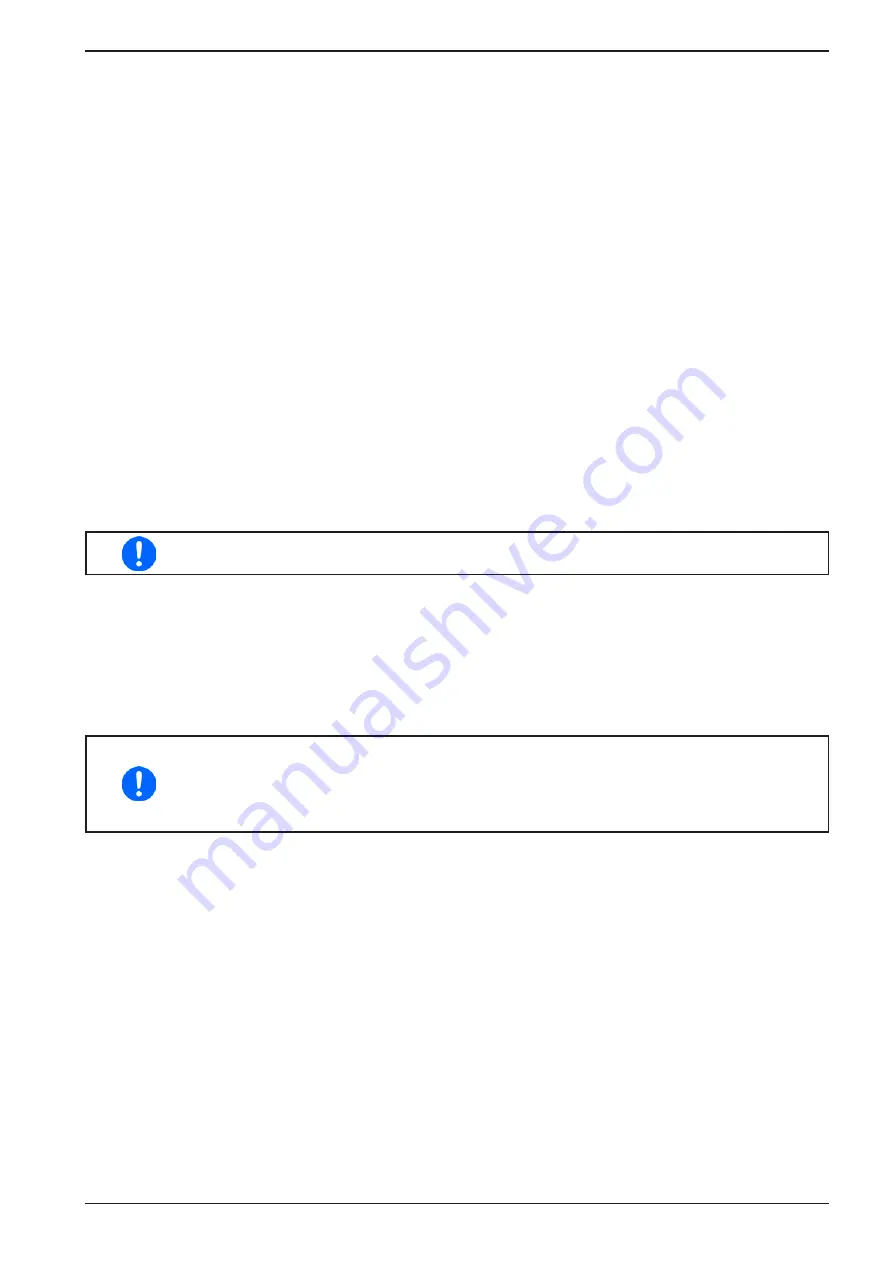
Page 86
EA Elektro-Automatik GmbH
Helmholtzstr. 31-37 • 41747 Viersen
Germany
Fon: +49 2162 / 3785-0
Fax: +49 2162 / 16230
www.elektroautomatik.de
ELR 9000 HP Series
3.11.3.3 Settings on the devices
The master-slave settings in the MENU also affect the Share bus. For correct 2QO operation, all involved load
units must be slaves on the Share bus. This is achieved by setting the master-slave mode to OFF or SLAVE, de-
pending on if there is digital master-slave in use or not. For the one load that is master (setting: MASTER) in the
master-slave system the additional parameter “PSI/ELR system” has to be activated.
On any of the power supplies, you need activate master-slave mode and set it to MASTER, unless it is already
the master unit of a master-slave system over digital MS bus. Refer to the documentation of the power supply for
further information. Also see
For safety of the connected E.U.T / D.U.T and to prevent damage, we recommend to adjust supervision thresholds
like OVP, OCP or OPP on all units to the desired levels, which will then switch off the DC output resp. the DC input
in case of excess.
3.11.3.4 Restrictions
After all electronic loads have been connected to the Share bus with one power supply as master, they cannot limit
their input voltage anymore to what you adjust as “U set” on the device. The correct voltage level comes from the
master unit via Share bus and is thus adjusted there.
3.11.3.5 Application example
Charging and discharging a battery with 24 V/400 Ah, using the wiring example in configuration A.
•
Power supply PSI 9080-170 3U with: I
Set
= 40 A (charging current, usually 1/10 of battery capacity), P
Set
= 5000 W
•
Electronic load ELR 9080-170 HP set to: I
Set
= max. discharge current of the battery (eg. 100 A), P
Set
= 5000 W,
UVD = 20 V with event type “Alarm” to stop discharging at a certain low voltage threshold
•
Assumption: the battery has a voltage of 26 V at test start
•
DC inputs resp. DC outputs on all units switched off
In this combination of devices it is recommended to always switch on the DC output of the
source first and then the DC input of the sink.
Part 1: Discharging the battery to 24 V
Setup: Voltage on the power supply set to 24 V, DC output of power supply and DC input of load activated
Reaction: the e-load will load the battery with a max. current of 100 A in order to discharge it to 24 V. The power
supply delivers no current at this moment, because the battery voltage is still higher than what is adjusted on the
power supply. The load will gradually reduce the input current in order to maintain the battery voltage at 24 V. Once
the battery voltage has reached 24 V with a discharge current of approx. 0 A, the voltage will be maintained at this
level by charging from the power supply.
The power supply determines the voltage setting of the load via the Share bus. In order to avoid
deep discharge of the battery due to accidentally setting the voltage on the power supply to a
very low value, it is recommended to configure the undervoltage detection feature (UVD) of the
load, so it will switch off the DC input when reaching minimum allowed discharge voltage. The
settings of the load, as given via the Share bus, can’t be read from the load’s display.
Part 2: Charging the battery to 27 V
Setup: Voltage on the power supply set to 27 V
Reaction: the power supply will charge the battery with a maximum current of 40 A, which will gradually reduce
with increasing voltage as a reaction to the changing internal resistance of the battery. The load absorbs no cur-
rent at this charging phase, because it is controlled via the Share and set to a certain voltage, which is still higher
than the actual battery voltage and the actual output voltage of the power supply. When reaching 27 V, the power
supply will deliver only the current needed to maintain the battery voltage.