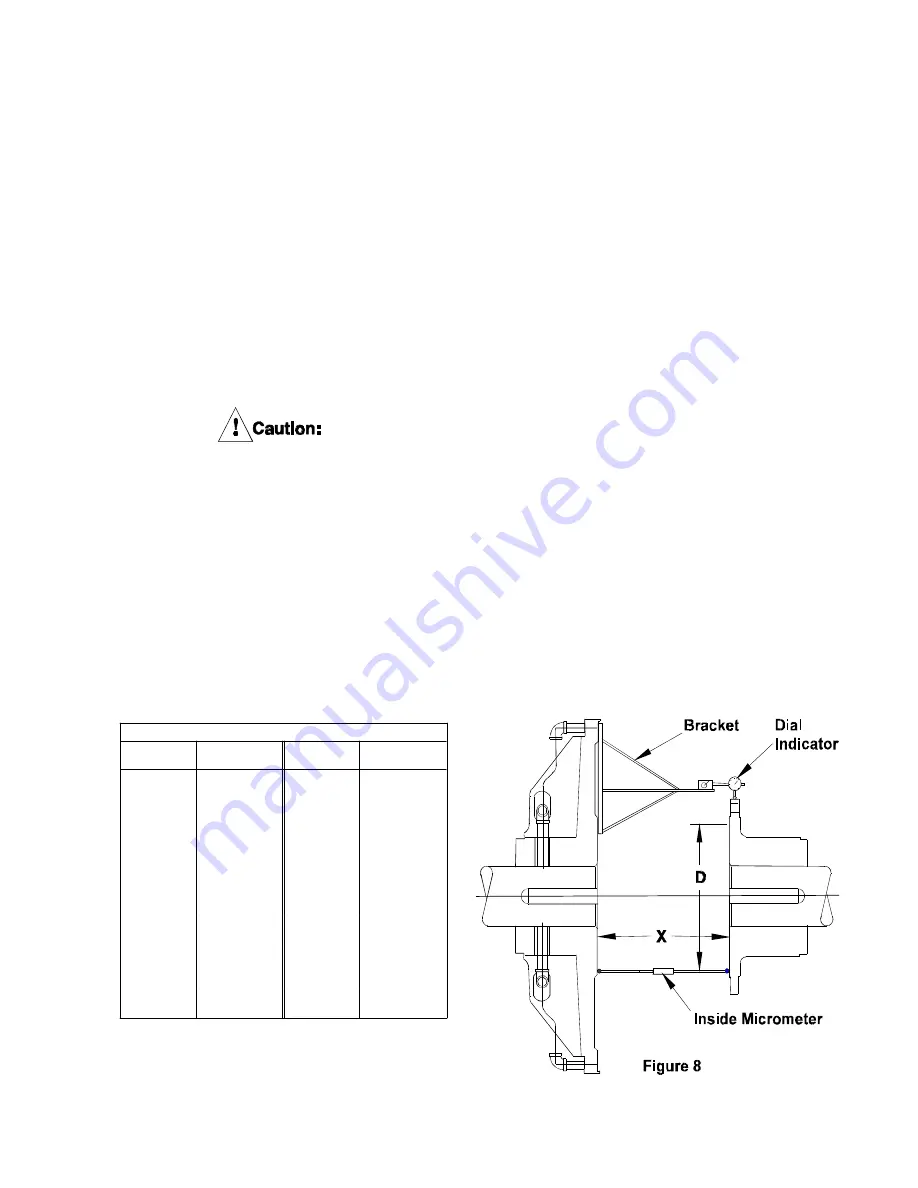
TABLE 2 - “X” DIMENSIONS (FIG. 8)
SINGLE
ELEMENTS
“X” in.
(mm)
DUAL
ELEMENTS
“X” in.
(mm)
6CB200
3.250 (82.6)
——
——
8CB250
3.750 (95.3)
——
——
10CB300
4.375 (111.2)
——
——
12CB350
5.000 (127.0)
12CB350
10.500(266.7)
14CB400
5.500 (139.7)
14CB400
11.500(292.1)
16CB500
7.062 (179.4)
16CB500
14.000(355.6)
18CB500
7.062 (179.4)
18CB500
14.000(355.6)
20CB500
7.062 (179.4)
20CB500
14.000(355.6)
22CB500
7.062 (179.4)
22CB500
14.000(355.6)
24CB500
7.062 (179.4)
24CB500
14.000(355.6)
26CB525
7.500 (190.5)
26CB525
14.625(371.5)
28CB525
7.500 (190.5)
28CB525
14.750(374.7)
30CB525
7.500 (190.5)
30CB525
14.750(347.7)
32CB525
7.500 (190.5)
32CB525
14.750(347.7)
36CB525
7.500 (190.5)
36CB525
14.750(347.7)
40CB525
7.500 (190.5)
40CB525
14.750(347.7)
45CB525
7.500 (190.5)
45CB525
14.750(347.7)
2.3
Mounting Spider and Drum Hub
2.3.1
The spider and drum hub are bored for a
press fit onto their respective shafts. The inter-
ference is approximately .0005 in, per inch
(.0005mm/mm) of shaft diameter,
2.3.1.1 Ensure the shaft is clean and free of nicks or
burrs and check the shaft and bore diameters
for proper fit.
2.3.1.2 Tap the key into the keyway, making sure it
bottoms.
2.3.1.3 Apply a light coat of anti-seizing compound to
the shaft and key.
2.3.1.4 Heat the drum hub or spider uniformly to
250º F (121ºC) to expand the bore.
It is recommended the drum hub or
spider be heated in oil or an oven;
however, since this is not always
possible, torches may be used. When
using torches, use several with “rose-
bud” (broad-flame) tips and keep
them moving to avoid “hot spots”.
Check bore temperature frequently to
avoid overheating.
2.3.1.5 Slide the heated drum hub or spider onto the
shaft until the hub face is flush with the end of
the shaft. Hold in position and allow to cool.
2.4
Shaft Alignment
Note: The text in this section applies to gap-
mounted applications; however, the alignment
tolerances apply to all types of mountings.
Parallel Alignment Tolerance (Off-
set
):
Not to exceed 0.010 inch (.254mm) Total In-
dicator Reading (0.005 in. (.127mm)maxi-
mum offset).
Angular Alignment Tolerance (Gap):
Not to be exceed 0.0005 inch per inch
(.0005mm/mm) diameter at which readings
are taken (“D” on FIg. 8).
Note: The alignment procedure described be-
low has been used successfully on many CB
clutch and brake applications. Other proce-
dures, of course, may be used;
however, the alignment tolerances are the
same regardless of the technique used.
2.4.1
Foundations must be set so distance “X”,
shown in Figure 8, is established. If the clutch
is mounted on a shaft having plain bearings,
make sure the shaft is centered within the
bearings when establishing the “X” dimension.
Refer to Table 2 for appropriate “X” dimen-
sions.
Note: It is presumed that one of the shafts has
been properly located and anchored.
PDF Format
6
© Copyright Eaton Corp., 2001. All rights reserved.