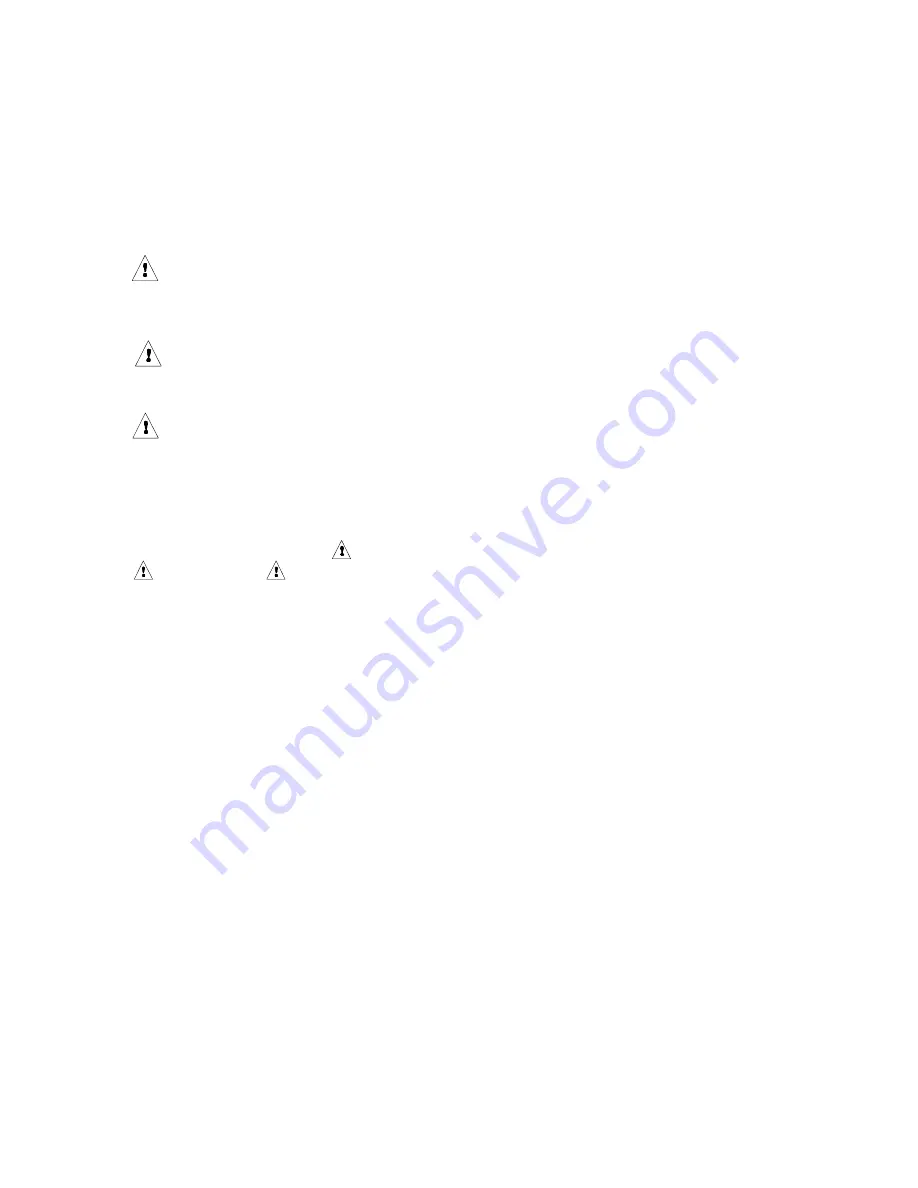
1.0
INTRODUCTION
Throughout this manual there are a number
of
HAZARD WARNINGS
that must be read
and adhered to in order to prevent possible
personal injury and/or damage to equipment.
Three signal words
“DANGER”
,
“WARNING”
,
and
“CAUTION”
are used to indicate the se-
verity of a hazard, and are preceded by the
safety alert symbol
DANGER
- Denotes the most serious
hazard, and is used when serious injury or
death
WILL
result from misuse or failure to
follow specific instructions.
WARNING
- Used when serious injury
or death
MAY
result from misuse or failure to
follow specific instructions.
CAUTION
- Used when injury or
product/equipment damage may result from
misuse or failure to follow specific instructions.
It is the responsibility and duty of all personnel
involved in the installation, operation and main-
tenance of the equipment on which this device
is used to fully understand the DANGER,
WARNING, and CAUTION proce-
dures by which hazards are to be avoided.
1.1
Description
1.1.2
The Airflex® air-actuated CB element assem-
bly is designed and manufactured to provide
dependable clutch or brake service in a multi-
tude of industrial applications. It is suited to
high speed, cyclic operations, as well as for
coupling and general power transmission. All
torque load is carried through the neoprene
and cord actuating tube which absorbs damag-
ing shock loads. The Airflex CB element as-
sembly requires no lubrication or adjustment.
1.1.3
Airflex element assemblies are available for
drum diameters from four inches through 45
inches. The element size designation indi-
cates the nominal outside drum diameter in
inches, the clutch model, and the width of the
friction material. For example, size “12CB350"
indicates the element operates on a drum hav-
ing a nominal diameter of 12 inches, is an Air-
flex ”CB" series clutch or brake (the scope of
this manual) and has friction material which is
three and one-half inches wide.
1.1.4
Where diametral space is limited, or the
torque required is greater than a single ele-
ment can transmit, CB elements size
12CB350 and larger can be supplied as dual
units.
1.2
How It Works
1.2.1
Referring to Figure 1, CB construction con-
sists of a neoprene and cord actuating tube
which is bonded to the outer steel rim. The rim
is drilled for mounting to the driving compo-
nent (or reaction bracket in the case of a CB
brake application). Friction shoe assemblies
(FSA’s) are attached to the inside diameter of
the tube with shoe pins which are then re-
tained with lockwires.
1.2.2
As air pressure is applied to the air actuating
tube, the tube inflates, forcing the friction shoe
assemblies uniformly against the drum which
is attached to the driven component. In the
case where the CB element is being used as a
clutch and is attached to the driving shaft,
through the element mounting component
(typically an iron spider), through the rim/tube
structure to the friction shoe assemblies,
where the torque is trnasmitted through the
friction couple to the components mounted on
the driven shaft (clutch drum and drum mount-
ing component). As actuating air is exhausted,
the resiliency of the tube, aided by centrifugal
force when used as a clutch, retracts the
shoes, resulting in total disengagement.
1.3
Element Adjustment
1.3.1
Airflex CB elements are completely self adjust-
ing and automatically compensate for lining
and drum wear. Lubrication is not required.
The torque developed is dependent upon rotat-
ing speed and applied air pressure. By limiting
the applied pressure, the element will act as a
torque limiting device and provide overload
protection.
1.3.2
To accomplish regulated or cushioned engage-
ment of the element, a flow control valve may
be installed in the element air supply line and
adjusted to restrict air flow to the element
while allowing free flow away from the element
for rapid disengagement. By adjusting the
flow, the rate of engagement may be varied.
Note that the flow control valve does not regu-
late air pressure - the supply pressure must al-
ways be adequate to transmit the maximum
required torque. Refer to the OPERATION sec-
tion of this manual for air piping configurations.
PDF Format
2
© Copyright Eaton Corp., 2001. All rights reserved.