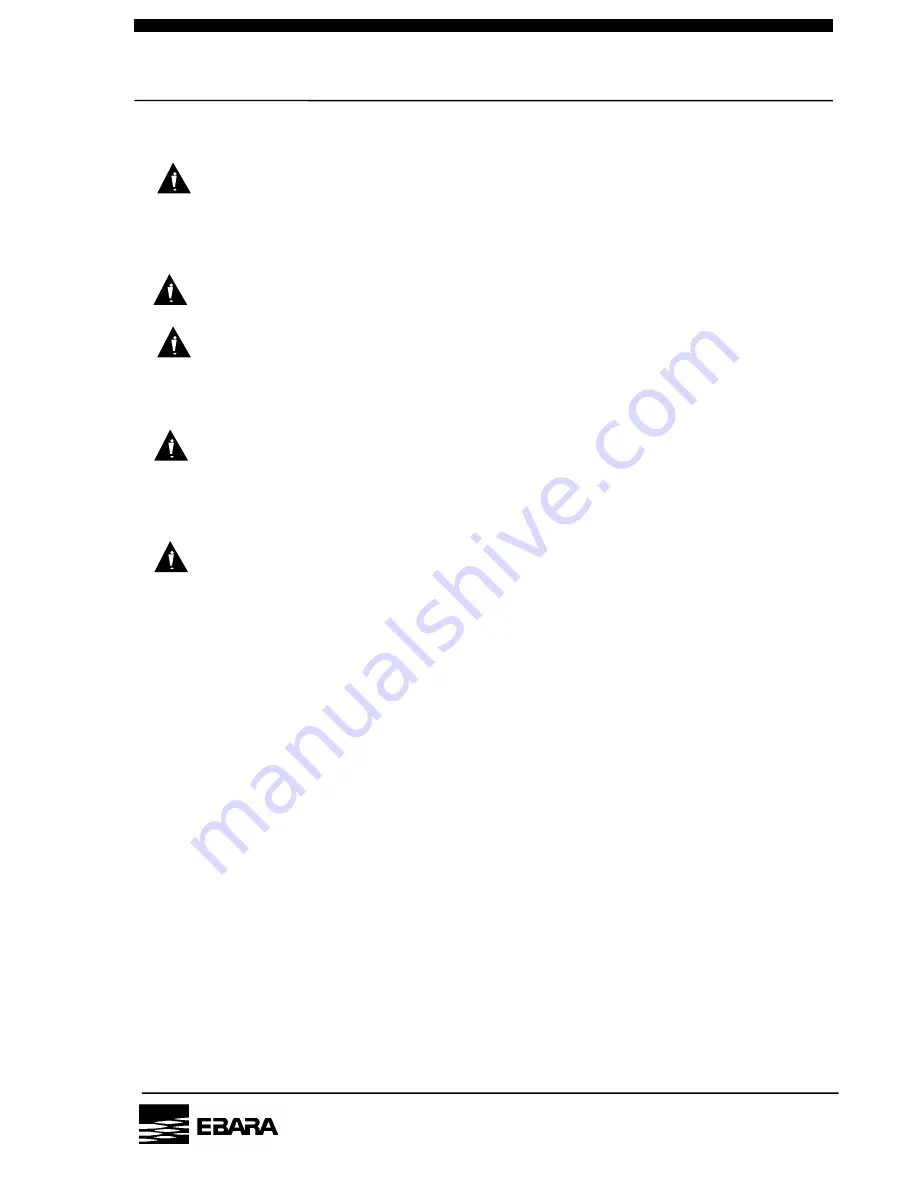
P.45
4.3 Electrical Wiring
WARNING
Be sure to keep the power supply to the pump turned off and
lock-outed until you have finished the wiring and connecting
work. Also interrupt the Circuit Protector (CP) during this.
WARNING
Electrical wiring shall be carried out only by qualified electricians.
CAUTION
Do not apply the power supply from the pump's power pack to
any other equipment as this will result in malfunctioning of the
control units and in pump failure.
CAUTION
CB is not installed in the pump unit. Please install CB based on
the law and the standard in the installation region. (Please attach
the Circuit breaker(CB) type of UL489 to SEMI correspondence.)
CAUTION
Do not supply a power supply to other instruments out of a pump
package. It becomes an operation mistake of a control part, and
a cause of pump failure.
PM10U
EBARA
CORPORATION
Summary of Contents for EV-S100
Page 10: ...viii LOCATION WARNING LABEL1 PM10U EBARA CORPORATION...
Page 11: ...ix LOCATION WARNING LABEL2 PM10U EBARA CORPORATION...
Page 16: ...xiv PM10U EBARA CORPORATION...
Page 33: ...P 14 3 5 3 Outline Drawing MODEL EV S20 OUTLINE DRAWING PM10U EBARA CORPORATION...
Page 34: ...P 15 MODEL EV S20P EV S 20N OUTLINE DRAWING PM10U EBARA CORPORATION...
Page 35: ...P 16 MODEL EV S50 OUTLINE DRAWING PM10U EBARA CORPORATION...
Page 36: ...P 17 MODEL EV S50P EV S50N OUTLINE DRAWING PM10U EBARA CORPORATION...
Page 37: ...P 18 MODEL EV S100 OUTLINE DRAWING PM10U EBARA CORPORATION...
Page 38: ...P 19 MODEL EV S100P EV S 100N OUTLINE DRAWING PM10U EBARA CORPORATION...
Page 39: ...P 20 MODEL EV S200 OUTLINE DRAWING PM10U EBARA CORPORATION...
Page 40: ...P 21 MODEL EV S200P EV S 200N OUTLINE DRAWING PM10U EBARA CORPORATION...
Page 41: ...P 22 MODEL EV S20 OUTLINE DRAWING OPTION PM10U EBARA CORPORATION...
Page 42: ...P 23 MODEL EV S20P EV S 20N OUTLINE DRAWING OPTION PM10U EBARA CORPORATION...
Page 43: ...P 24 MODEL EV S50 OUTLINE DRAWING OPTION PM10U EBARA CORPORATION...
Page 44: ...P 25 MODEL EV S50P EV S50N OUTLINE DRAWING OPTION PM10U EBARA CORPORATION...
Page 45: ...P 26 MODEL EV S100 OUTLINE DRAWING OPTION PM10U EBARA CORPORATION...
Page 46: ...P 27 MODEL EV S100P EV S 100N OUTLINE DRAWING OPTION PM10U EBARA CORPORATION...
Page 47: ...P 28 MODEL EV S200 OUTLINE DRAWING OPTION PM10U EBARA CORPORATION...
Page 48: ...P 29 MODEL EV S200P EV S 200N OUTLINE DRAWING OPTION PM10U EBARA CORPORATION...
Page 56: ...P 37 EV S20 LOCATION FIXTURE PM10U EBARA CORPORATION...
Page 57: ...P 38 EV S50 LOCATION FIXTURE PM10U EBARA CORPORATION...
Page 58: ...P 39 EV S100 LOCATION FIXTURE PM10U EBARA CORPORATION...
Page 59: ...P 40 EV S200 LOCATION FIXTURE PM10U EBARA CORPORATION...