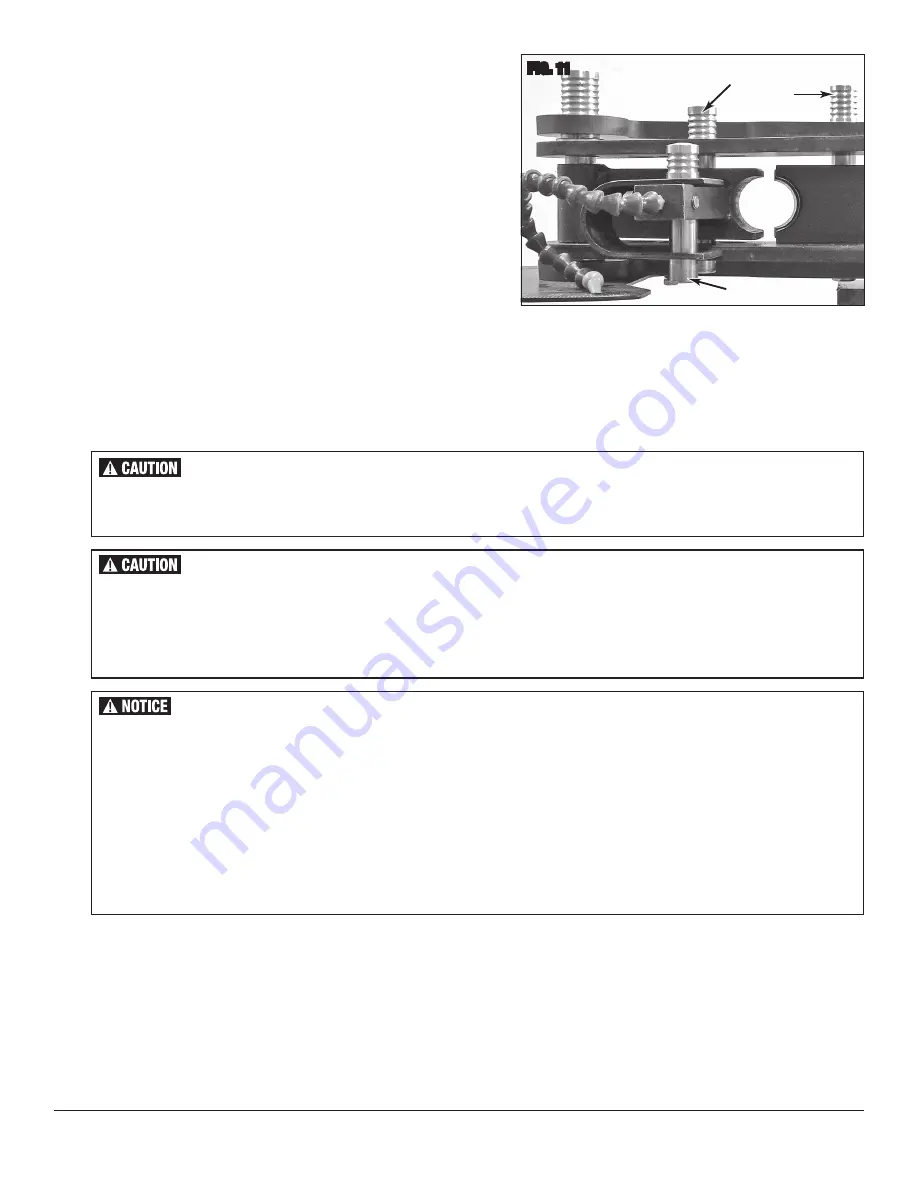
8
Eastwood Technical Assistance: 800.343.9353 >> [email protected]
ATTACHING DEGREE POINTER
• After mounting a selected Die set (not included), thread the base of the Degree
Pointer
[G]
into the M9 thread on the end of the rectangular bar Offset Arm
feature of the Die
(FIG 11)
.
NOTE:
The Degree Pointer must be removed and re-installed with each Die size
change.
INSTALLATION AND LOCATION
• The Bender
MUST
be located on a solid and level surface for proper operation
and safety.
• The Bender
MUST
be located in a clean, dry, well-lighted environment free of
dust, grit, or other contaminates.
• Consideration
MUST
be given to the movement of the free end of tubing being
bent and the amount of open space surrounding the Bender. Ensure surrounding
area is clear of people and obstacles.
OPERATION
FIG. 11
PINCH HAZARD!
The Eastwood Hydraulic Tubing Bender exerts tremendous bending and crushing forces in operation which can present a hand/fin-
ger pinch hazard and cause potentially serious injuries in a matter of seconds. Avoid moving parts while operating and wear thick,
well-fitting work gloves to prevent cuts from handling sharp metal. The use of safety shoes is strongly recommended.
INJURY HAZARD!
If any breakage or damage to the Bender occurs, DO NOT USE until proper repairs are made.
The Eastwood Hydraulic Tubing Bender was specifically designed to be operated by one person only. Never have one person operate
the lever while one handles the material workpiece or serious injury could occur.
Injury or property damage could occur from being struck by moving workpiece material. Before beginning work, be sure the
surrounding work area is clear of obstructions or persons to accommodate the swing of long sections of workpiece material.
The Eastwood Hydraulic Tubing Bender, as with many advanced metal working tools, requires a learning curve to become proficient
in its use. Plan on using a generous amount of practice material in order to achieve a “feel” for the tool and learn what results to
expect before attempting a finished piece.
In addition, it is strongly suggested that a set of “templates” be made of each size, material, thickness and degree of bend for every
type of tubing you plan to use in a planned project. This will save a great deal of time and material waste when planning future
projects.
Workpiece material must be clean of any rust, burrs, nicks, welds or coatings before attempting to bend or interference and binding
will occur.
Apply only a minimal amount of lubricant to material and die surfaces to prevent the tubing from binding during the bending
process. DO NOT over lubricate.
✓
L
✓
K
✓
H or J