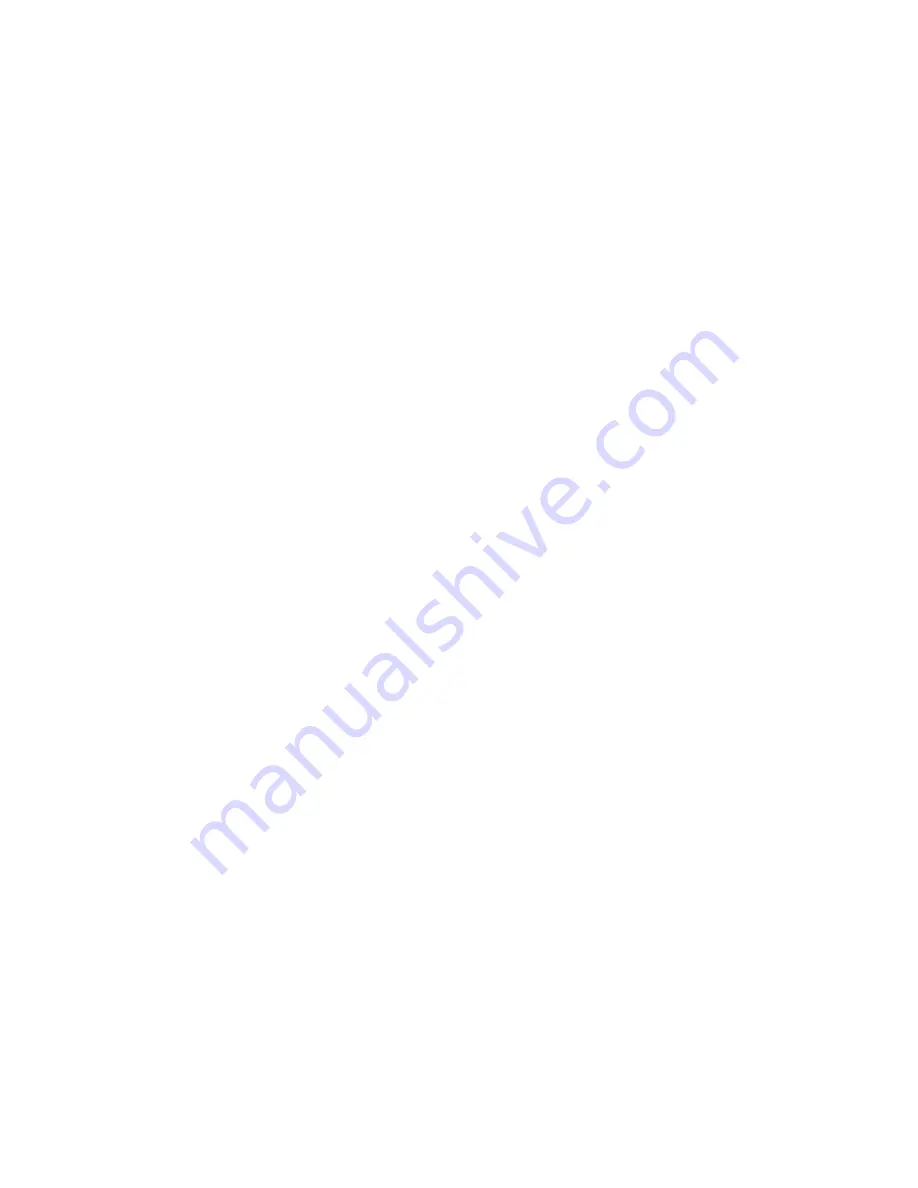
To order parts and supplies: 800.345.1178 >> eastwood.com
13
ShEET METAL wELDING TEchNIquES
When welding sheet metal a different approach is usually taken to account for how thin the metal is and it’s susceptible to
warping it is. The technique most often used is called Stitch Welding and this process is described below:
1.
Clean the metal to be welded of any paint, rust, oil, grease, dirt or any other contaminants that may be on the surface of the piece.
2.
Secure the pieces to be welded in place using clamps. Be sure to leave a small gap between the two pieces of sheet
metal for the weld to flow into, this will result in a lower bead height which will require minimal finishing.
3.
Consult the Suggested Settings Chart and set the Voltage and Wire Speed knobs appropriately.
4.
Get some pieces of scrap metal of the same thickness and verify that the settings will work for the specific weld you
will be making.
5.
Once the settings have been fine tuned tack weld your final pieces in places and remove the clamps if they are in the
way of the weld.
6.
The Stitch Welding technique can now be utilized which is basically a series of tacks connecting together. To perform
the technique, trigger the gun to form a tack weld and then continue to trigger on and off the gun making a series of
connected tack welds following along the path of the weld joint. Continue the series of tacks for an inch or so and then
move to a different section of the weld and perform the process there. It is essential to keep moving around to spread
out the heat making sure not to get one section too hot and warp the metal.
7.
Once the entire weld has been completed allow the metal to cool. If necessary follow up with a flap disc to grind the
weld bead flush.
hEAvY GAuGE METAL wELDING TEchNIquES
When welding sheet metal, a different approach is usually taken to account for how thin the metal is and it’s susceptible
to warping it is. The technique most often used is called Stitch Welding and this process is described below:
1.
Clean the metal to be welded of any paint, rust, oil, grease, dirt or any other contaminants that may be on the surface
of the piece.
2.
Secure the pieces to be welded in place using clamps. Be sure to leave a small gap between the two pieces of metal
for the weld to flow into, this will result in a lower bead height which will require minimal finishing.
3.
Consult the Suggested Settings Chart and set the Voltage and Wire Speed knobs appropriately.
4.
Get some pieces of scrap metal of the same thickness and verify that the settings will work for the specific weld you will be making.
5.
Once the settings have been fine-tuned tack weld your final pieces in places and remove the clamps if they are in the
way of the weld.
6.
When welding heavy gauge metal there are two basic approaches to creating the weld. The first is a continuous bead
with steady gun movement along the length of the joint. The second type of weld is a Stringer or Weave bead. This is
accomplished by moving the torch in a circular or zig zag pattern. Either of these techniques will create strong welds
but in some cases the Stringer or Weave type will create a more aesthetically appeasing weld bead.
7.
Once the entire weld has been completed, allow the metal to cool. If necessary, follow up with a flap disc to grind the
weld bead flush.
OvERLOAD PROTEcTION
Your Eastwood MIG175 is equipped with a temperature controller as well as an overload breaker. These two protection devices will
protect your welder if the duty cycle is exceeded. If the output is exceeded, the internal breaker will trip and stop power supply to the
drive motor although the fan will still run to cool the unit.
If the breaker tripped resulting from an overload, the circuit breaker button on the rear of the welder will extend out. This circuit
breaker must be reset manually. Before resetting the circuit breaker button allow the welder to cool for a minimum of 15 minutes.
If there is no voltage output and the circuit breaker was not tripped, the internal thermal protector may have shut off the welder until
it cools to normal operating temperature. This is an automatic function and does not require the user to manually reset anything.