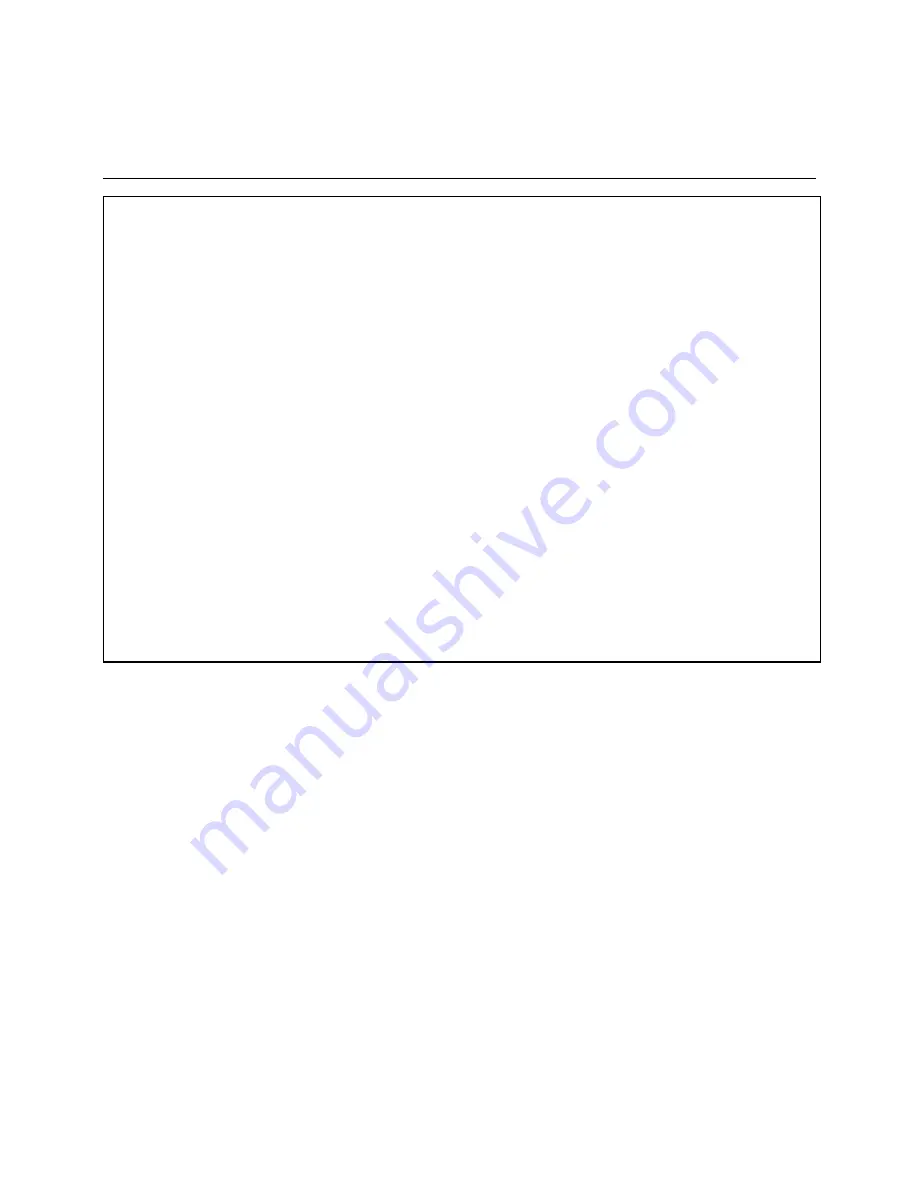
21
Ignition Burner Type ZT0
Technical Data
Construction according to sectional
drawing
The igniter consists mainly of the trans-
former unit (Item 1) housing the ignition
transformer, the igniter tube with air and
mounting flange (Item 6), a gas tube (9)
with nozzle (11) and the electrode car-
rier ring (10). The igniter tube with the
Rp1 air connection is bolted to the
transformer unit. After the 4 bolts (Item
4) have been unscrewed it may be
removed or turned by 90° if required by
the position of the air connection. When
turning the tubes care must be taken
not to change the position of the inner
supporting rings and rods because this
might lead to operational trouble.
The gas supply may be connected eit-
her to the left-hand or right-hand ope-
ning. The opening not used is closed
with a screw plug which also carries the
screw-in gas test socket (3). The elec-
trode support ring (Item 10) is mounted
to the end of the gas tube.
The ionization electrode and ignition
electrode are extended with connecting
rods (Item 8). These rods are installed
through the bottom of the transformer
housing in 2 ceramic insulators and car-
ried by intermediate supporting rings
(Item 7) spaced at 300 mm.
Flame monitor
An ionization electrode is provided for
flame monitoring. The flame signal is
generated by d.c. current which due to
the ionization effect and the rectifier
effect of the flame is caused to flow from
the igniter tube earth via the flame to
the ionization electrode and via the con-
necting rod to the amplifier in the auto-
matic furnace controller. The ionization
electrode and ignition electrodes are
adjusted in accordance with the dra-
wing.
When installing new electrodes these
must be bent, cut to length and adjusted
as required.
The internal resistance of the ionization
system amounts to some megohms.
Such a high resistance ensures a good
insulating capacity of the electrodes and
connecting rods. In a dust-laden com-
bustion air environment it is therefore
important to clean the insulators at shor-
ter intervals. Humidity should be kept
out. See also electrical function.
The ceramic insulator of the ionization
electrode must not be allowed to heat
up above 500 °C because this could
lead to shutdown on trouble. Therefore,
a minimum air flow rate (10-20 % of the
full-load rate) should be allowed to flow
if this temperature is likely to be rea-
ched by radiation or convection with the
furnace chamber in hot condition and
the burner flame turned off.
Technical data of ignition gas burner type ZT0
Fuel
gases according to G 260
Flame power
max. 120 kW
Flame length
max. 600 mm
Gas connection
Rp 1/2 right or left
Air connection
Rp 1, may be turned by 4x90°
Air flow rate
max. 50 m³/h
Air index
0.3-0.5; remaining air rate must be available from furnace chamber
Max. ambient
temperature
500°C in tube; if temperature is higher, keep combustion air
connected partly as cooling air; 0°C to +60°C in transformer unit
Transformer unit
Connection voltage 230 V, 50 Hz
Connector type
plug connector
Power input
ignition transformer 100 VA, 20% duty cycle (with thermal winding shield)
ignition 5 kV (2-3 seconds via automatic furnace controller)
Ambient temperature 0°C to +60°C
Degree of protection IP 54
Electrical connection
Cl. 1 (Mp)
Cl. 8 (Ph)
ignition transfer, primary Use shielded cable Z 912 F 00 for flame feedback.
Cl. 10
ionization signal
NOTE:
The shield must not make contact with earth.