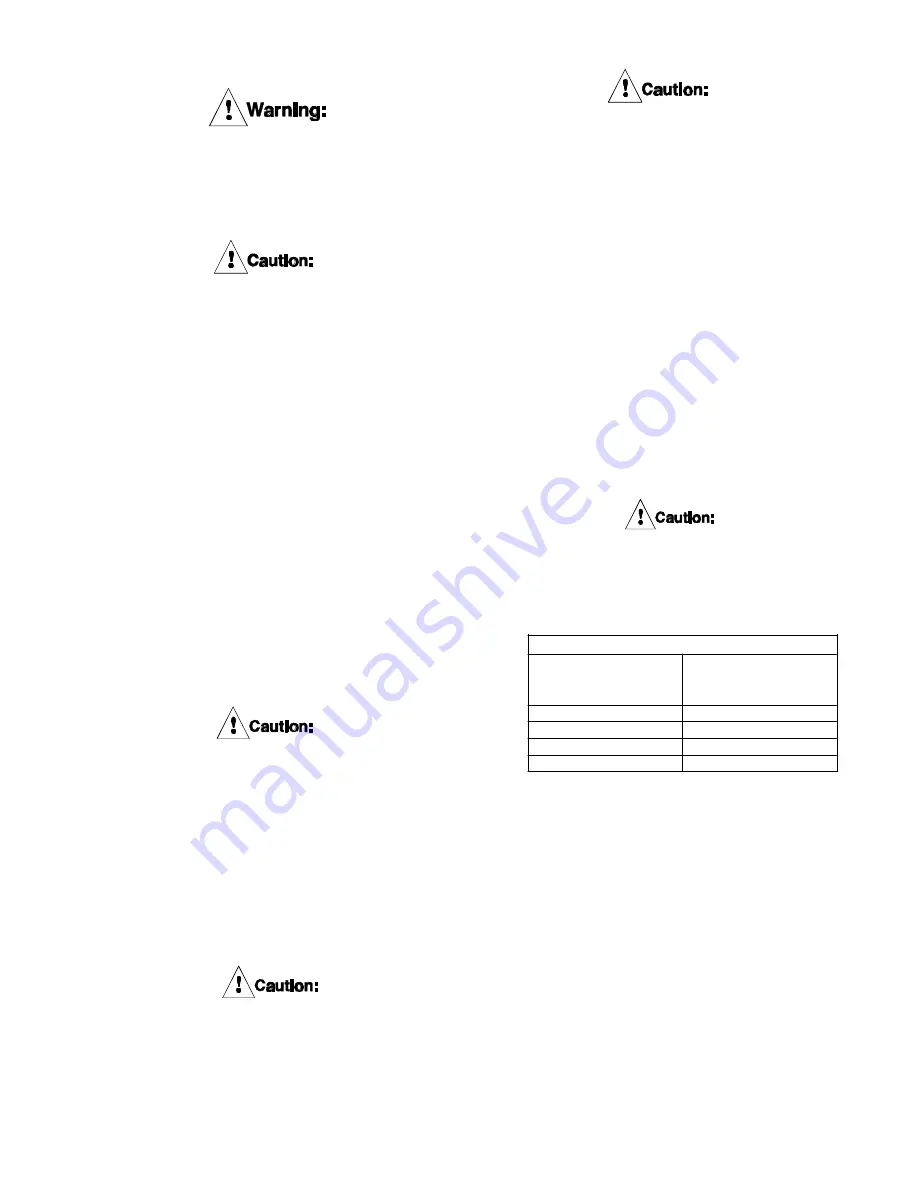
Do not use compressed air to blow
dust accumulations out from be-
tween the friction shoes. Although
the friction material does not contain
asbestos, the dust created as the fric-
tion material wears, along with the
dust from the operating environment,
may irritate the respiratory system.
4.1.2
Partial or complete disassembly is required to
inspect the following items:
4.1.2.1
Drum Diameter Wear
- Check the O.D. of the
drum and compare to the values shown on
Table 4. Minor heat-checking may be re-
moved by machining the drum O.D. If the
drum has been subjected to excessive heat,
the open end may flare out, giving the impres-
sion that the drum has not worn. It is therefore
important to check the diameter at several lo-
cations across the face.
Operation of the clutch or brake on
a drum that has worn, or has been
machined, to less that minimum al-
lowable diameter will result in dam-
age to the element components.
*Note: The number preceding the letters “CB”
in the element size designates the original
drum diameter in inches.
Example: For 10CB300 - Original Drum
Diameter = 10.00 inches (254mm)
Minimum allowable drum diameter is:
10.00 - .09 = 9.91 (254 - 2 = 252mm).
4.1.2.2
Air Actuating Tube
- Check that the rubber
tube has not been damaged by excessive
heat. If any portion of the tube is hard or
charred, the entire element must be replaced.
Check for any blisters, which would indicate
ply separtion. A tube in this condition also re-
quires replacement of the entire element.
4.0
MAINTENANCE
Only qualified personnel should
maintain and repair these units.
Faulty workmanship may result in
personal injury or equipment dam-
age.
When replacing components, use
only genuine Airflex replacement
parts. Use of other materials may
severely effect performance.
4.1
Periodic Inspection
4.1.1
The following items may be inspected without
disassembly of the element:
4.1.1.1
Air Control Components
- Check for proper
adjustment of the air control components.
Make sure the safety pressure switches, if
used, are set correctly. Repair any air leaks.
4.1.1.2
Friction Shoe Assembly Lining Wear
-
If the linings have worn to the minimum allow-
able thickness of 1/16" (1.5mm), they must be
replaced as a complete set, with the excep-
tion of element size 4CB200, where replace-
ment of the entire element is required when
worn to
the minimum lining thichness of 1/32"
(0.8mm).
Operation with friction material worn
to less than minimum allowable thick-
ness will result in damage to the
drum.
4.1.1.3
Contamination of Shoes or Drum
- Oil
or grease contamination will reduct the
developed torque of the clutch or brake.
Disassembly will be required to clean any oil
or grease build-up. Any dust accumulation
may be vacuumed from between the friction
shoe assemblies.
Do not attempt to use a solvent to
remove oil or grease without first
removing the element. While squirt-
inga solvent into an installed clutch
TABLE 4 - DRUM WEAR LIMITS
Element
Size
Maximum Allowable
Wear on Drum
Diameter *, in. (mm)
4CB200 thru 14CB400
.09 (2)
16CB500 thru 24CB500
.12 (3)
26CB525 thru 40CB525
.19 (5)
45CB525
.25 (6)
PDF Format
9
© Copyright Eaton Corp., 2001. All rights reserved.