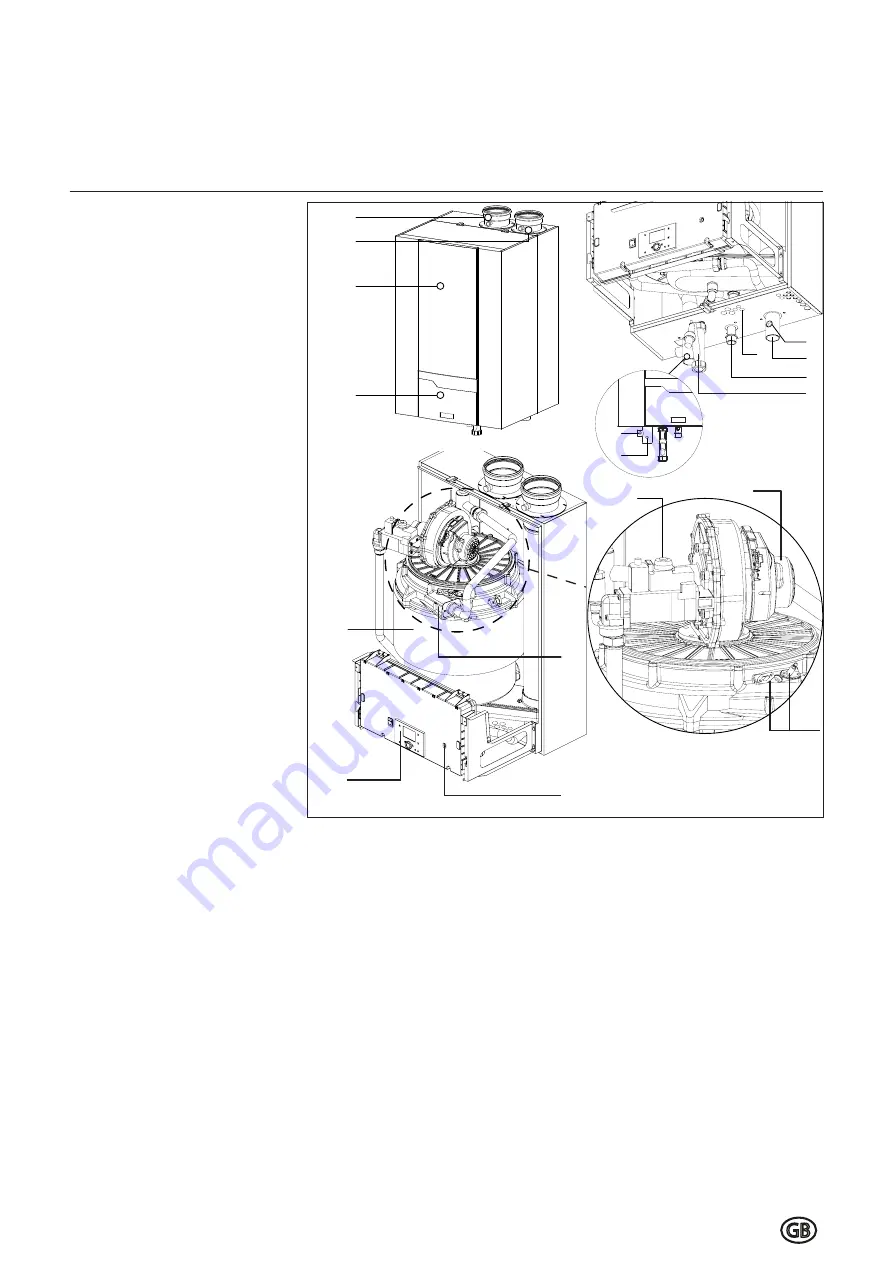
4
3
1
2
11
6
7
9
8
10
5
16
12
18
17
14
13
15
Construc on
GB
7
Layout of the boiler
Opera ng principle
Layout of boiler
The THISION L EVO boiler consists of
the following main components:
1. Casing
2. Access door to control panel
3. Flue gas connec on
(+ test point)
4. Air intake connec on
(+ test point)
5. Flow water connec on
6. Return water connec on
7. Gas connec on
8. Syphon
9. Input for wiring
10. Connec on for safety valve
11. Connec on for
fi
ll/drain valve
12. Control Panel
13. Fan
14. Gas valve
15. Igni on and ionisa on electrodes
16. Heat exchanger
17. Igni on transformer
18. Electrical input connec ons
Opera ng principle
The THISION L EVO is a fully modu-
la ng boiler.
The control unit of the boiler adapts
the modula on ra o automa cally
to the heat demand requested by
the system. This is done by control-
ling the speed of the fan. As a re-
sult, the venturi mixing system will
adapt the gas ra o to the chosen fan
speed, in order to maintain the best
possible combus on
fi
gures and
therewith the best e
ffi
ciency.
The
fl
ue gases created by the com-
bus on are transported downwards
through the heat exchanger and
leave the boiler at the top into the
chimney connec on.
The return water from the system
enters the boiler in the lower sec-
on, where is the lowest
fl
ue gas
temperature in the boiler.
In this sec on condensa on takes
place. The water is being transport-
ed upwards through the heat ex-
changer, in order to leave the boiler
at the
fl
ow connec on. The cross
fl
ow working principle (water up,
fl
ue gas down) ensures the most ef-
fi
cient combus on results.
The LMS14 control unit can control
the boiler opera on based on:
• Boiler control
(stand alone opera on);
• weather compensated opera on
(with op onal outdoor sensor);
• with 0-10V external in
fl
uence (tem-
perature or capacity) from a build-
ing management system.
Summary of Contents for Thision EVO WH 250-120
Page 1: ...Operation and Installation manual THISION EVO WH 08 2016 PAG THEWH01...
Page 2: ......
Page 4: ......