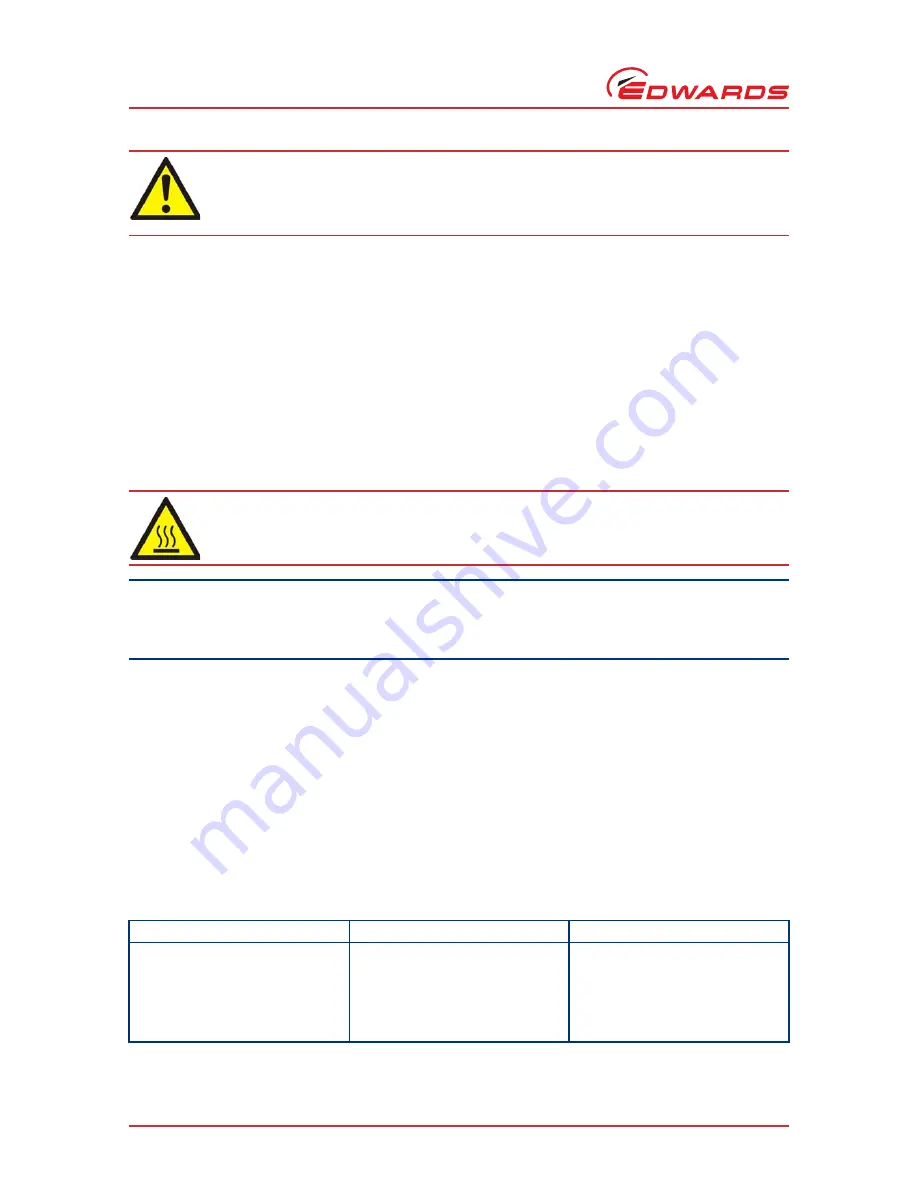
B800-00-880 Issue D
Page 64
© Edwards Limited 2013. All rights reserved.
Edwards and the Edwards logo are trademarks of Edwards Limited.
Operation
If the electrical supply to the nEXT pump fails when the pump is rotating, the motor of the pump is used as a
generator. The regenerated power is used to maintain the output signals on the logic interface (such as the normal
signal and serial communications), to power the three indicator LEDs on the controller and to maintain power at the
controller output (to control the vent valve, if fitted).
As the pump rotational speed decreases, the motor's ability to generate power also decreases until it is no longer
able to maintain power to the logic interface or LEDs. This will occur at speeds below 50% full rotational speed. In
this case, there will be no indication of pump rotational speed, yet the impeller may still be turning.
When the power is reinstated after a power failure, the behaviour of the pump will depend on the control mode at
the time of failure (parallel or serial) and the length of time the pump was without power.
Table 24
shows a number
of scenarios.
4.10
Bakeout
CAUTION
Pumps with ISO flanges are not suitable for bakeout, only pumps with CF flanges must be used. When baking the
pump to above 70 °C at the inlet flange, the pump must be water cooled to prevent damage to the bearing
lubricant.
If the pump (and the vacuum system) are heated, the degassing process will speed up and the pump will reach
ultimate vacuum in the shortest possible time. Heating the pump will also prevent condensation of vapours inside
the pump.
The Edwards BX bakeout band may be used to heat the pump (refer to
Section 7.4
). Fit the appropriate band around
the pump, just below the CF inlet flange. When baking the pump or the system, make sure that the temperature of
the inlet flange does not exceed the values specified in
Table 2
.
When baking the vacuum system, if the temperature of the system exceeds 200 °C, put a radiation shield between
the system and the pump. This radiation shield will reduce the heat radiated onto the pump rotor.
Typically, a bakeout of four hours is long enough to remove water condensation from the pump. However, the
bakeout time will depend on the amount of condensation in the pump and the vacuum system, and the ultimate
pressure desired.
WARNING
If the parallel start control signal on the logic interface connector is set to start, the pump may
automatically restart when the electrical supply is restored after an electrical supply failure.
Ensure that people cannot be injured by the rotating blades of the pump.
WARNING
Do not touch the bakeout band or surrounding surfaces during the bakeout process as they will be
hot.
Table 24 - Behaviour of a pump when the power is re-instated after an electrical supply failure
Length of power failure
Control mode
Behaviour of pump
Power is reinstated before pump
rotational speed falls below 50%
Either parallel or serial control mode Regenerative power maintains all
output signals during the power
failure. The pump will ramp to its
designated speed as quickly as
possible after the power has been
restored.