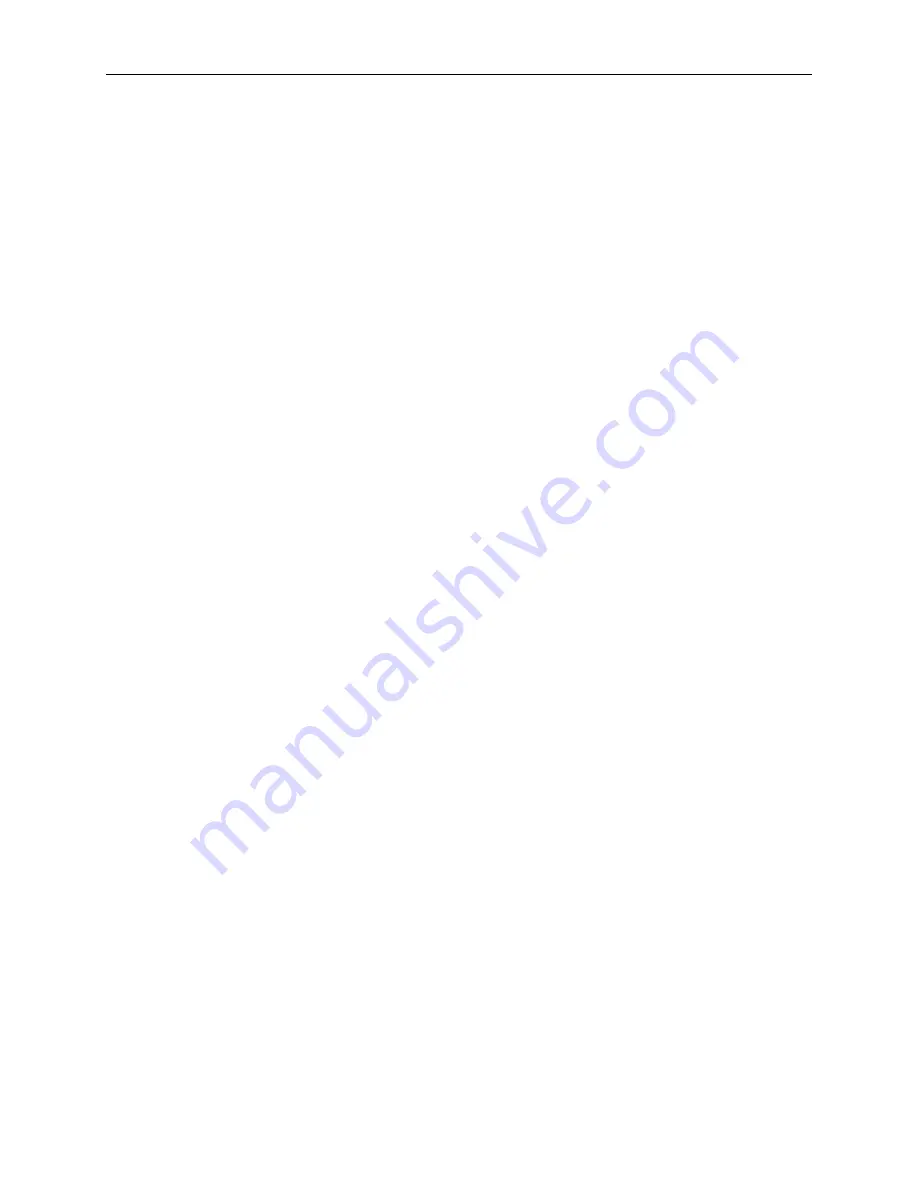
20 Operation
Special Notes About the Bundling Tunnel Shutdown Sequence
When shutting down the tunnel, be sure to first turn the heater-bank switch to Off.
Once the heater-bank switch is switched off, it will take some time (this will vary
depending on heat settings) for the tunnel to cool down completely.
When the tunnel cools down to approximately 150°F or 66°C (unless a different cool-
down temperature has been set), the tunnel conveyor and blowers will shut off
automatically.
Bringing the tunnel down this way helps prevent damage to the conveyor and
internal components from excess prolonged exposure to heat inside the tunnel.
When the tunnel is in the resulting standby state, it shuts off the power to the
conveyor and heating elements but the lights and controller use only minimal power
in a standby state. This allows the tunnel to be readily brought up for the next
production run once the heater banks are switched on and the rest of the normal
daily sequence of operation is followed.
It is not necessary to shut the main power lever off and then move it back to the On
position to “reset” or “reboot” the system after each production run, and this can
actually result in undue, premature wear of the main power switch.