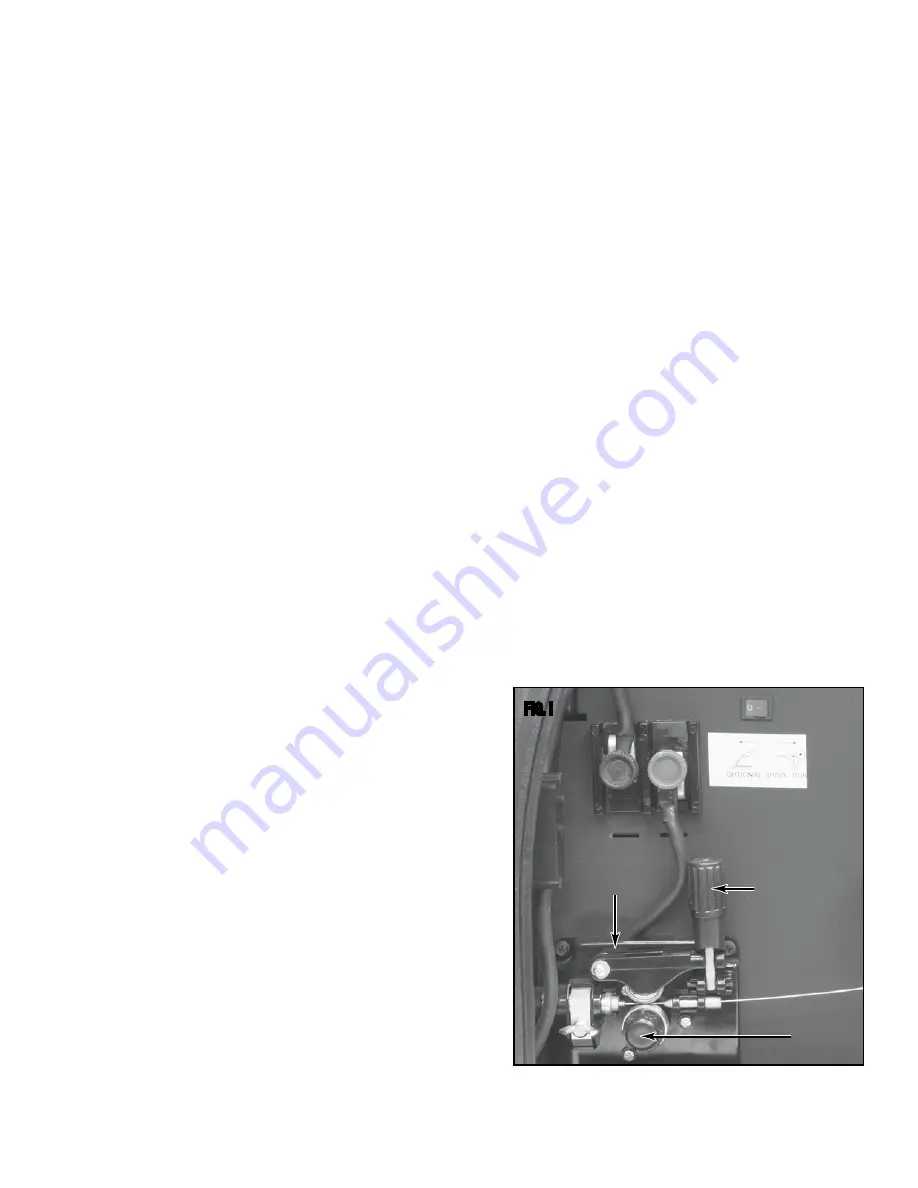
To order parts and supplies: 800.345.1178 >> eastwood.com
9
ShIELDING GAS FLOw ADjuSTMENT
After connecting your Shielding Gas Regulator, the gas flow rate needs to be adjusted so that the proper amount of Shielding Gas
is flowing over your weld. If there is too little gas flow there will be porosity in your welds as well as excessive spatter, if there is
too much gas flow you will be wasting gas and may affect the weld quality. The included regulator has 2 gauges on it; the gauge
on the left is your flow rate while the gauge on your right is your tank pressure.
1.
Open your Shielding Gas tank valve all the way.
2.
Adjust the knob on the regulator to ~30 CFH.
3.
Turn on the welder and trigger the torch switch which will start the gas flow.
4.
As you trigger the torch switch you will notice that as the gas flow starts the needle on the gauge drops to a steady reading.
The reading while flowing is the value you want to read.
5.
The gas flow should be set to ~20CFH while flowing. The CFH (Cubic Feet per Hour) scale is the inside scale in red on your
flow gauge. 20CFH is the most typical flow rate but it may need to be adjusted in some cases depending if there is a slight
breeze or some other instance where additional shielding gas is required to prevent porosity in the weld.
6.
When finished welding remember to close the gas valve on the bottle.
chANGING ThE DRIvER ROLLER
The wire feed drive roller on the drive motor has 2 grooves, one for 0.023” (0.6mm) welding wire and another for 0.030” (0.8mm)
or 0.035” (0.9mm) welding wire. Your MIG175 comes with the drive roller pre installed for using 0.030” (0.8mm) wire. In the event
that 0.023” welding wire is to be used, the wire feed roller needs to be changed.
1.
Turn off the welder and unplug the welder from power.
2.
Unlock the Tensioner (Fig. 1I) by pulling it towards you.
3.
Lift the Rocker Arm (Fig. 2I) up and rotate out of the way.
4.
Remove the star knob (Fig. 3I) by loosening it by hand.
5.
Slide the drive roller off the shaft.
6.
Determine which size wire is going to be used and slide the
drive roller back onto the shaft by aligning the key on the shaft
with the keyway on the roller.
NOTE:
The stamped marking on the side of the drive roller indicates
the size of the groove on the opposite side of the roller. The groove
closest to the drive motor is the groove that will be used. If setting up
to use 0.023” (0.6mm) wire, the ‘0.6’ stamping should be facing the
user when installing it.
7.
Tighten the star knob finger tight.
8.
Push the rocker arm back down into place.
9.
Lift up on the Tensioner to put back in place and adjust as
necessary.
FIG. I
1.
1⁄4 turn and test again.
2.
You do not want too much tension on the tension roller as it will tend to deform the wire. Just enough to feed
the wire without slipping
3.
Once the wire has emerged from the tip of the gun, turn the machine OFF and replace the tip and nozzle.
✓
1I
✓
2I
✓
3I