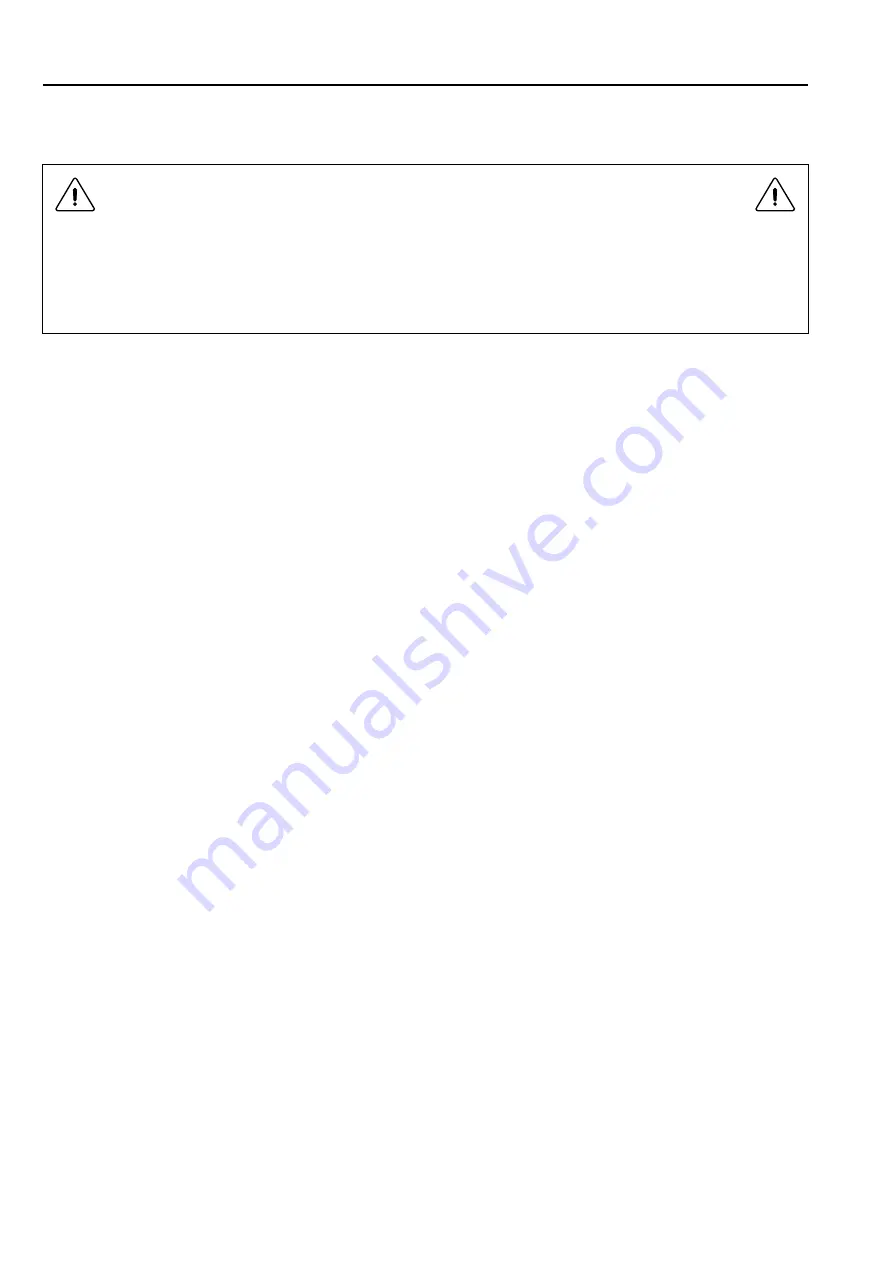
68
Installation manual
• Check the direction of rotation of the circulating pump and of the draught accelerator gas heating.
The exchangers of the gas heated machines have a water circulating pump.
Before the first start of the machine, you must check if this pump is priming well.
Therefore, it is necessary to fill the machine with water and to run only the circulating pump, without heating, by
pushing, with an isolated screwdriver, on the manual control of the exchanger's KM3 contactor.
To be sure that the pump is well primed (10 to 15 seconds), you must pay attention to a change in the running
noise when the water goes through the circuit.
• Check that the inner drum is empty.
• Open the manual valves controlling the water and steam supplies (for steam heating machines).
• Operate the machine manually to fill with cold water, then hot water. Check that these water supplies are con-
nected as they should be.
• Start the machine on wash action, and check that the motor is revolving alternately in the both ways, as normal for
wash action.
• Start heating by programming a final temperature. Check that the steam valve opens or the heating element relay
reacts, as appropriate.
• Check that the detergents container is working as they should.
• Check the water and steam connections and the drain valve for signs of any leakages.
• Empty the water from the machine and open its door.
Automatic operation
• Check that the external switch or switches are switched on and that the manual valves for water and steam (if the
machine has steam heating) are open.
• Run one of the machine's built-in (standard) with heating.
• Check that the program proceeds normally, and the water filling, detergent filling, heating and motor action are all
working in accordance with the program display on the display screen.
Final checking
If all function checks have been satisfactory, reassemble all protection casings.
Summary of Contents for WB6-20
Page 1: ...Installation manual Washer extractors WB6 20 WB6 27 WB6 35 Original instructions 05201148 EN ...
Page 2: ......
Page 25: ...Installation manual 25 Back view Right view Drain connection Top view ...
Page 47: ...Installation manual 47 No Barrier washer Barrier washer ...
Page 49: ...Installation manual 49 Front view Side view Top view Gas exchanger with draught accelerator ...
Page 62: ...62 Installation manual ...
Page 71: ......
Page 72: ...Electrolux Professional AB 341 80 Ljungby Sweden www electroluxprofessional com ...