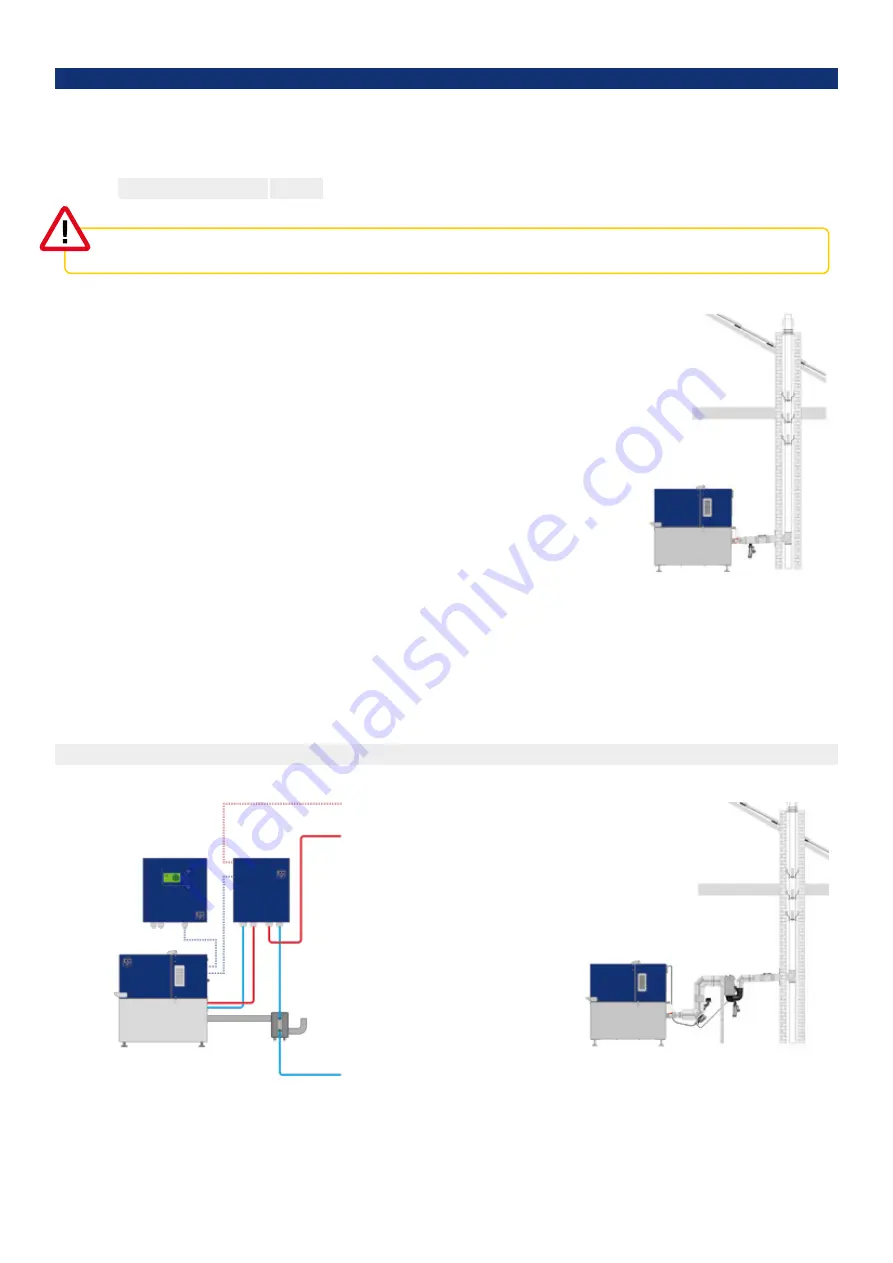
XRGI
®
- INSTALLATION GUIDE
VERSION 1.0 2018
52
C O N D E N S I N G E X H A U S T
G A S H E AT E X C H A N G E R
to the Storage Tank
from the Storage Tank
5.2
E X H A U S T G A S S I D E I N S TA L L AT I O N
5.2.1 E X T E R N A L E X H A U S T H E AT E X C H A N G E R
E x h a u s t g a s c o n n e c t i o n o n t h e P o w e r U n i t
X R G I ® 6 / 9 / 1 5 / 2 0
DN 60
Discharge the exhaust gases from the Power Unit through an exhaust gas pipe. Install the exhaust gas system in accordance with
regulations applicable in the country of installation.
Make sure that the fresh air intake and the exhaust gas pipes comply with installation
type B (room air dependent). Only permit a qualified fitter to connect up the system.
The installation regulations of the exhaust system manufacturer are to be observed.
The Power Unit is not designed for condensing operation, nevertheless install a conden-
sate drain to trap and discharge any condensation produced when the system starts
up. Fit a condensate box with a large water reserve or a trap with a ball valve or similar
to prevent the condensate drain from drying out. Use exhaust gas lines that comply
with temperature class T160 or higher, since the exhaust gas temperatures involved are
continuously close to the permissible limit and the XRGI® system mainly runs for long
periods of time.
Make sure that the exhaust gas system is pressure-tight (pressure-resistant to 5,000 Pa,
type H1 or H2). Do not route condensate and exhaust gas pipes horizontally. Ensure that
they have a minimal gradient of 5% to allow the condensate to run off. Make sure that
the length of the exhaust gas line, with an internal diameter of 80 mm and up to five
bends, does not exceed 20 metres. Extrapolate in line with EN 13384 as required if there
are more than five bends or if the pipe is longer.
In principle, each XRGI® system needs a separate exhaust gas pipe. Exhaust gas pipes can be cascaded from the Power Unit side, but
the exhaust pipe must be approved for this purpose by the manufacturer. You may have to extrapolate the pressure conditions in line
with EN 13384.
You can add an external exhaust heat exchanger to the Power Unit to improve its thermal efficiency. However, a notable increase
in output can only be achieved in condensing operation. The return temperatures from the heating system should permanently lie
below 45 to 50 °C. After the external exhaust heat exchanger, flue pipes with approval 120 ° C (PP) are permitted.
Ensure that the exhaust gas pipe is gas-tight. Comply with all national fire regulations!
Fig. 5.18 – Assembly example
Fig. 5.16 – Assembly example
Fig. 5.17