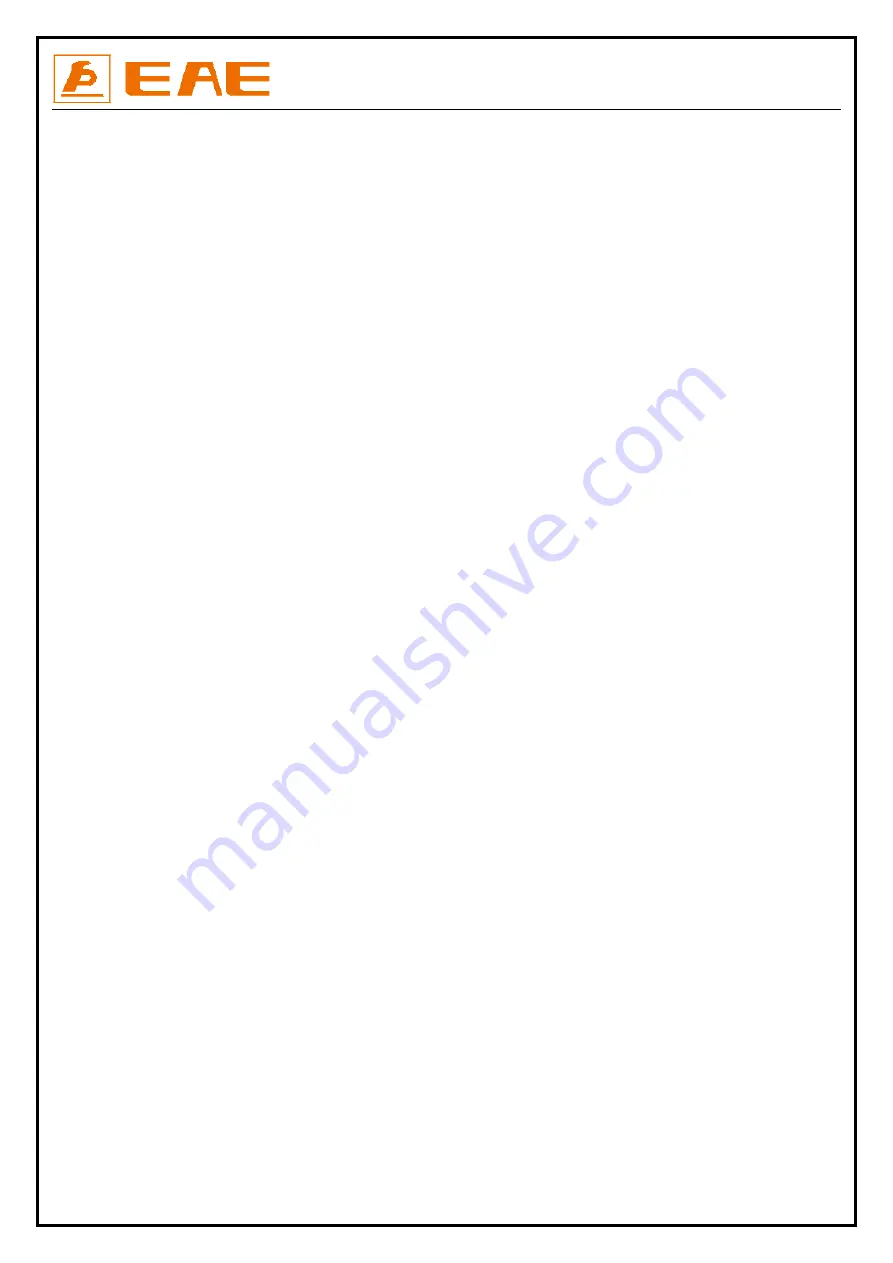
Installation, Operation and Parts Manual
EE-6445P
4
to
be
able
to
check
and
give
an
expert
option
on
lifting
platforms.
1.3
Important
safety
notices
1.3.1
Recommend
for
indoor
use
only.
DO
not
expose
the
lift
to
rain,
snow
or
excessive
moisture.
1.3.2
Only
use
this
lift
on
a
surface
that
is
stable,
level
and
dry
and
not
slippery,
and
capable
of
sustaining
the
load.
Do
not
install
the
lift
on
any
asphalt
surface.
1.3.3
Read
and
understand
all
safety
warnings
before
operating
the
lift.
1.3.4
Do
not
leave
the
controls
while
the
lift
is
still
in
motion.
1.3.5
Keep
hands
and
feet
away
from
any
moving
parts.
Keep
feet
clear
of
the
lift
when
lowering.
1.3.6
Only
these
properly
trained
personnel
can
operate
the
lift.
1.3.7
Do
not
wear
unfit
clothes
such
as
large
clothes
with
flounces,
tires,
etc.,
which
could
be
caught
by
moving
parts
of
the
lift.
1.3.8
To
prevent
evitable
incidents,
surrounding
areas
of
the
lift
must
be
tidy
and
with
nothing
unconcerned.
1.3.9
The
lift
is
simply
designed
to
lift
the
entire
body
of
vehicles,
with
its
maximum
weight
within
the
lifting
capacity.
1.3.10
Always
insure
the
safety
locks
are
engaged
before
any
attempt
to
work
near
or
under
the
vehicle.
Never
remove
safety
related
components
from
the
lift.
Do
not
use
if
safety
related
components
are
damaged
or
missing.
1.3.11
Do
not
rock
the
vehicle
while
on
the
lift
or
remove
any
heavy
component
from
vehicle
that
may
cause
excessive
weight
shift.
1.3.12
Check
at
any
time
the
parts
of
the
lift
to
ensure
the
agility
of
moving
parts
and
the
performance
of
synchronization.
Ensure
regular
maintenance
and
if
anything
abnormal
occurs,
stop
using
the
lift
immediately
and
contact
our
dealers
for
help.
1.3.13
Lower
the
lift
to
its
lowest
position
and
do
remember
to
cut
off
the
power
when
not
using
the
lift.
1.3.14
Do
not
modify
any
parts
of
the
lift
without
manufacturer’s
advice.
1.3.15
If
the
lift
is
going
to
be
left
unused
for
a
long
time,
users
are
required
to:
a.
Disconnect
the
power;
b.
Empty
the
oil
tank;
c.
Lubricate
the
moving
parts
with
hydraulic
oil.
WARNING
:
The
warnings,
cautions
and
instructions
discussed
in
this
instruction
manual
cannot
cover
all
possible
conditions
and
situations
that
may
occur.
It
must
be
understood
by
the
operator
that
common
sense
and
caution
are
factors
which
cannot
be
built
into
this
product,
but
must
be
supplied
by
the
operator.
CAUTION1:
ALWAYS ensure the mechanical safety locks are engaged parking. Never remove safety
related components from the lift. Do not use if safety related components are damaged or missing.
C
AUTION2: Failure installation and operation or any improper modification could result in hurts or even
death of operators. Please do read and understand this manual thoroughly and operate as it required.