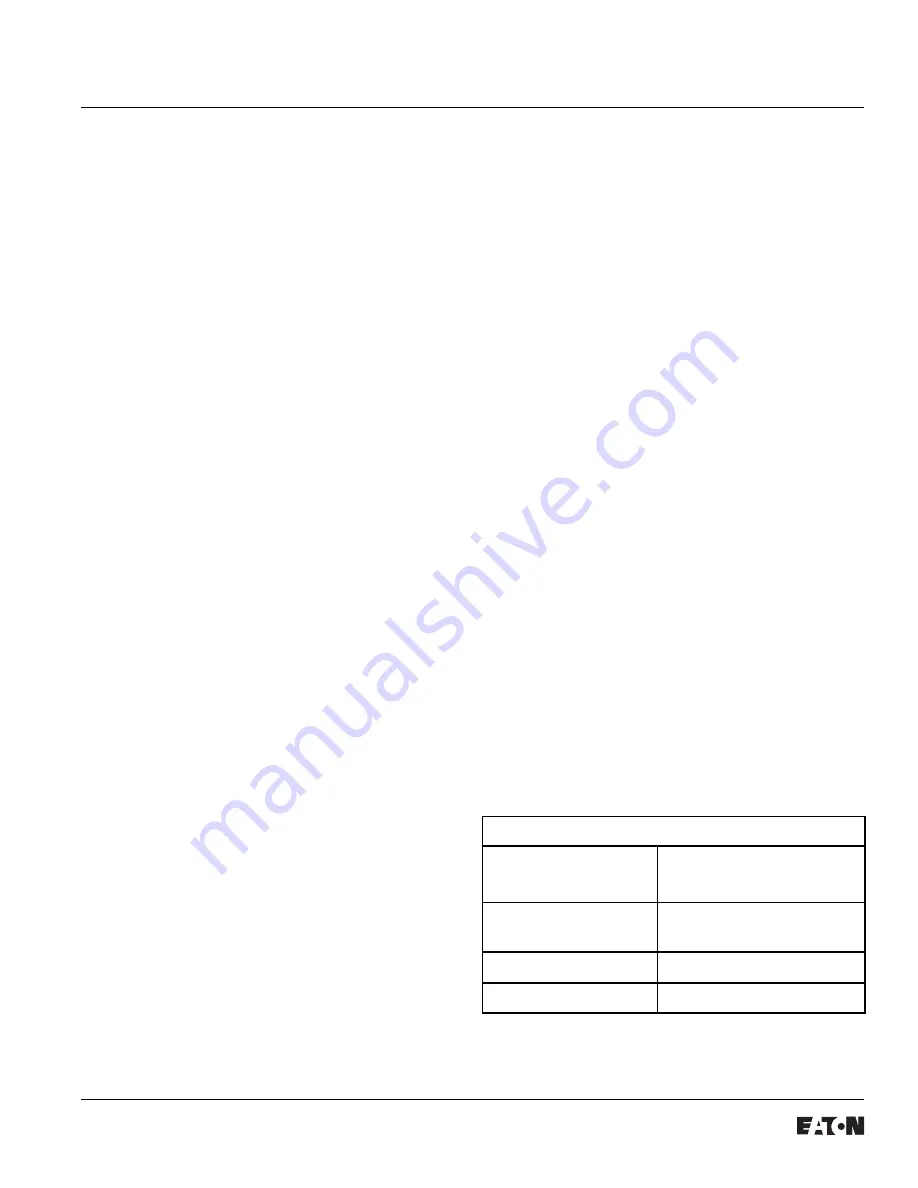
I.B. 48003
Page 19
Effective 11/97
If for some reason a coil must be changed, proceed as
follows:
1.
Deenergize all circuits.
2.
Loosen the set screw holding the kickout spring
adjusting screw. See Figure 6.
Loosen the kickout spring adjusting screw until the
kickout spring can be removed easily.
NOTE: Whenever adjusting the kickout spring lever,
put a free hand over the kickout spring as a precau-
tion.
3.
Remove leads to coil terminals, noting their position
for later reconnection.
4.
Remove the two 0.313-inch magnet mounting bolts.
Remove the bolts completely and set aside until later.
5.
Lift magnet and coil upward and out.
6.
Remove the coil clip from old coil and install on the
new coil. Note that the coil clip is THREADED.
Remove the coil lock nut before removing the screw.
When installing the clip on the new coil, tighten the
screw only to snug. Then lock the screw into the coil
clip with the lock nut. Note that the head of the screw
must be toward the armature.
7.
Re-install the magnet into the coil, and lower both
into position. Do not force. Sometimes it is neces-
sary to jiggle the coil slightly into its sealed position.
8.
Install the two magnet mounting bolts, but do not
tighten.
9.
Re-connect the coil circuit.
10. After checking for safe operation, energize the coil
and close the contactor. While the magnet is sealed,
tighten the two magnet mounting bolts, using continu-
ing care against shock. Then de-energize the coil.
11. Re-install the kickout spring, making sure to put the
two ends of the spring wire downward, so that the
spring will take a natural bow. Tighten the adjusting
screw until the kickout spring lever is approximately
vertical, and the armature is solidly against its stop
on the molded frame. See Figure 12. When a
screwdriver is pushed against the bottom end of the
armature in the open position, the armature must not
move. If it does, the kickout spring should be tight-
ened further to push the armature to a solid position.
Tighten the set screw to lock the kickout spring
adjusting screw.
If the magnet chatters, look for mechanical interference
that prevents the magnet from sealing. If there is no
interference, then the magnet itself may be misaligned.
The magnet gap can be seen from the left and the right
sides with the help of a flashlight. The stationary magnet
can be aligned with a 0.50-inch (12.7mm) diameter steel
rod inserted into the two holes in the core of the magnet
and used as a lever to put a corrective set into the
magnet frame. it should not be necessary to do this
unless the contactor has been damaged and it can be
seen that the armature does not fit against the magnet.
A poor magnet-to-armature fit usually produces a high
dropout voltage and/or chatter.
Mechanical interference can be produced by various
incorrect adjustments. Two specific points to check are:
A. Armature travel incorrect, causing the contact springs
to be compressed into a solid, non-resilient “tube”
that stops the crossbar rigidly. Call Cutler-Hammer
Service for assistance.
B. The auxiliary contact assemblies operating arms are
misadjusted, so that a contact plunger bottoms
solidly before the magnet seals. When the contactor
is fully sealed closed, there should still be a small
amount of travel remaining for these plungers. Adjust
as described below.
Contactor Auxiliary Contacts
Two Type L64 auxiliary contact assemblies are mounted
on the contactor front (right side) to provide four isolated
auxiliary, 600 VAC, 10 ampere, double-break contacts for
use in control circuits. Any combination of normally-open
or normally-closed circuits is available by selection of the
appropriate assembly from Table IV.
The normally-open (NO) L64 auxiliary contacts close just
after the main contacts of the contactor close. The
normally-closed (NC) L64 auxiliary contacts open just
before the main contacts close.
In addition, a single-circuit Type L63 auxiliary contact
(normally-closed) is mounted on the front (left side) and
is connected to coil terminals C and D. This auxiliary
contact (578D461G03) is equipped with permanent
magnet blowouts on the contacts.
TABLE IV. TYPE L64 AUXILIARY CONTACTS
Circuit Combination Provided
Part Number
By One Auxiliary Contact
Assembly
843D943G21
One Normally-Open and
One Normally-Closed
843D943G22
Two Normally-Open
843D943G23
Two Normally-Closed