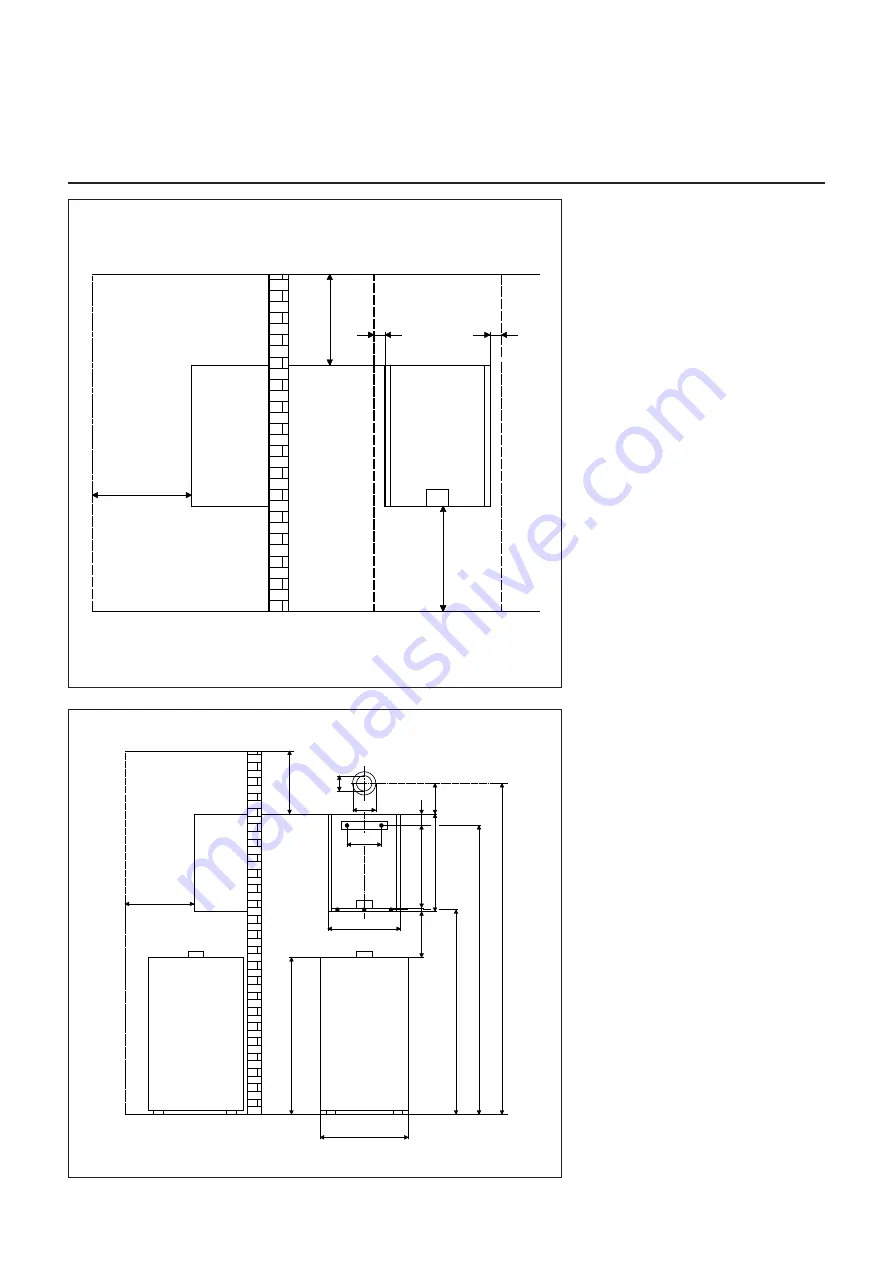
Installation
Minimum clearances
9
450
21
0
50
50
30
0
305
336
7
67
2
72
75
0
15
5
m
in
.3
00
m
ax
.3
50
550
84
0
450
21
0
40
0*
m
in
.2
04
5
m
ax
.2
09
59
125
80
m
in
.
20
45
m
ax
.2
09
5
m
in
.
18
19
m
ax
.1
86
9
m
in
.
11
47
m
ax
.1
19
7
120 Liter
150 Liter **
Minimum clearances
For servicing of heating appliance the
minimum clearances specified in the
diagram must be observed.
Wall mounting
Mount the heating appliance with the
aid of the positioning device and a
spirit level*.
Affix the metal bracket to the wall by
means of the expansion anchor to be
used and hang the heating appliance.
* with fitted expansion tank
** with 150 l tank
vertical mass + 178 mm