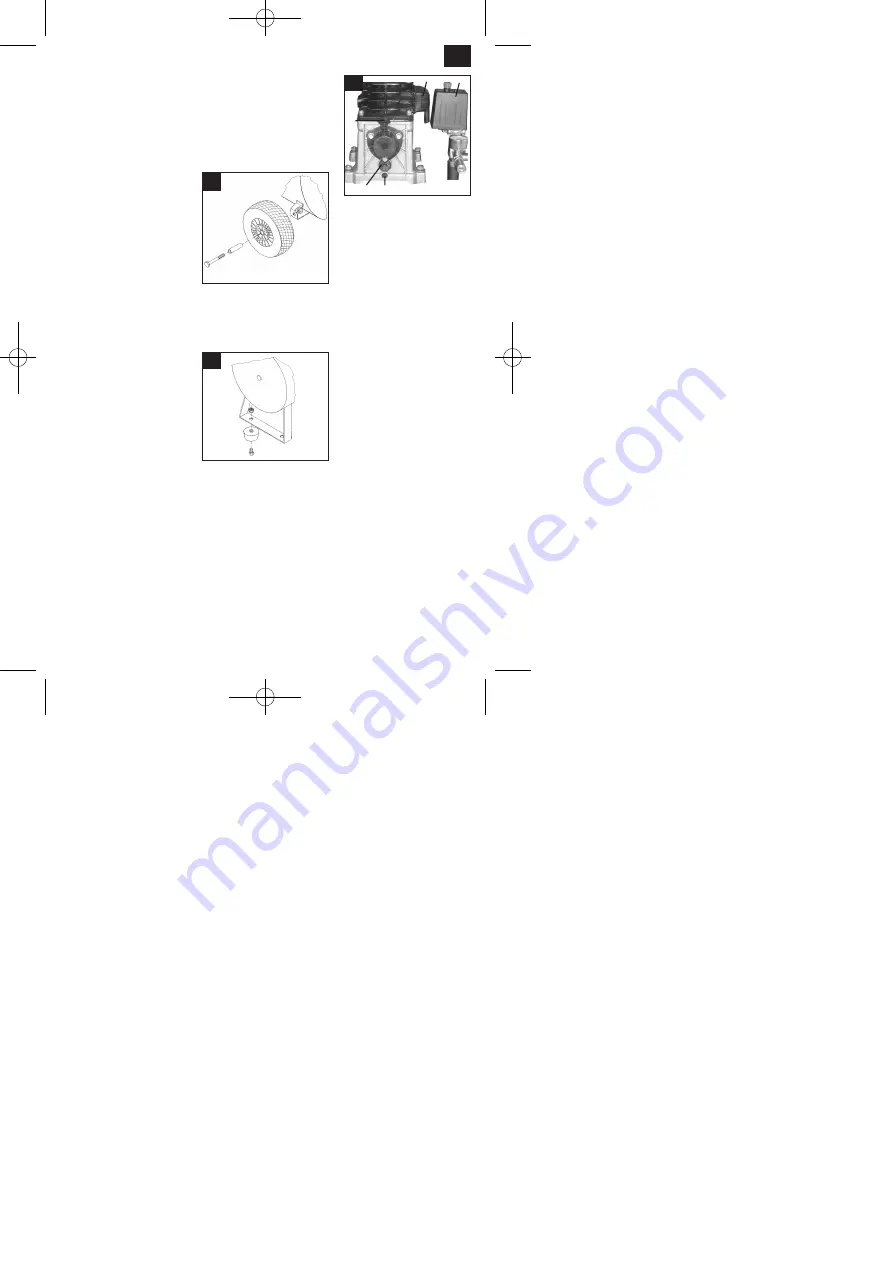
11
packaging of the processed
material, must be observed.
Additional protective measures
are to be undertaken if
necessary, particularly the
wearing of suitable clothing and
masks.
●
The work room has to be
bigger than 30 m
3
and have
sufficient ventilation for
spraying and drying. Never
spray into the wind.
It is always imperative to
observe the regulations of your
local police authorities when
spraying combustible or
hazardous substances.
●
Never process media such as
white petroleum spirit, butyl
alcohol and methylene chloride
with the PVC pressure hose
(reduced life span).
Operation of pressure
vessels in accordance
with the pertinent
pressure vessel
regulations
1. An operator of a pressure
vessel is required to keep the
pressure vessel in good
working order, to operate it
properly, to supervise its use,
to carry out essential
maintenance and repair work
immediately, and to introduce
essential safety measures
according to requirements.
2. The supervisory authorities
may order essential safeguards
from case to case.
3. A pressure vessel may not be
operated if it has any defects
which constitute a danger to
employees or third parties.
4. The pressure vessel must be
regularly inspected for damage,
e.g. rust. If you discover any
damage, then please contact
the customer service
workshop.
Putting the compressor
into operation
Assembling the wheels (1):
The enclosed wheels must be
assembled in accordance with
Diagram 1.
Make sure that the valve is
positioned on the outside.
Assembling the rubber buffer
The enclosed rubber stops must
be assembled on the supporting
foot in accordance with Diagram
2.
Replacing the oil filter and
installing the air filter (fig. 3)
Use a screwdriver to remove the
oil filter plug and insert the
supplied stopper (2) in the
opening.Important! Check the oil
level.
Changing the air filter:
Unscrew the guard hood of the
pushbutton switch (5). The air
filter (1) can now be bolted to the
side of the pump, or
disconnected.
Connecting to the power
supply:
The compressor is equipped with
a mains cable with shock-proof
plug. This can be connected to
any 230V ~ 50Hz shock-proof
socket which is protected by a 16
A fuse. The motor is protected
against overload by a thermal
overload switch. If the rated
current is exceeded, the overload
switch shuts down. After the
overload switch has shut down,
the pressure switch should be
switched off (see Figure 4). After
a short cooling down period, the
overload switch switches itself
back on again.
By pressing the ON/OFF switch
on the pressure switch, the
compressor can be switched on
again. Long supply cables,
extensions, cable reels etc. cause
a drop in voltage and can impede
motor start-up. In the case of low
temperatures below 0°C, motor
start-up is jeopardized as a result
of stiffness.
Explanation of the compressed
air fittings
1 Pressure switch
2 Safety valve
3 Pressure gauge (to indicate the
vessel pressure)
4 Pressure gauge (to indicate the
set pressure)
5 Pressure reducing valve
(pressure setting)
6 On/Off switch
GB
1
2
3
���
���
���
���
���
Anleitung Euro 4000-1_SPK1:Anleitung Euro 4000-1_SPK1 22.02.2007 13:22 Uhr Seite 11