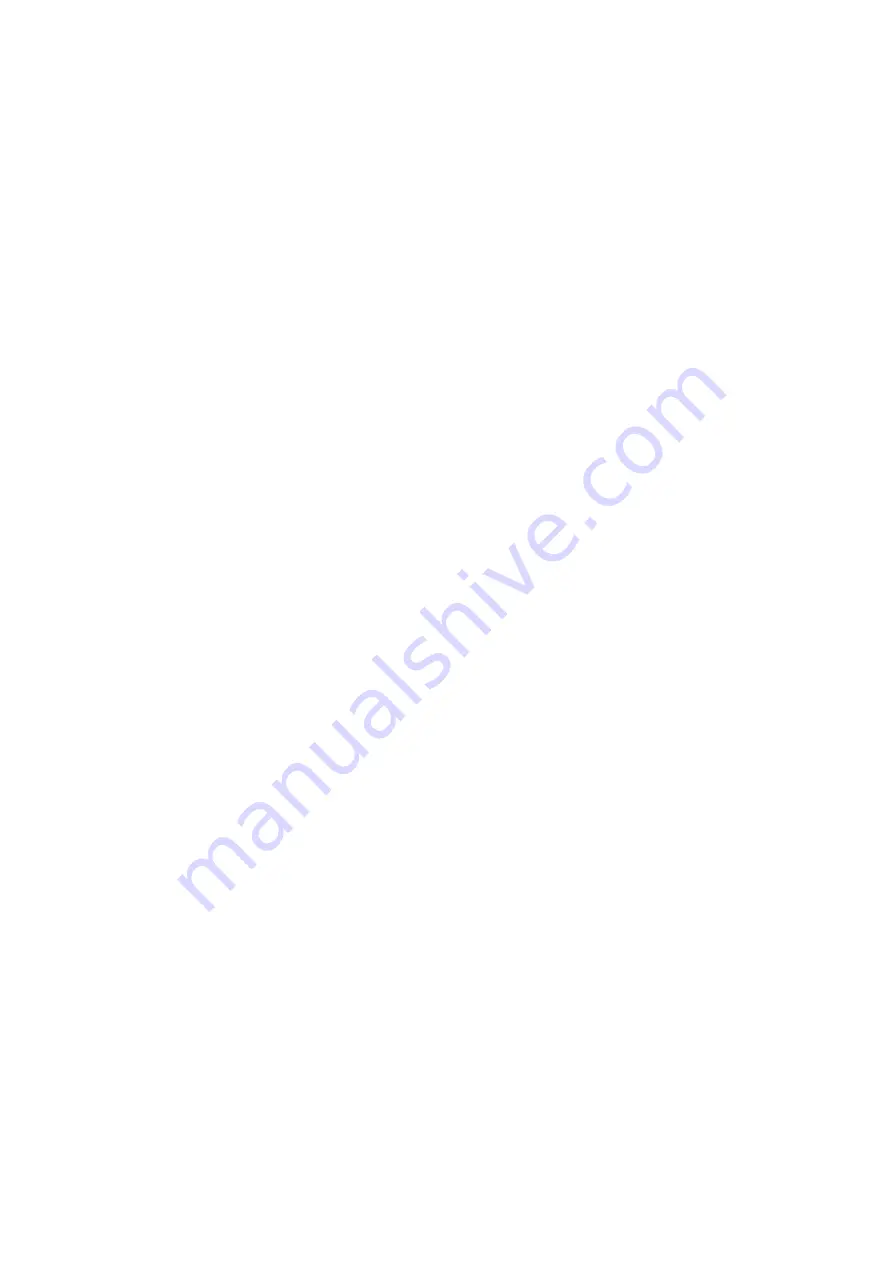
▪
The electrical supply voltage is too high.
▪
The exhaust filter or exhaust line is blocked.
▪
The oil level is too low.
▪
The pump is filled with the wrong type of oil.
▪
The oil is contaminated.
▪
The process gas is too hot or the throughput is too high.
7.5 The vacuum is not maintained after the pump is switched off
▪
The gas-ballast control is open.
▪
O-ring(s) are damaged or missing.
▪
The shaft seals have deteriorated.
7.6 The pumping speed is poor
▪
The connecting pipelines are too small in diameter.
▪
The connecting pipelines are too long.
▪
The inlet-filter is blocked.
7.7 There is an external oil leak
▪
The oil pump shaft seal is worn or damaged.
▪
The oil box gasket has deteriorated.
▪
There is an oil leak from gas-ballast control.
▪
There is an oil-leak from the drain-plug.
Page 33
A37132880_F - Fault finding
Summary of Contents for A37104902
Page 43: ...Page 41 A37132880_F Service...
Page 44: ...edwardsvacuum com...