hold the torch at an
angle and slowly straighten it so that the nozzle does not
spray molten metal (see pict. 3). This must be done when
making holes in pieces more than 3 mm thick.
Do not keep the pilot arc lit in the air when not needed, to
avoid unnecessary consumption of the electrode, swirl ring
or nozzle.
Turn the machine off when the task is completed.
3. CUTTING ERRORS
3.1. INSUFFICIENT PENETRATION
This error may be caused by the following:
y
high speed. Always make sure that the arc fully
penetrates the workpiece and is never held at a
forward angle of more than 10 - 15°. This will avoid
incorrect consumption of the nozzle and burns to the
nozzle holder.
y
Excessively thick workpiece (see cutting speed
diagrams).
y
Grounding clamp not in good electrical contact with
the workpiece.
y
Worn nozzle and electrode.
y
Cutting current too low.
NOTE: When the arc does not penetrate, the molten metal
scraps obstruct the nozzle.
3.2. THE CUTTING ARC GOES OFF
This error may be caused by:
• worn nozzle, electrode or swirl ring
• air pressure too high
• supply voltage too low
3.3. TILTED CUTTING
When cutting appears tilted (see picture 4), switch the unit
off, loosen nozzle holder and turn nozzle by a quarter turn,
then lock and try again. Repeat this operation until cutting
is straight (see picture 5).
3.4. EXCESSIVE WEAR ON CONSUMABLE PARTS
This problem may be caused by:
a) air pressure too low compared to the recommended
level.
b) excessive burns on the end of the nozzle holder.
4. HELPFUL HINTS
y
If the system air contains considerable amounts of
moisture and oil, it is best to use a drying filter to avoid
excessive oxidation and wear on consumer parts,
damage to the torch and a reduction in the speed and
quality of the cutting.
y
The impurities in the air encourage oxidation of the
electrode and nozzle, and may make it difficult to
strike the pilot arc. If this occurs, use fine sandpaper
to clean the end of the electrode and the interior of the
Summary of Contents for 483
Page 2: ...2 1 2 3 4 5 6 7 8 ...
Page 23: ......