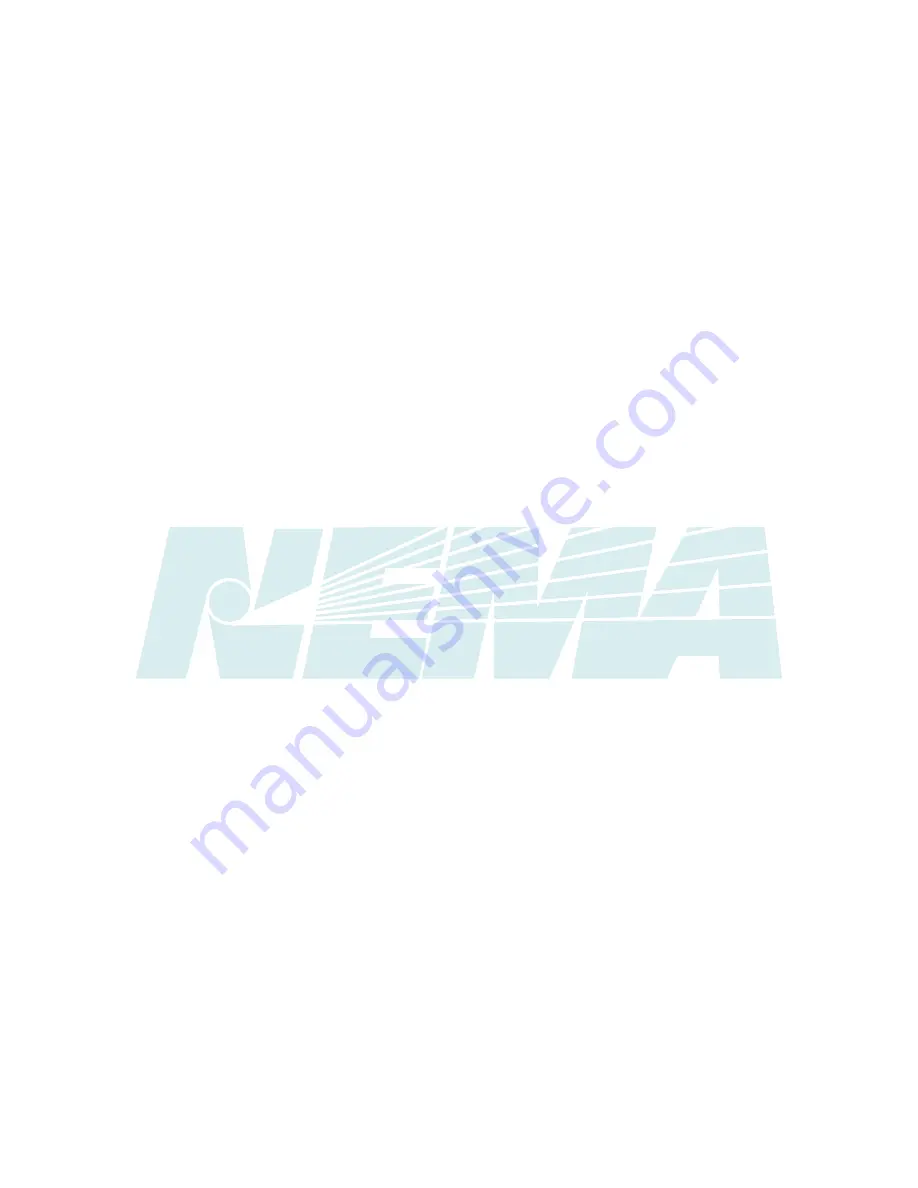
KS 3-2010
Page iii
Introduction
NEMA KS 3 deals with guidelines for inspection and preventive maintenance of switches used in
commercial and industrial applications. These guidelines are to be used to identify switches requiring
maintenance or replacement. Good practice includes periodic switch maintenance during plant shutdown
or during a regular maintenance period as specified, for example, in NFPA 70B. When a switch operates
automatically, good practice dictates that the source of the overcurrent should be located, and if it is
suspected that the operation was at or near the interrupting rating, the switch condition should be
checked prior to circuit re-energization.
When appropriately maintained, switches provide reliable protection for many years. The exact lifetime of
the switch, however, is determined by the switch’s operational duty and by its environment.
With respect to operational duty, for some circuits there will be occasional overload conditions or low-
current fault conditions. Here the operating life will be tens of years. In other circuits, there may be high
short-circuit-current faults but it should be noted that bolted faults at the switch interrupting rating are
rarely encountered. Short circuit events can significantly reduce the operating life of the switch and may
necessitate replacement of the switch. Switches in this Guideline are evaluated to three different UL
Standards: UL 98
Enclosed and Dead-Front Switches
, UL 977
Fused Power-Circuit Devices
, and UL
1429
Pullout Switches
. They are subjected to thousands of endurance test operations; overload test
operations; and two interrupting tests at maximum short-circuit-current rating. Thus switches have an
extensive but finite interrupting capability, and switches that experience multiple high short-circuit-current
faults should receive a thorough inspection and be replaced if necessary.
With respect to environmental effects, switches are sometimes exposed to high ambient temperatures,
high humidity, and other ambient conditions that are hostile to long term performance. For example,
industries may have corrosive environments or could be associated with dusty environments that could
affect operating parts.
It is not intended that switches be disassembled for inspection. Rather, NEMA KS 3 should be referenced
during periodic maintenance or during specific inspection following a high short-circuit-current fault. This
document is intended to ensure that switches are well maintained, and provides guidelines for switch
replacement.
This document is divided into separate sections as follows:
Section 1
presents the scope and referenced standards.
Section 2
details the safety procedures to be followed.
Section 3
deals with general guidance.
Section 4
deals with inspection procedures and describes thermal checks (4.2) and visual checks (4.3)
of the enclosure and switch condition. Overheating of the switch would necessitate further investigation,
and cracks in the insulation systems would certainly necessitate switch replacement.
Section 5
deals with preventive maintenance and ensures that the switch’s life is not compromised by
external conditions. The objectives are that the switch operates in a clean environment and that the
terminals are in good condition (5.2), that fuses (if required) are connected properly (5.3), and that wire
connectors are in good condition and are correctly torqued (5.4).
Section 6
deals with non-destructive test procedures that can be used to verify specific operating
characteristics of switches. These include the Mechanical Operation Test (6.2), the Insulation Resistance
Test (6.3), and the Individual Pole Resistance Test (millivolt drop test) (6.4). Non-compliance to one or
more of these tests could necessitate switch replacement.
© Copyright 2010 by the National Electrical Manufacturers Association.
Summary of Contents for Pow-R-Line SPX0361126
Page 2: ......
Page 4: ......
Page 6: ......
Page 7: ...TAB 1 Switchboards ...
Page 8: ......
Page 10: ......
Page 11: ...Instruction Data ...
Page 12: ......
Page 37: ...Component Data ...
Page 38: ......
Page 43: ......
Page 44: ......
Page 48: ......
Page 66: ...3 6 IM02601001E www eaton com Mechanical Installation ...
Page 114: ...14 IM02601001E www eaton com Using the I O Option Cards ...
Page 134: ...9 14 IM02601001E www eaton com Functions on the Web Server Pages Events Page ...
Page 156: ...10 22 IM02601001E www eaton com Setup on the Web Server Pages ...
Page 166: ...A 2 IM02601001E www eaton com Navigation Maps Main Menu Screens Sheet 1 ...
Page 167: ...www eaton com IM02601001E A 3 Navigation Maps Operating Mode Screens Sheet 2 ...
Page 168: ...A 4 IM02601001E www eaton com Navigation Maps Reset Mode Screens Sheet 3 ...
Page 169: ...www eaton com IM02601001E A 5 Navigation Maps Configuration Mode Screens Sheet ...
Page 170: ...A 6 IM02601001E www eaton com Navigation Maps ...
Page 172: ...B 2 IM02601001E www eaton com DIP Switch Description ...
Page 240: ...C 68 IM02601001E www eaton com Modbus Register Maps ...
Page 241: ......
Page 242: ......
Page 259: ...Shop Drawings ...
Page 260: ......
Page 262: ......
Page 264: ......
Page 266: ......
Page 268: ......
Page 270: ......
Page 272: ......
Page 274: ......
Page 275: ...Date PDF Generated 10 19 2012 Page 1 of 1 ...
Page 276: ......
Page 278: ......
Page 280: ......
Page 282: ......
Page 284: ......
Page 286: ......
Page 288: ......
Page 289: ...TAB 2 Panelboards ...
Page 290: ......
Page 292: ......
Page 293: ...Instruction Data ...
Page 294: ......
Page 296: ......
Page 325: ...Spare Parts ...
Page 326: ......
Page 371: ...Drawings ...
Page 372: ......
Page 374: ......
Page 376: ......
Page 378: ......
Page 380: ......
Page 382: ......
Page 384: ......
Page 386: ......
Page 387: ...TAB 3 Dry Type Transformers ...
Page 388: ......
Page 390: ......
Page 391: ...Instruction Data ...
Page 392: ......
Page 401: ...Drawings ...
Page 402: ......
Page 404: ......
Page 405: ...TAB 4 Molded Case Circuit Breakers ...
Page 406: ......
Page 408: ......
Page 409: ...Instruction Data ...
Page 410: ......
Page 417: ...TAB 5 Safety Switches ...
Page 418: ......
Page 420: ......
Page 421: ...Instruction Data ...
Page 422: ......
Page 424: ......
Page 452: ......
Page 453: ...Spare Parts ...
Page 454: ......
Page 467: ...Drawings ...
Page 468: ......
Page 470: ......
Page 471: ...Item 001 Cat DH261FGK ...
Page 472: ......
Page 474: ......
Page 475: ...Item 002 Cat DH261FGK ...
Page 476: ......
Page 478: ......
Page 479: ...Item 003 Cat DH261FGK ...
Page 480: ......
Page 482: ......
Page 483: ...Item 004 Cat DH261FGK ...
Page 484: ......
Page 486: ......
Page 487: ...Item 09 Cat DH364NRK ...
Page 488: ......
Page 490: ......
Page 491: ...Item 011 Cat DH324NGK ...
Page 492: ......
Page 494: ......
Page 495: ...Item 013 Cat DH362FRK ...
Page 496: ......
Page 498: ......
Page 499: ...Item 015 Cat DH321NRK ...
Page 500: ......
Page 502: ......
Page 503: ...Item 017 Cat DH362FRK ...
Page 504: ......
Page 506: ......
Page 507: ...Itm 019 Cat DH221NGK ...
Page 508: ......
Page 510: ......
Page 511: ...Item 021 Cat DH361UGK ...
Page 512: ......
Page 513: ...TAB 6 Enclosed Control NEMA ...
Page 514: ......
Page 516: ......
Page 517: ...Instruction Data ...
Page 518: ......
Page 550: ......
Page 551: ......
Page 552: ......
Page 561: ......
Page 562: ......
Page 578: ......
Page 579: ...Drawings ...
Page 580: ......
Page 582: ......
Page 584: ......